![Christine Furstoss, Vice President and Chief Technology Officer, GE Additive at formnext 2018 [Image: Fabbaloo]](https://fabbaloo.com/wp-content/uploads/2020/05/image-asset_img_5eb0a23f2c81b.jpg)
Additive manufacturing is industrializing, but what does that mean?
GE Additive VP and CTO Christine Furstoss isn’t afraid to pull back the curtain, and our conversation at formnext was refreshingly straightforward. For a young technology to fit into existing workflows and build new ways of making, certain realities need to be faced — not least among them what those realities really mean.
“As we go through industrialization, it’s so important with use cases out there to understand how additive manufacturing fits; how do we now step back to understand what does industrialization truly mean?” she asked.
“When you’re making castings and forgings, no one expects it to be right the first time, but there is more expectation with that for additive. We need to get analytics, to get information to customers for reliability, for repeatability, and integrate that into our offerings.”
Furstoss well understands the need for clearly communicated results; her background is in metallurgy, and she has been working in primarily engineering and supply chain departments at GE for the last three decades. Moving into the additive arena sees her leveraging her years of experience into a fast-growing field with the need for grounded perspective.
“The additive ecosystem is not talked about often enough; we need to understand machines, software, and post-processing and look at them all,” she continued. “Our job is to help our customers understand how and why additive is the next step in their journey — is it to address existing pain points, to look at distributed manufacturing, to explore new materials? There are so many business models, which is both a challenge and an opportunity.”
The key to addressing these challenges, and to seeing them as opportunities, lies in understanding the needs of each individual customer and unique use case. Furstoss pointed to the many launches during formnext, as software continues to gear more toward customer designs and how to meet their needs through printing and post-processing.
“2019 is the year of customer solutions,” Furstoss said, looking ahead. “We will take this complete ecosystem and take it to the customer for the solutions they need. We want customers to think of GE Additive as the industrialization company.”
That means focusing work at Customer Experience Centers for direct work with users so they have that confidence to grow, she added.
“For the first time, we’re looking at a technology with desirable function and geometries at the same time. In subtractive, you start with given material properties and work from there. Now you’re looking at how to view function with geometry and have the material properties tailored, releasing the constraints on both. We’re really looking at the material, which is why it’s so important we have powders in our portfolio,” she noted.
That portfolio is relatively expansive, as GE Additive has incorporated hardware, software, and material solutions into its offerings.
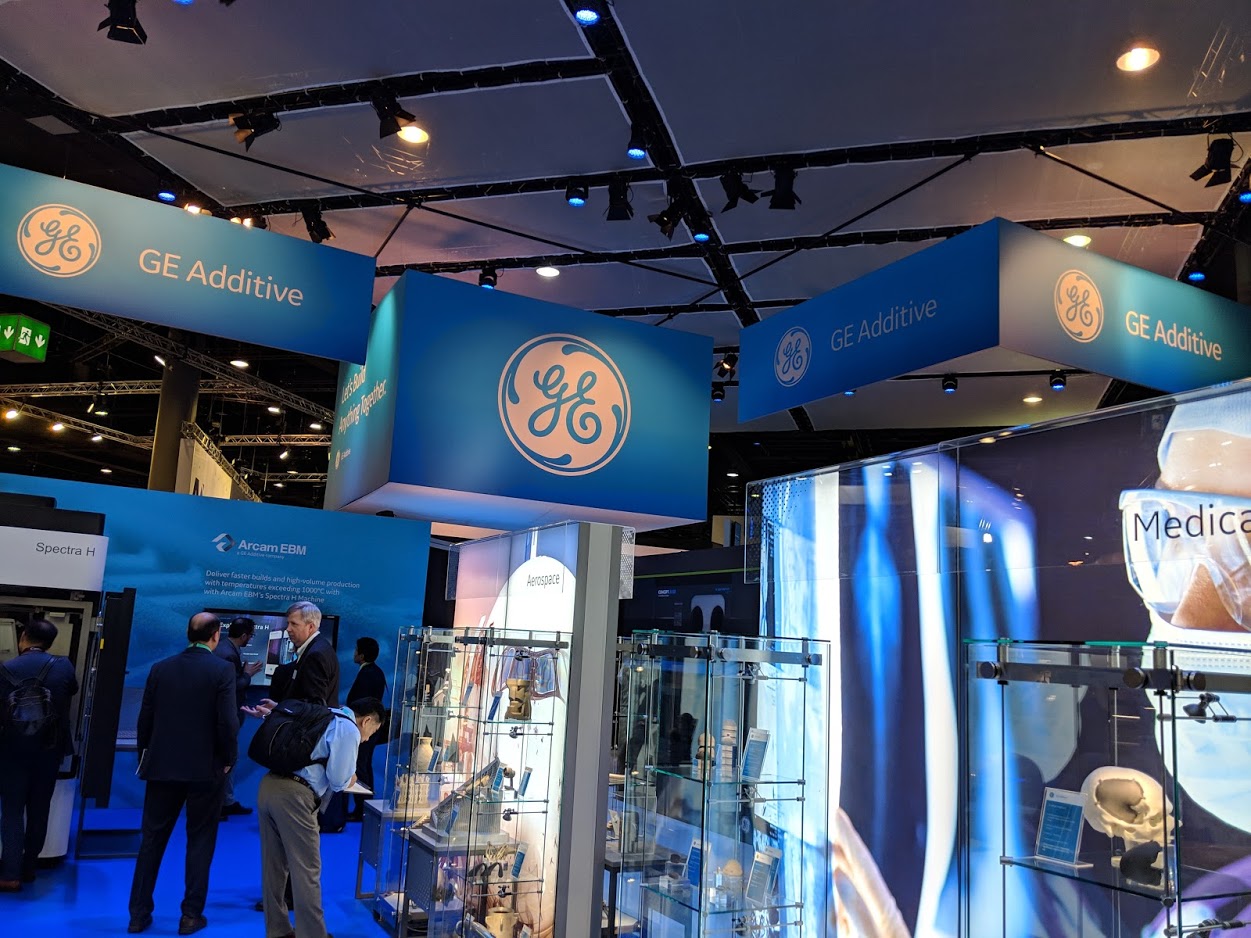
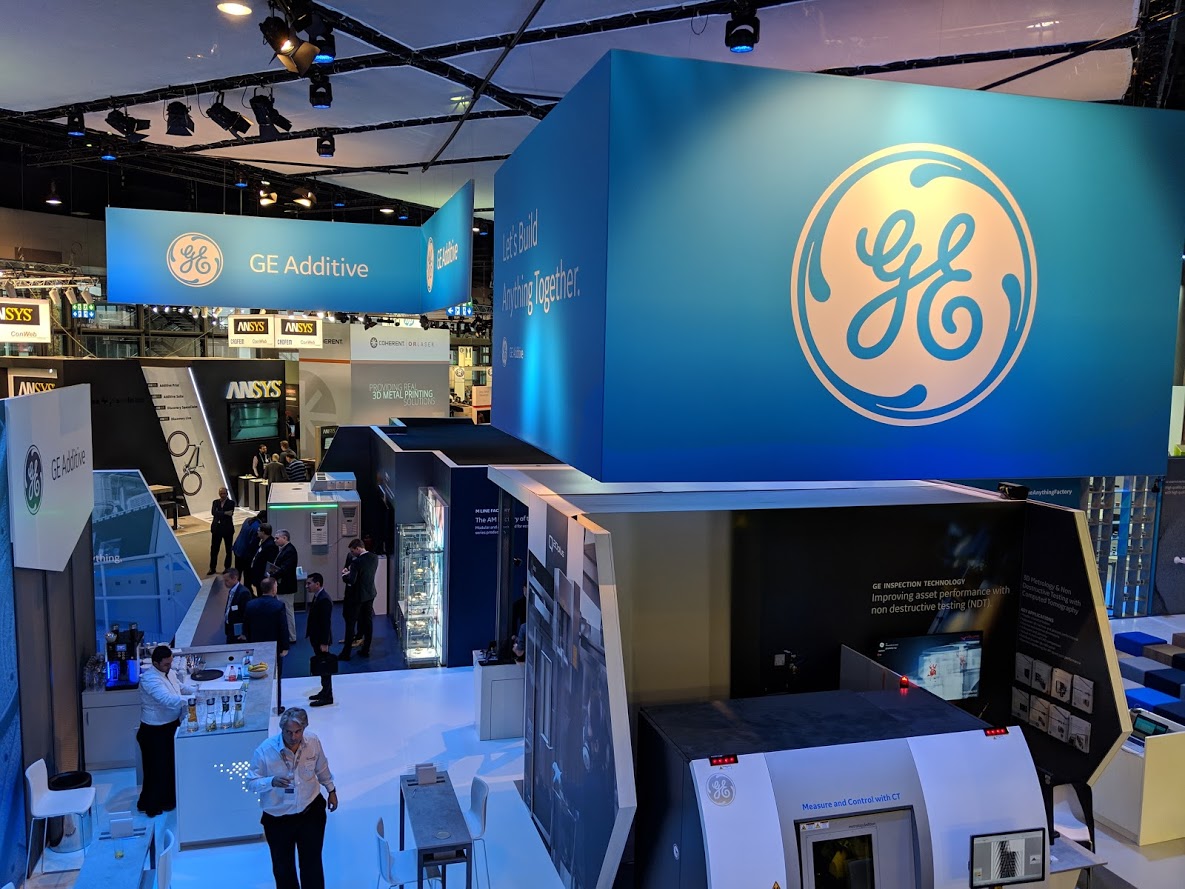
“We work with customers on pain points and address these. There is no one answer; it will be a tough road. It isn’t done in ten minutes,” Furstoss said of the work ahead.
Looking to her own background with GE, she pointed to the energy sector as an example of additive manufacturing adoption.
“In the energy sector, we really need to examine distributed manufacturing. Using additive for spare parts made closer for oil and gas, mining, and power plants can potentially save significant time and money for these 24/7 operations,” she said.
Beyond these examples, the question remains: What role can additive play?
“What sets my agenda is really understanding what industrialization means for each customer and for what they need. Integrating into that ecosystem means a customer needs to start with their business model and we need to ask: how can AM play a role?” she noted.
“We’re focusing on robustness and repeatability of machines; it’s not as much about how many lasers can we put in, but about how to make them configurable to meet customers’ needs.”
So with all that, what does industrialization mean for additive manufacturing?
Similarly to any area of industrializing focus, it can mean something different to every user; whether easing work flows, adding agility to logistics, creating a better geometry/material relationship, speeding response time for replacement parts, lightening weight, or consolidating part counts. For all, though, it means creating an integrated process with a fully functional ecosystem producing reliable, repeatable results. And this is where additive manufacturing is headed — in more than ten minutes, yes, but the journey is happening now.
Via GE Additive