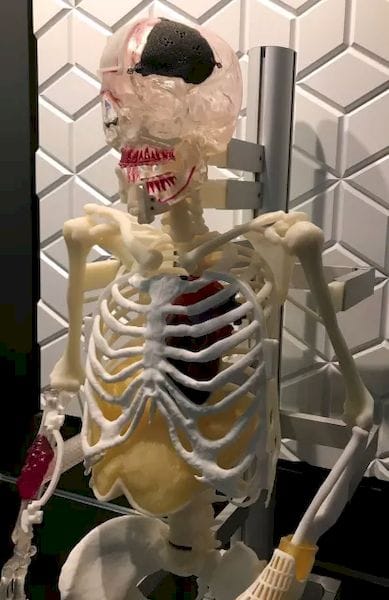
Many companies wish getting a part made was easy as plugging a computer to a 3D printer and pushing a button.
This noble goal may become a reality thanks to 3D Systems, the company best known for its array of 3D printers.
CEO Vyomesh Joshi, with his executives in step at the company’s recent press launch, referred to the “digital workflow,” the idea that a part can exist as bits and bytes all the way from its design to its physical realization.
What Is the Digital Workflow?
The digital workflow is the process a part endures to get made. It is different for different industries. The process can be anything but smooth. A part starts as a CAD part, but is converted to paper drawings, re-digitized as g-code and machined on a milling machine before the finished part can be held in your hand. In a dream digital workflow, the part moves unimpeded by stops, changes and human intervention. If the tortuous process is like a previous century traveler on a journey taken on foot, in a carriage and a ship, the dream digital workflow is like a nonstop flight.
Joshi targets certain industries already more modern and digital than others, those with less stop-and-go in their workflow and computerized for less human intervention, as the ones most able to benefit from his 3D printers. Large-scale manufacturing has enormous potential. A factory that can operate without humans or lights and no messy cutting fluids and metal shavings is a 3D-printer company’s promise. Another industry is health care. A patient’s digital data—the result of CAT scans and MRIs—is perfect for customized replacement parts. It is a market seemingly without cost constraints and one in which 3D Systems has had much success. Jewelry is next.
But as 3D printing is currently a process rather than a push button, a self-made industry has sprung up to assist. In it are experienced practitioners of 3D printing, chiefly among service bureaus that accept design file in CAD or formats and turn them into STL files that the 3D printers can deal with.
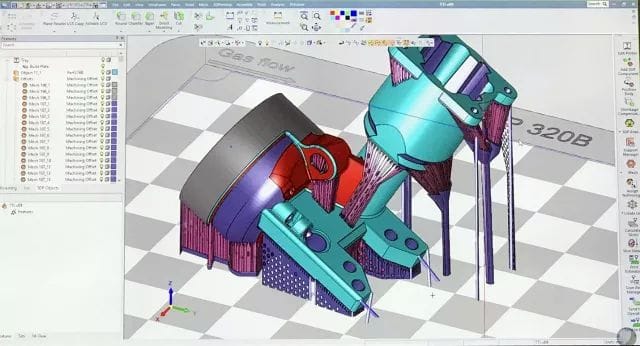
There is software to assist in the transition from CAD to 3D print. 3D Systems has one for metal parts called 3DXpert. First shown to us at IMTS 2016, the company gave us another look at it during the launch event. 3DXpert is provided free with every 3D printer 3D Systems makes, although a few bells and whistles are extra cost items—simulation and advanced lattice control. Some of its notable features follow.
Read more at ENGINEERING.com