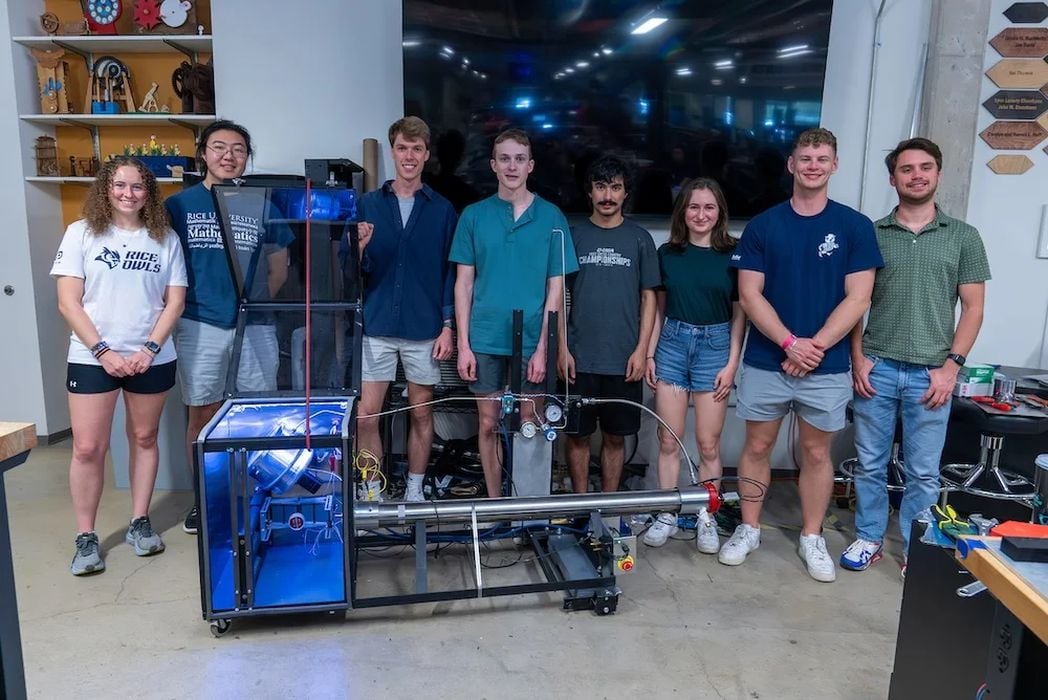
Students at Rice University have developed an incredibly inexpensive metal 3D printer prototype.
The problem they were concerned about is the rather expensive cost of metal 3D printing. Typically this is done today with either LPBF systems requiring extensive environmental setups, or WAAM systems requiring expensive robotic arms.
One of the key barriers to the widespread adoption of metal 3D printing is the sheer cost of the process. Because of this the technology has largely been limited to industries where parts are expected to be pricey, such as aerospace or healthcare.
The studentās approach is to use a variation of cold-spray technology. While most metal 3D printers use extreme heat to melt metal particles or wire, it is also possible to fuse particles together using kinetic energy.
If particles of the same material strike each other at extreme velocities, then the molecules will be close enough to bond, just as they would in a chunk of metal.
This approach hasnāt been widely used in 3D printing, with the only major example being SPEE3Dās supersonic system that blasts particles at high velocity to quickly form metal 3D printed parts. The company doesnāt seem to publish the particle velocity, but apparently itās sufficient to bond stainless steel particles with their Phaser nozzle.
Meanwhile, the students developed a system that offers incredibly high velocities.
They explained that a reservoir of nitrogen is heated, which greatly raises the pressure of the gas. This gas is routed through a parabolic nozzle, which accelerates the gas to Mach 3! This propels copper particles up to 550m/s, or about 2000km/hr, far more than just supersonic.
The best part of the student design is the cost. For approximately US$5,000 they were able to put together their prototype. Thatās quite inexpensive, and almost in the range of hobbyists.
However, itās a prototype and not a fully developed 3D printer. The technology will have to be commercialized into a real product that customers can purchase.
The approach seems quite promising, but thereās one thing Iām wondering about: the nitrogen would have a fixed capacity, so printing would stop when the pressure lowers beyond a threshold.
What is that threshold? How long could a print job last? Would you need a really big nitrogen setup to print larger items? Could the nitrogen be recycled?
There are many questions here, in spite of the success of the project. Iām hoping entrepreneurs take up this technology and attempt to make it into a real 3D printer.
Via Rice University