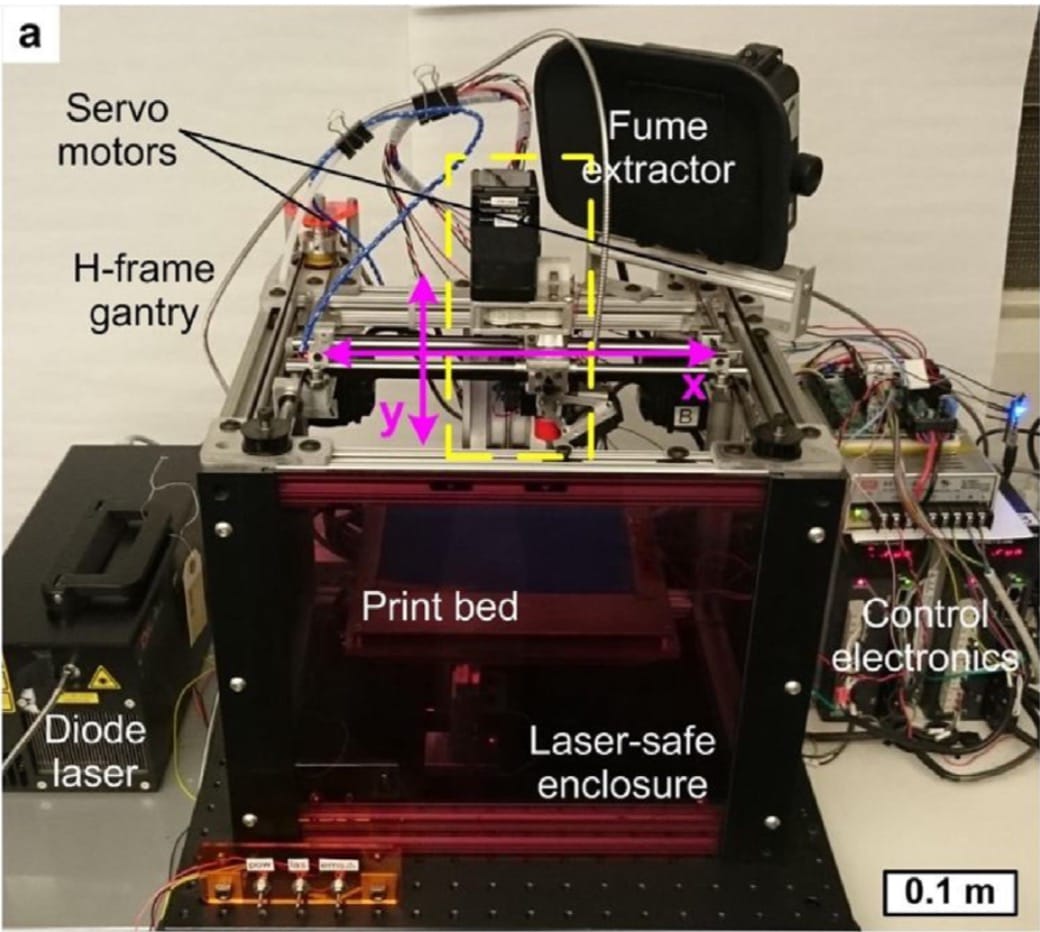
Researchers at MIT have devised a method of dramatically speeding up plastic extrusion 3D printing, but is it enough to make a difference?
The researchers analyzed the fundamental properties of extrusion-based 3D printers and determined several ways to overcome the notorious slow speed of that particular 3D printing technology. Typical 3D printers of today might take hours to 3D print a fist-sized object, limiting the utility of the technology in many ways.
But their project is quite different from other speedup attempts weâve seen in the past. Most other speedy 3D printer ventures have undertaken these approaches:
- Larger nozzles to extrude more material at a time, but at the cost of resolution
- Pellet-based extruders to overcome the mechanical limitations of pushing thin filament
- Beefy heating elements or longer heating paths on hot ends to enable more heat to be applied to moving thermoplastic
- Motion system enhancements through speedy real-time onboard processors
And while each of these approaches has indeed delivered some speed advantages in their respective machines, none has yet to âtake overâ the market.
Now MIT has delivered a new concept, called âFastFFFâ, which combines several new advances into a system that seemingly can be much faster than any single approach. Itâs quite interesting what theyâve done.
Their analysis shows the speed is governed by three foundational elements:
- The speed at which heat can be applied to thermoplastic;
- The force that can be applied to moving plastic into the system;
- The speed at which the extruder can be accurately moved around the build platform.
The new system design attacks all of these factors directly.
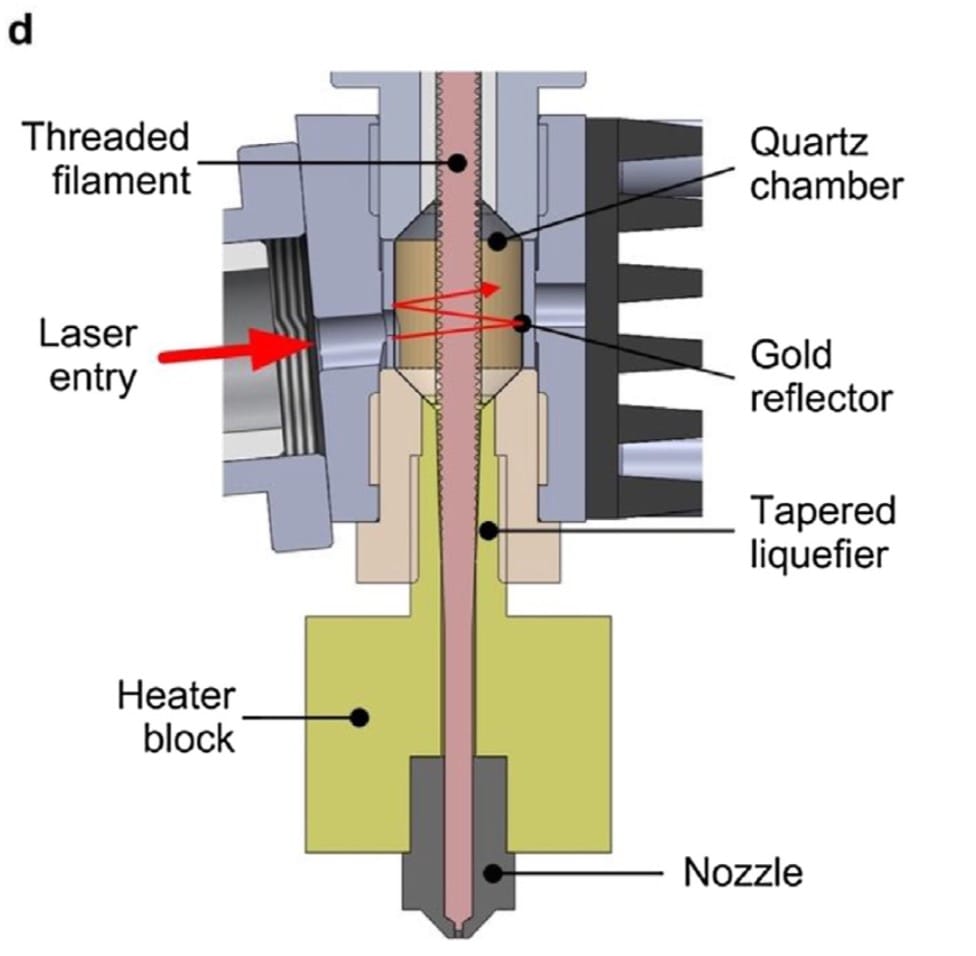
First, theyâve developed a unique way to apply more force to the incoming plastic filament. Theyâve changed from a standard âsmoothâ filament to a threaded filament. Yes, this is a filament with threads on its exterior. It appears they cut a standard filament with a die system to form triangular threads. The thread design is optimized to provide the maximum amount of force.
Once formed they use the threads with a ânut feedâ approach. Essentially the nut exactly fits the threads of the incoming filament and needs only turn to push the filament with great force. While common 3D printers use a pinch wheel approach, this is far stronger – but you need to have a specially prepared filament.
The second system development is a way to increase the speed of heating. This is done with a two-stage approach. First, the filament travels through a zone with a transparent window and reflective chamber. Through this window a 50W near-infrared laser pre-heats the filament. The filament reaches its final softening temperature as it passes through the hot end. The hot end thus needs only raise the temperature slightly instead of a great deal. This is more efficient than other heating approaches that involve very long heating paths.
An interesting twist to this approach is that the frequency of the laser must be matched to the visual properties of the incoming material; differently colored filaments require laser tweaks.
Another twist is that the hot end must be reformed to handle the thread on the incoming filament. Unlike regular smooth filament, the threaded surface wonât properly contact the sides of the hot end unless it is carefully designed to accommodate the threads.
Finally, theyâve redesigned the motion system over an H-frame using servo motors for optimum speed. The big problem is overcoming the momentum on speedy directional changes, but it seems theyâve designed this system to do so.
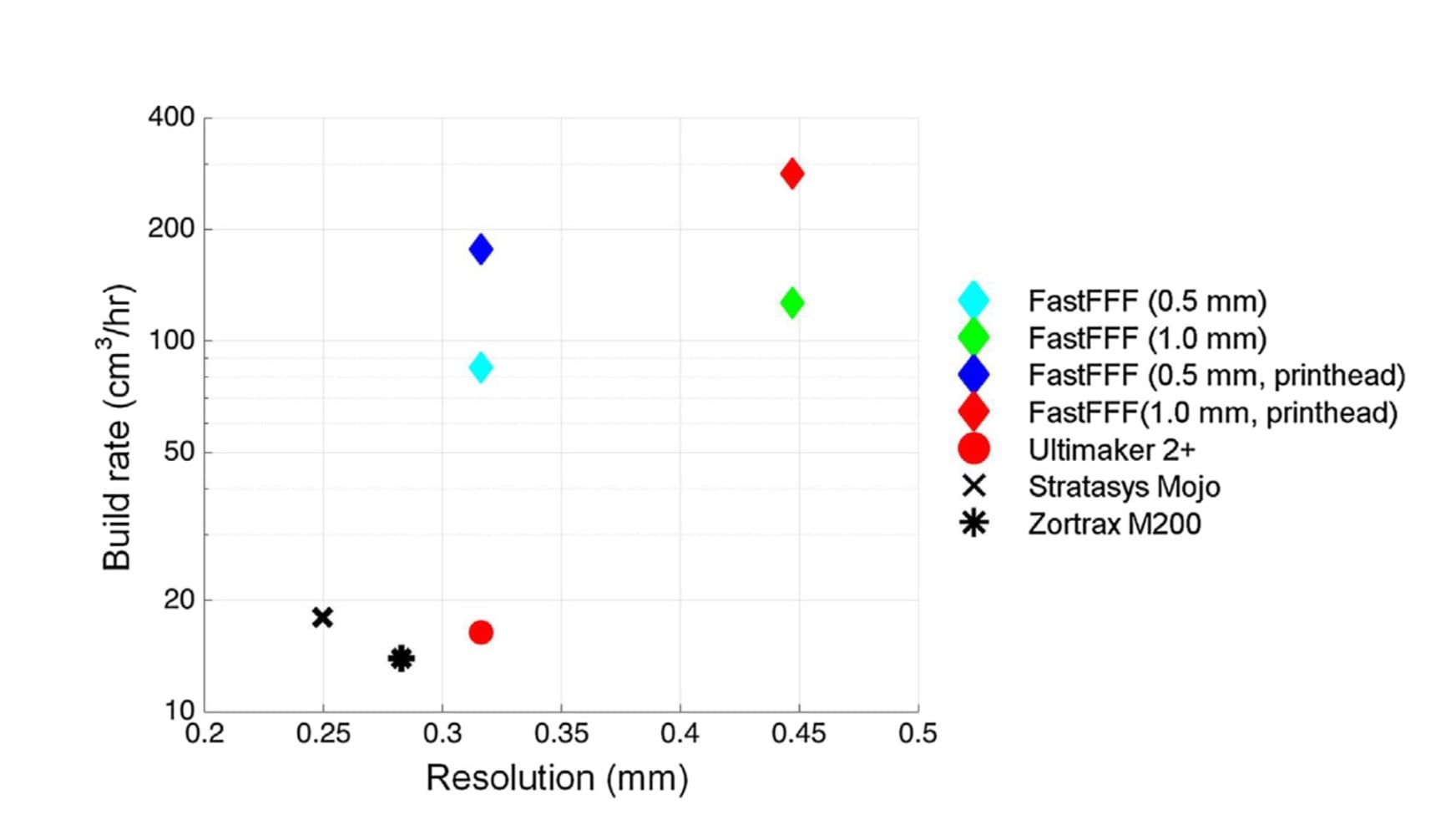
Adding all this together, they say the FastFFF system can deposit – accurately – 282cc per hour, which is around seven times more than conventional systems. There is the possibility of going even higher with refinements to the system and of course on particular geometries that are amenable to the FastFFF process.
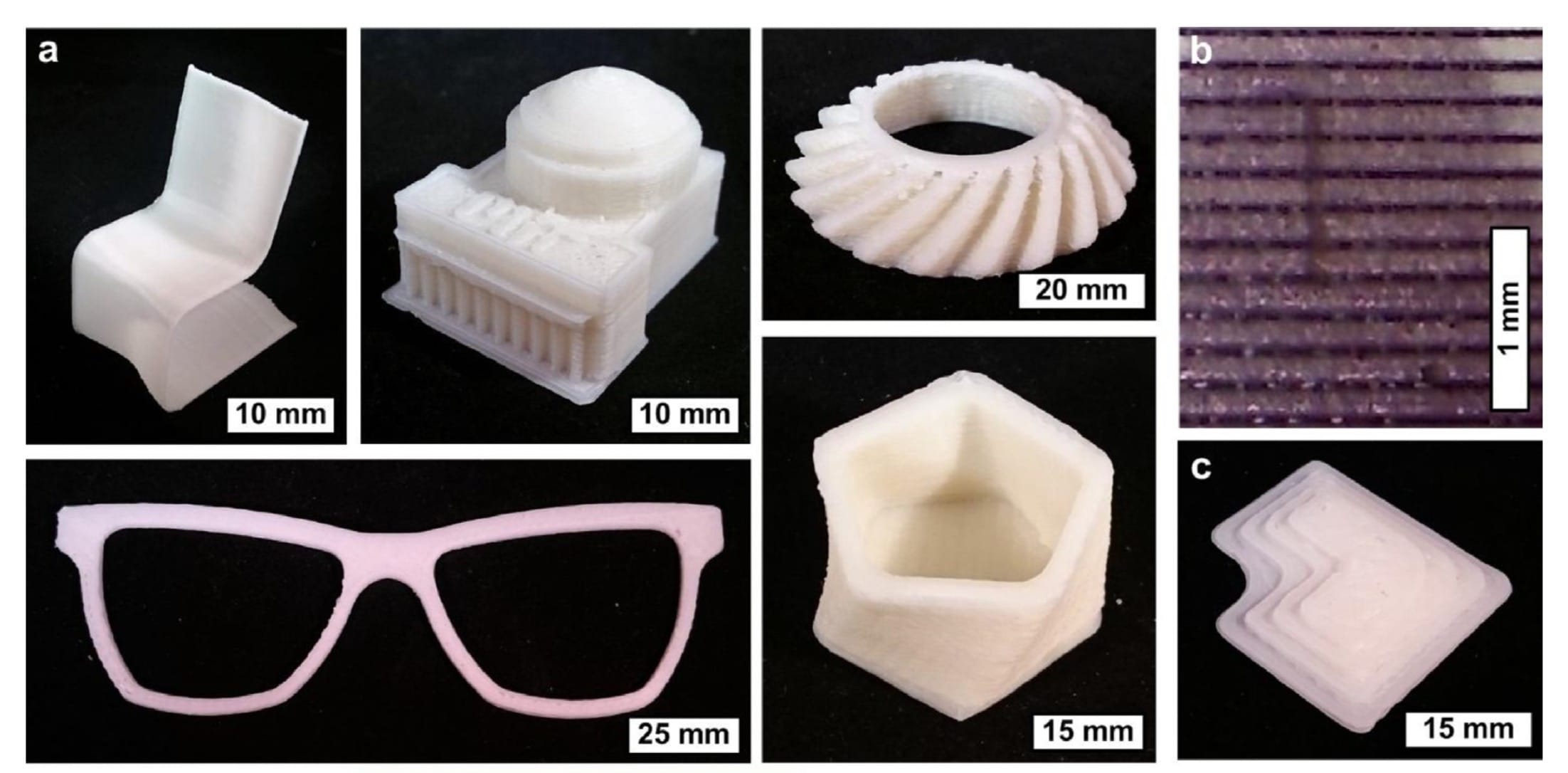
This is research at this point, and certainly not a product. While extremely promising, I am not sure this will be commercially viable for a couple of reasons.
First, the FastFFF system requires specially prepared filament for which there are no sources today. Itâs possible the plastics vendors will begin producing such, but only if there is demand. We have a chicken and egg situation here. In the meantime this specialty filament will be much more expensive and thus limit use.
Second, the FastFFF process is likely to be patented by the inventors and thus limiting it to be developed by only one company – or a few others that license it. This will slow the growth of the process, but in the meantime other speedy 3D printing initiatives may catch up.
Third, the researchers have compared the FastFFF process to some common systems, as shown in this graph. However, there are are other systems that are much speedier than these already available, making the speed advantage not nearly as significant.
Finally, what is the actual benefit of a speed advantage? How much does it really matter, in a practical way, that a large object can be printed in 2 hours rather than 14? The 14 hour print would be left overnight to complete by most companies, making the delay insignificant in practical terms. It may be that extreme speed advantages are only meaningful in certain situations – like very large format 3D printing – and not in general cases, making the market for FastFFF machines a bit smaller than otherwise. To be truly groundshaking, 3D printing must be much faster than even the FastFFF process can achieve.
Regardless of how FastFFF turns out, it is certainly a very interesting development that will surely inspire others to speed up their 3D printers.
Via Science Direct
1 comment
Comments are closed.