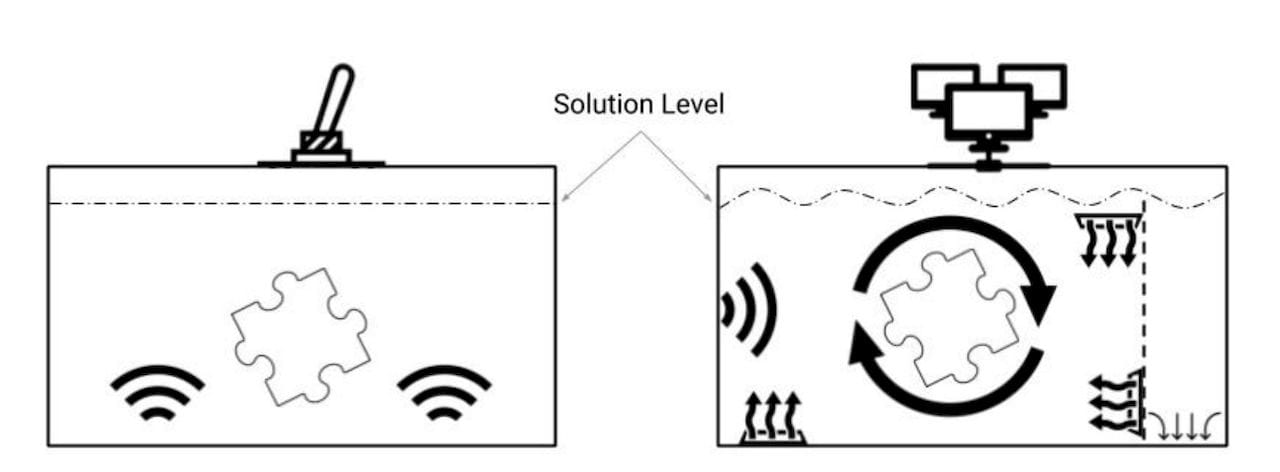
I’m reading a white paper from PostProcess that’s discussing the complexities of removing dissolvable support material from fresh 3D prints.
While their white paper focuses on the use of Stratasys’ PolyJet process and removal of that method’s support material, the points they make in the paper are certainly applicable to most dissolvable support removal situations.
Dissolvable support material is highly desired because of the relative simplicity of use and the ability to handle any geometries. It’s quite possible to design a 3D model that requires support in areas where it cannot be mechanically removed. This problem effectively prevents 3D printing of these geometries until a solution is found. Even less complex geometries have problems with non-dissolvable supports, as delicate structures could be broken or bent during manual removal.
The solution has been dissolvable support material. The idea is so incredibly simple: print with the dissolvable support in the usual manner. In fact, this support material acts entirely normal in every respect until you want to remove it.
When printing is complete you dunk the print into a tub of water, where the supports dissolve and you are left with a perfect 3D print, regardless of geometry, hooray!
But it’s most definitely not at all like that in real life. Usually you will wait hours for the process to complete, sometimes longer than it took to print the object in the first place, and that wasn’t quick either. The result is a very lengthy process, and that is not conducive to effective continuous 3D printing operations.
PostProcess is a company that’s dedicated to fixing that problem, and it seems that they’ve done considerable research in this area. Dropping an object into a pail of water is simply not going to be effective, or even work in many cases. Their white paper explains the many issues related to efficient handling of dissolvable support material, including:
- Including the appropriate detergent agents in the water to speed the chemical reactions of support breakdown
- Maintaining the optimum temperature for these chemical reactions to take place
- Maintaining an adequate flow of fluid around the object to keep chemical reactions occurring rapidly
- Including an abrasive material in the water to aid breaking down the support material
- Floating the part to keep it in an area of the tank that provides optimum dissolving action
- Ensuring the entire object is uniformly exposed to these conditions
- Doing all this in an automated way to ensure consistency between prints
PostProcess just happens to produce machines that do most of these functions. If your operation involves causal 3D printing, then perhaps this extreme optimization isn’t for you.
But if you are operating a 3D printing workshop whose goal is efficiency, equipment of this type should certainly be considered. It might be possible to lower labor costs through automation, but at the same time improve part quality and consistency.
You might want to read their white paper, found at this link.
Via PostProcess