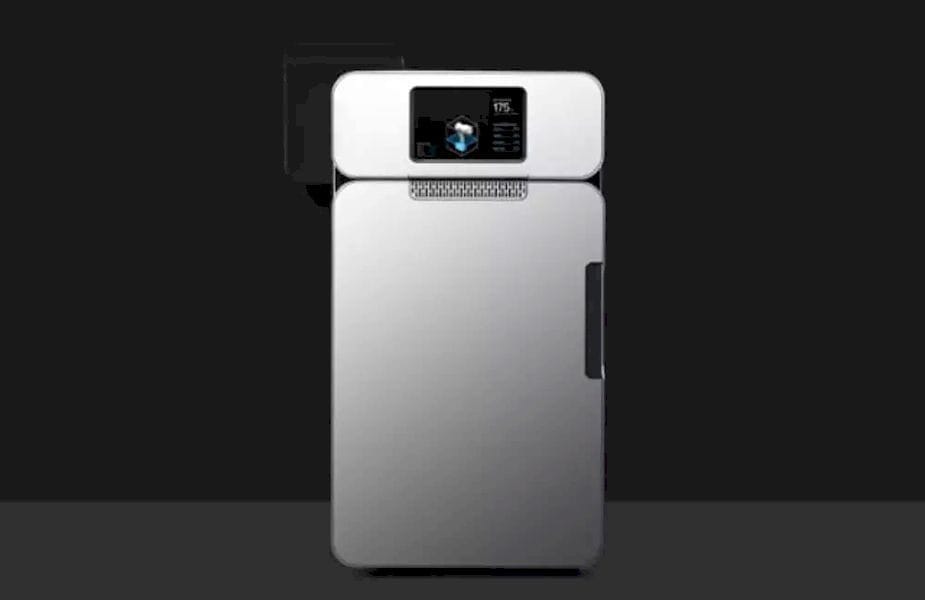
What does 2018 hold for the world?
That may be difficult to predict, but what 2018 holds for 3D printing is a bit easier to grasp since weâve reached out to a number of experts in the industry to get their input on what 2018 looks like for 3D printing.
Increased Adoption
According to Michelle Bockman, global head of 3D printing commercial expansion and development for HP Inc., 3D printing for full-scale manufacturing will see increased adoption. This will take the following shape, according to Bockman: âIndustrial 3D printing will expand to a host of new countries, making it a truly global transformation. Advances in technology will significantly increase the speed, reliability and capability of 3D production. The scale economics of 3D printing will continue to improve, making digital manufacturing more cost-effective for more types of companies in more places. More companies will enter the 3D materials marketplace, helping to drive innovation, lower costs and increase materials diversity. Commercial applications of 3D printing will become more defined across major industriesâautomotive, medical, aerospace, consumer goods, heavy industryâmaking the digital industrial revolution a growing part of our everyday lives.â
Scott Sevcik, VP of Manufacturing Solutions at Stratasys, echoed this point, with a specific emphasis on aerospace. “Looking into 2018, we’ll definitely see the acceleration of production part adoption in aerospace. Major OEMs have already industrialized FDM for interior applications – and this adoption is expanding both upstream and downstream,” Sevcik said. “This is seen as suppliers expand use of 3D printing for efficient, low volume and custom production – and as airlines and MROs leverage the technology for supply chain flexibility. You can already see that standards are currently being developed for industry-leading technologies and fused deposition modeling (FDM), while new simulation and analysis tools are coming online to aid designers in additive designs. As the year progresses, we’ll see low-volume automotive catching up to aerospace with more and more parts in vehicles as well as broad adoption for Rapid Tooling on the automotive factory floor.”
Greg Mark, CEO of Markforged, reinforced the practical application of 3D printing technology, emphasizing its shift away from prototyping and towards end-use parts. In other words, the hype associated with 3D printing over the past few years is now coming to fruition. Markforged is known both for its carbon fiber and metal 3D printing technology.
âNow, weâre finally living up to the promise and printing high-strength parts for real-world use cases,â Mark said. âWith Markforged printers, companies are able to print carbon fiberâreinforced composites that are strong enough for the harshest applications, and metal 3D printing just got an order of magnitude more affordable,â he added. âCombined, these innovations dramatically expand the value proposition of 3D printing and are driving triple-digit growth fueled by rapid return on investment. Markforged customers typically see three-month return on investments for carbon fiber printers. The payback period is so fast that 31 percent of customers buy a second printer within the first year.â
Vice President of Advanced Application Development at 3D Systems Patrick Dunne also believes that 3D printing will see increased adoption. âIn 2018, we will see businesses of all profiles across industries move toward deeper adoption of additive manufacturing (AM),â Dunne said. âThe technology will drive small businesses in the sense that they can up-level their capabilities to those of a more established, mature business; this may introduce new levels of competition and new business models and market opportunity. Similarly, large companies will engage AM technologies earlier in the process, from the design phase, as capabilities to support the entire end-to-end workflow mature.â
3D printing wonât be isolated to niche applications, according to Dunne. Instead, it will become a standard tool for âmany existing and novel production streams.â
Improved Design
Duann Scott, responsible for Business Development and Strategy for Additive Manufacturing at Autodesk, saw major trends in design occurring next year. “In 2018, we will start to see people really understand that design for additive manufacturing is key to it transforming from a very small part of manufacturing, to a substantial part of the economy,” Scott said. “Comparing an existing traditionally manufactured part to an AM replica is rarely going to be a financial win, but consolidating an entire assembly into a single AM part can massively reduce the manufacturing cost, completely compress the supply chain and improve the performance within a single design change. Once engineers (and their managers) start to realize this in the year ahead, we expect to see massive investment in design for AM.”
An important contribution to improvements in design for 3D printing may be entirely new design processes, such as generative design. This makes it possible to enter specific parameters for a part, such as reduced weight, and allow software to alter a part’s topology to meet those requirements automatically. “We can speed up this education process through Generative Design software, where we take a sub-assembly out of an existing design, define the constraints and engineering requirements, and let the Generative Design tool help the engineer explore potential solutions to replace the sub-assembly with a single part,” Scott said.
New and Improved Metal 3D Printing
As mentioned in the introduction, metal 3D printing is developing rapidly, both in terms of lowering costs and increased adoption. Bart Van der Schueren, chief technology officer of Materialise, a 3D printing service provider and software developer, echoed as much in a statement to ENGINEERING.com.
âMetal is booming. We know that metal 3D printing will never replace traditional manufacturingâbut as a complimentary manufacturing technology, its position is becoming increasingly important,â Van der Schueren relayed.âMetal 3D printing will become more and more of a necessity when solving specific manufacturing challenges and creating customized, complex end-use products. To that end, we acquired AC Tech this year, a German manufacturing company specialized in highly complex metal prototype casting. With their expertise in metal and our knowledge of 3D printing, we are prepared to bring metal 3D printing to the next level.â
Metal 3D printing will see improvement both in terms of new technologies, as well as improvements to established ones. For instance, 3D Systems recently announced the expansion of its metal 3D printing line with a large, more automated system.
Dunne spoke to this development, saying, âA broader range of metals will be optimized for direct metal printing. The conversion of raw materials into finished production products will see significant growth in 2018. Hardware will evolve in parallel to become more capable from both a part-size perspective as well as process control, with solutions like 3D Systemsâ recently announced DMP 8500. This machine can print a 500-mm XYZ, the largest âseamlessâ part capability in the industry. This class of development will solidify the position of the technology as mainstream in industries like healthcare and aerospace. In the latter, for example, design optimization of parts expressed by AM to create new geometries has the potential to save thousands of dollars in fuel consumption alone, just by improving the strength-to-weight ratios.â
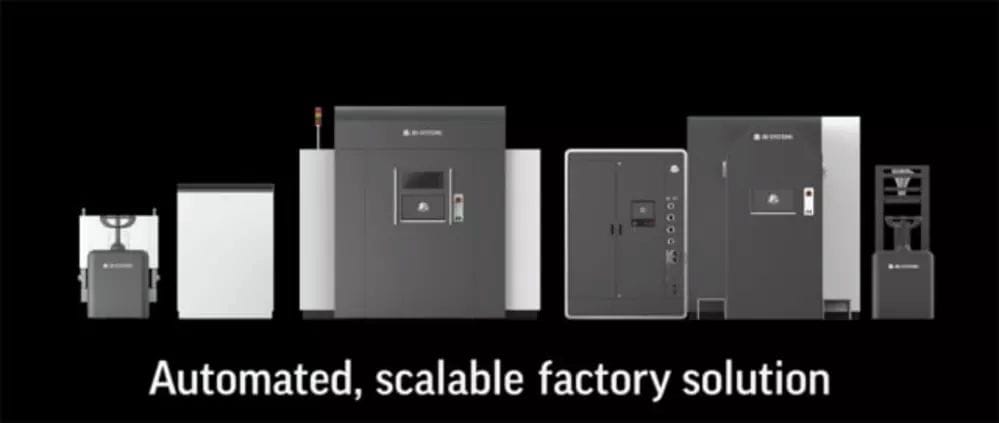
Markforged, on the other hand, is one of the innovators that is introducing new metal 3D printing processes, having released a technology capable of producing metal, 3D-printed parts with greater ease of use at a lower cost than previously possible. The Metal X 3D printer prints rods of metal powder bound together with thermoplastic, creating parts in a method similar to fused deposition modeling. The binding material of the âgreenâ part is then washed away before the subsequent âbrownâ part is placed into a sintering furnace to create a nearly fully dense metal part.
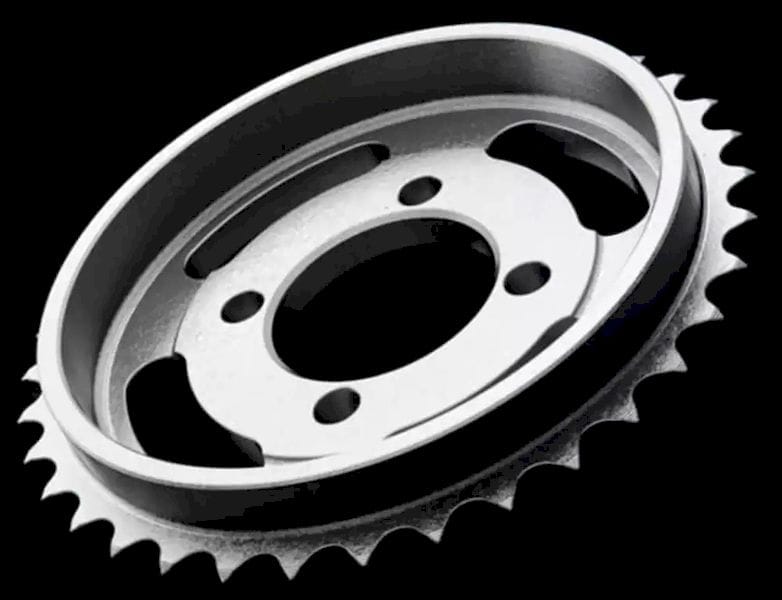
âMechanical engineering is entering a renaissance. 2018 is the year metal printing becomes a viable option for mainstream designers and engineers,â Mark told us. âOur new Metal X [3D printer] is 10 times lower cost than the current generation of metal printers. But thatâs only half of the story. Itâs also 10 times easier to use. The intersection of low cost and ease of use will drive a wave of adoption in the industry.â
Mark added, âMechanical engineers are going to become considerably more efficient. There are 2 million mechanical engineers who can design a part in hours, but have been waiting four to six weeks to get that part out of metal. Theyâre about to have next-day access, accelerating innovation.â
With its low-cost system, Markforged reintroduced the world to indirect metal 3D printing, already available with such processes as lost wax casting. Dunne, at 3D Systems, pointed to a growth in plastics and wax used for casting purposes. âIn 2017, there was a widespread adoption of waxes in ultra-high-fidelity direct inkjet of wax in the jewelry industry,â Dunne said. âThis will continue into the next year, while in parallel, we will see a marked expansion of the use of waxes within industrial investment casting workflows. We can expect that AM will become a standard pattern source for creating metal castings.â
While companies like Markforged are aiming to make metal 3D printing less expensive and more user-friendly through the development of new metal 3D printing processes, Oak Ridge National Laboratory (ORNL) is improving existing metal 3D printing techniques in a variety of ways. The lab is also aiming to blow up the process to even larger scales.
The labâs Manufacturing Demonstration Facility (MDF) is a leader in early-stage research of new 3D printing technologiesâmost notably the large-scale Big Area Additive Manufacturing (BAAM) carbon fiber-polymer 3D printerâand it has already begun work on metal. The MDFâs representatives told ENGINEERING.com that, in 2018, the lab will focus on developing âlarge-scale metal manufacturing through modeling, simulation, characterization and residual stressâ in 2018. âResearch will increase process scale and deposition rates, making new tailored materials available and applying data-driven analysis for part qualification and certification,â the lab relayed.
Read more at ENGINEERING.com