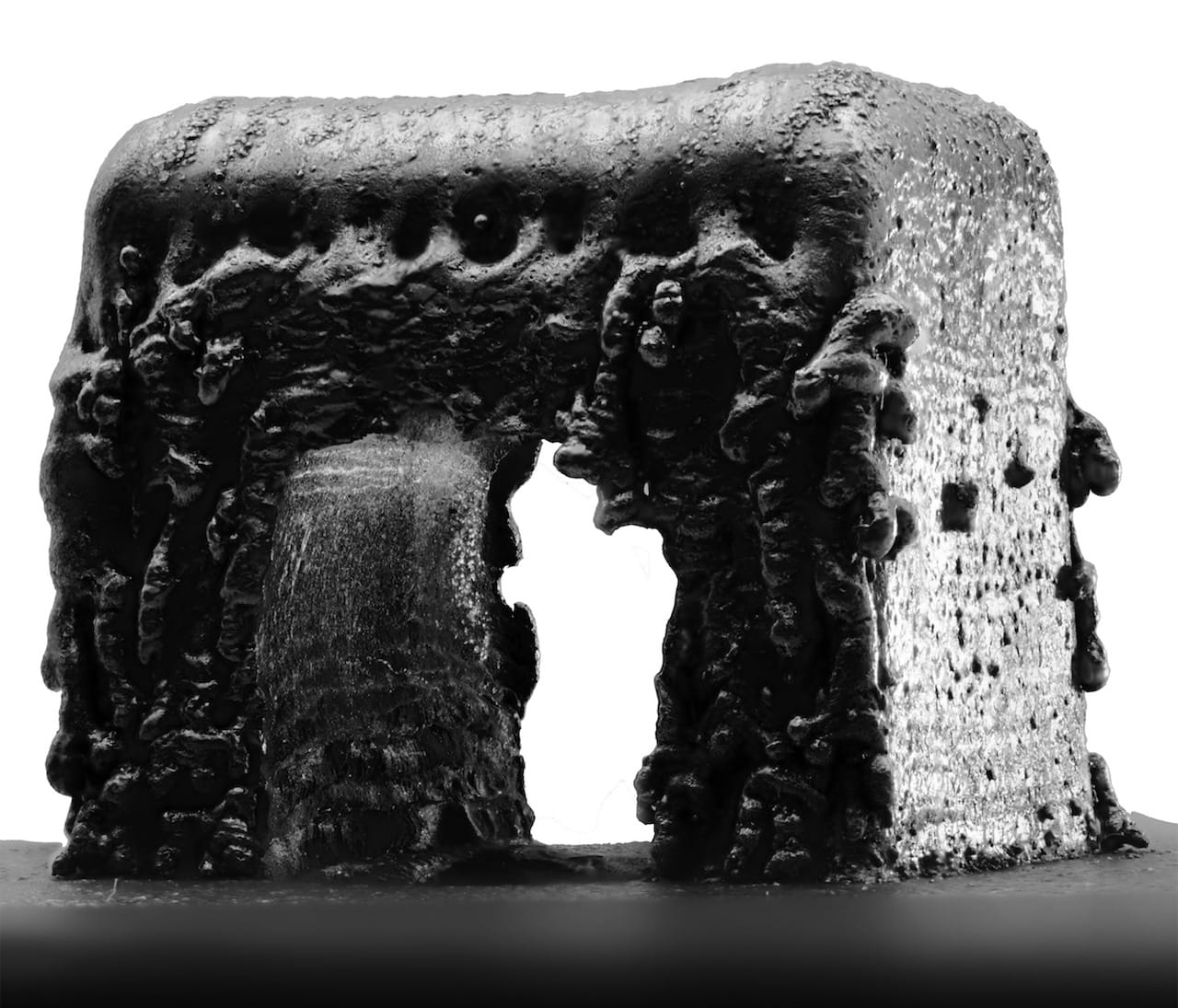
Researchers at Arizona State University have developed a very interesting method of providing dissolvable supports for 3D metal prints.
Somehow I missed this paper from last fall, where Owen J. Hildreth and team describe a process for using dissolvable metal supports. While dissolvable supports have long been used in plastic 3D printing from hobby to commercial levels of equipment, no one has previously done the same with metal printing systems.
Itās a powerful idea, because it could potentially reduce the effort of performing 3D metal printing significantly, which today requires a very significant amount of work to complete prints.
3D metal prints are typically printed on thick (and rather heavy) metal plates such as those pictured above. The metal prints are literally bonded – very strongly – to these plates and must be carefully cut off.
To do the cutting, most shops use expensive wire cutting equipment that precisely slices the prints off. These Wire EDM machines then ācleanā the bed by slicing off the excess material, leaving a flat surface on the plate for the next print.
However, the process results in a flat bottom to the print, which is very often not the desired shape. You must then carefully machine off the excess metal to expose the true bottom of the print. This machining is best done by multi-axis CNC equipment, which, you might guess, is quite expensive.
If you havenāt noticed the pattern here yet, Iāll spell it out: because of inadequate support structures for 3D metal printing, most shops must invest in Wire EDM and Multi-axis CNC machines, and the labor to operate them, in order to complete 3D metal prints.
Thatās likely to significantly add to the cost of 3D metal printing.
Now if this new research works, the operations could be significantly simplified and made less expensive. But how does it work? They explain:
We demonstrate that sacrificial metal supports can be fabricated by taking advantage of differences in the chemical and electrochemical stability between different metals. As a demonstration, a stainless steel bridged structure with a 90° overhang was fabricated using a carbon steel sacrificial support that was later removed through electrochemical etching in 41āwt.% nitric acid with bubbling O2.
Itās not exactly like using water to dissolve soluble PVA plastic supports, but it certainly could be fantastically less expensive – and faster – than traditional 3D metal printing approaches. They say:
No machining, grinding, or finishing operations were required to remove the metallic supports using this approach.
The process appears to work, but obviously has not yet been developed into a product or method that can be integrated into an existing system, and it’s likely further refinements would be required to completely eliminate post-printing CNC milling. However, the potential savings through this concept are so dramatic I am certain it will appear on the market in due course.
Via Liebert