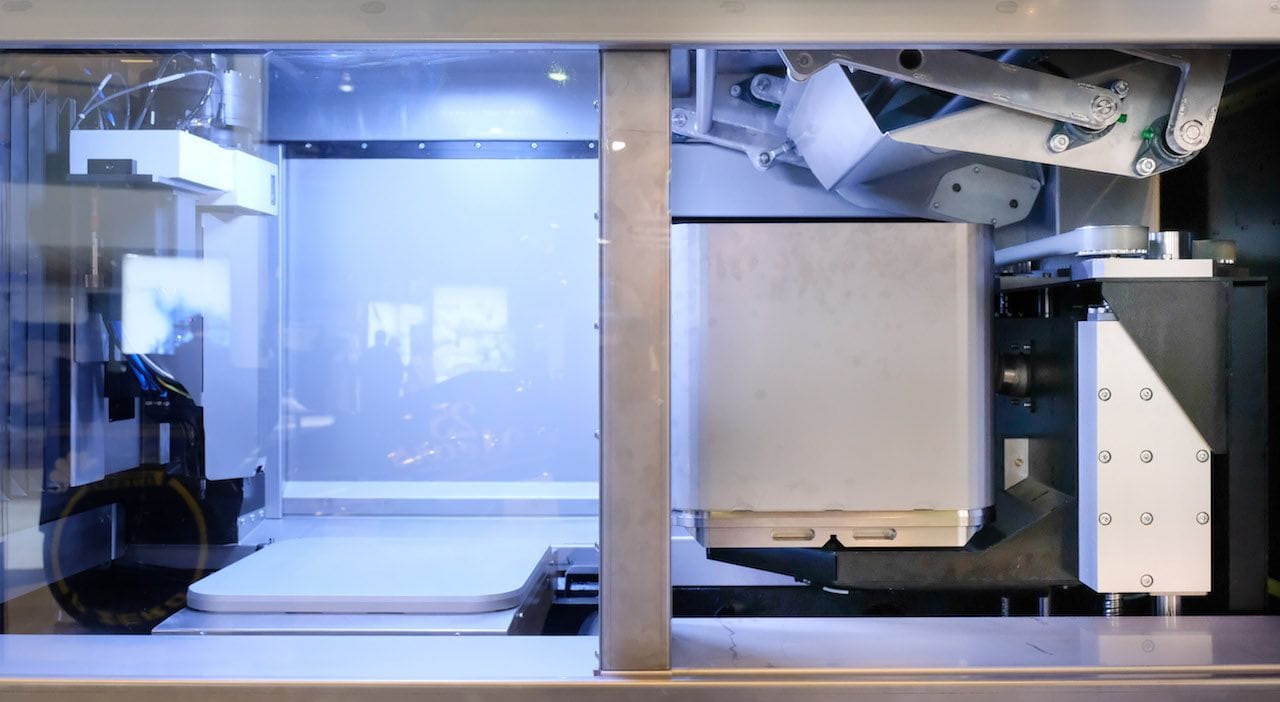
An interesting announcement from Additive Industries this week shows their continuing commitment to addressing the automation needs of metal manufacturers.
Unlike almost all of their competitors, automation has been the prime focus of Additive Industries, a 3D metal printer manufacturer from Netherlands. In most cases, competitive 3D metal printing equipment is simply āthe printerā, and the operators are left to handle all other aspects of the production process by their own design.
In a practical view, 3D metal printing itself is only one step of many that must be completed to actually receive a completed metal part. Here are some of the typical steps that must be executed in sequence:
- Prepare the metal powder for printing
- Perform the actual 3D print
- Post-printing heat treatment to finalize metal crystallization
- Remove print from the build plate
- Clean part from powder
- Other post-processing as required
Many of these steps are actually included in Additive Industriesā system, which operates much like an assembly line: the metal plate moves from module to module to perform these activities.
But one function was missing, at least until last week, when the company announced their new part removal module.
This new module, which tucks neatly into the modular machine concept, accepts a build plate and tips it over. Once tipped, a powerful saw slices the prints off the build plate.
[For those not familiar with 3D metal printing, the build plate is actually a flat rectangular – and very heavy – piece of metal upon which the print is applied. The completed print is essentially a metal plate with the printed parts welded on top of it. Plates can then be shaved down flat for reuse, at least until they are too thin.]
This new module from Additive Industries eliminates the need for separate acquisition of expensive wire EDM machines that are typically used to slice prints off build plates, but more importantly removes the manual labor in doing so. Remember that plates are quite hot when prints complete, and in some cases you must wait for cool down before a worker can move them to the separate machine. In the new Additive Industries concept, things can happen much faster, and in an automated way.
Cut-off prints are collected in a basket at the bottom of the new module, where they can then take part in additional post-printing steps.
This new module takes Additive Industriesā MetalFAB 1 to another level of automation that should attract more manufacturers who are seeking economical ways to achieve 3D printing. In most cases, such companies balk at the cost of setting up a complex 3D metal printing process, particularly when they are not familiar with all the steps required and how to do them properly. Additive Industries reduces those concerns considerably with the MetalFAB 1.