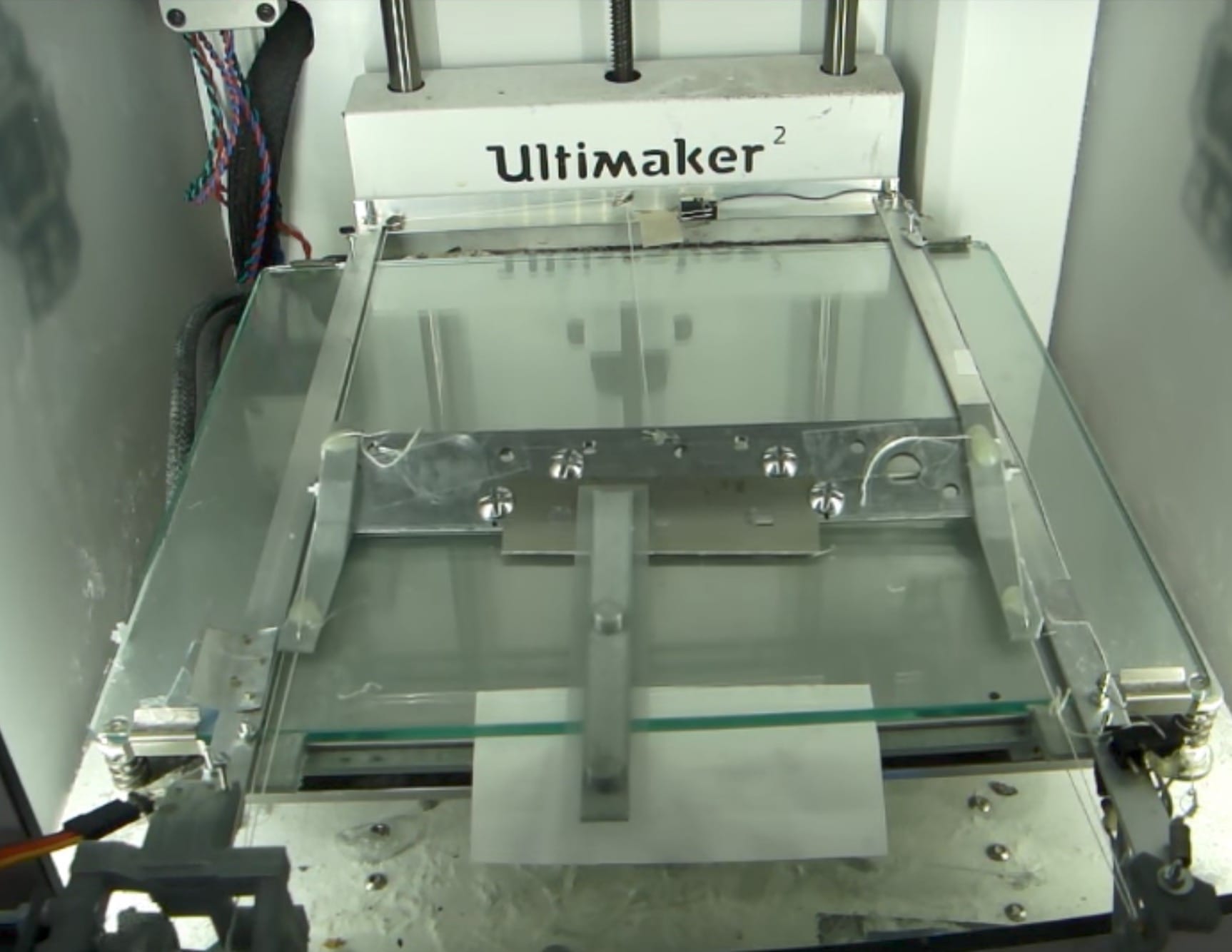
Thingiverse constributor Aad van der Geest has proposed – and prototyped – a 3D printer add-on for continuous 3D printing.
Continuous 3D printing is a goal for many, as it would provide a way to transform an otherwise single-print 3D printer into a kind of factory that can pump out larger quantities of objects while unattended.
I had a wonderful, but temporary, experience with MakerBot’s very early “continuous build platform”, which offered a kind of conveyor belt systems that rolled prints right off the bed when finished. I recall one particular sequence in which my primitive desktop MakerBot was able to run off around 100 small prints without interruption, filling a small basket under the device.
But then the “CBP” failed because the plastic conveyor belt eventually warped, causing an uneven print surface that failed miserably.
Since those early days, there have been several attempts at ways to convert single-use 3D printers into factory systems. The primary issue is the ability to remove the completed prints before the next print could commence. This is done manually in almost all cases.
You may ask about the supply of filament, and that is indeed also a concern for continuous 3D printing: you can’t print if you run out of filament. However, today’s 1kg spools can print quite a large number of small parts, and if that’s not enough, you can simply buy larger spools. I’ve seen spools as large as 8kg, which should be sufficient to run any 3D printer for many, many days.
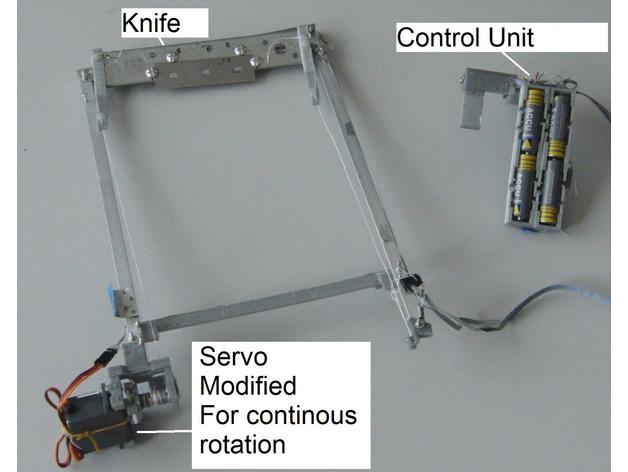
Back to the plate-clearing problem. Netherlands-based van der Geest devised what I call a “bulldozer” solution: a servo motor draws a strong blade across the print surface to free and slide prints out the front of the machine.
He’s even posted the entire design on Thingiverse so you can try it out yourself. Keep in mind, however, that the design is specific to the Ultimaker models, and likely requires some adjustment for installation on other devices.
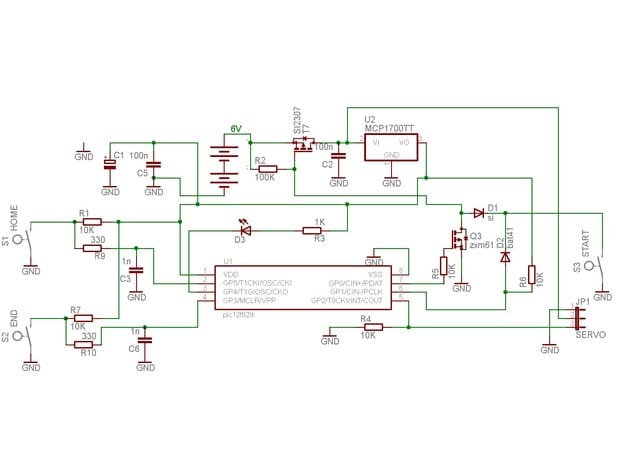
The system works because in the Ultimaker, the glass plate mostly releases PLA parts when it cools sufficiently. In fact, if you listen very closely you can hear a slight crack when the part snaps free from the cooling glass plate. These relatively loose parts are easily pushed off the platform.
I’ve seen other approaches where the moving extruder itself is used to push objects off the bed, but I prefer this approach because there is less danger of damaging the extruder. You can push the entire plate’s prints off at once.
To implement this, you’ll need to add some specific GCODE to the end of your print. Part of this code would wait until cooling is achieved, and then the extruder is moved to a specific corner of the print area to trigger a micro switch that activates the blade.
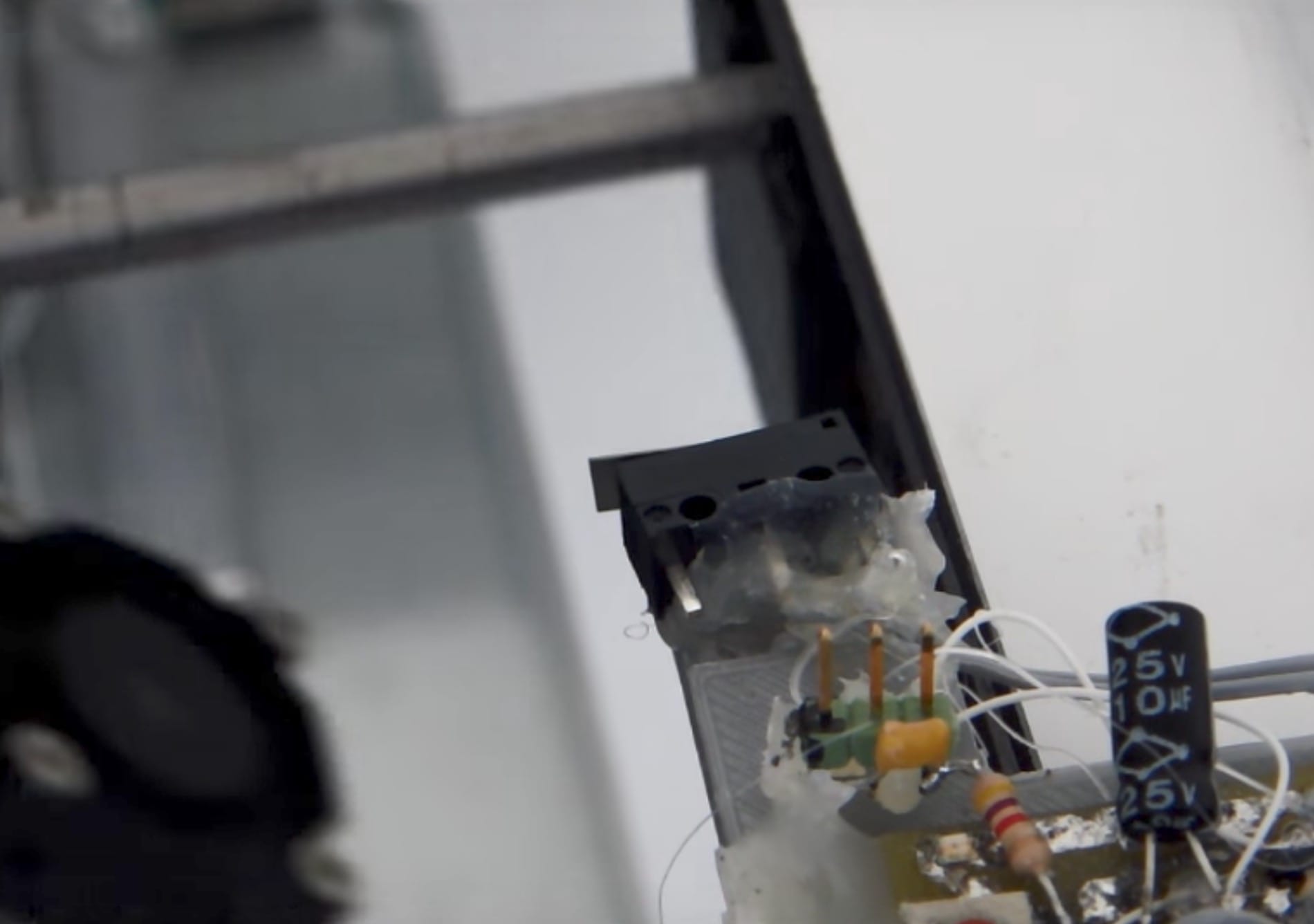
In this way you don’t need to perform any surgery on the 3D printer itself; you can simply drop the “automatic part unloader” onto the print bed and go.
This system may work well for those desktop 3D printers that are able to provide “loose” prints by cooling, but would not work very well for systems in which the print is held secure, as happens on many third party adhesion systems.
If you’d like to give this a try, hit the Thingiverse link.
Via Thingiverse