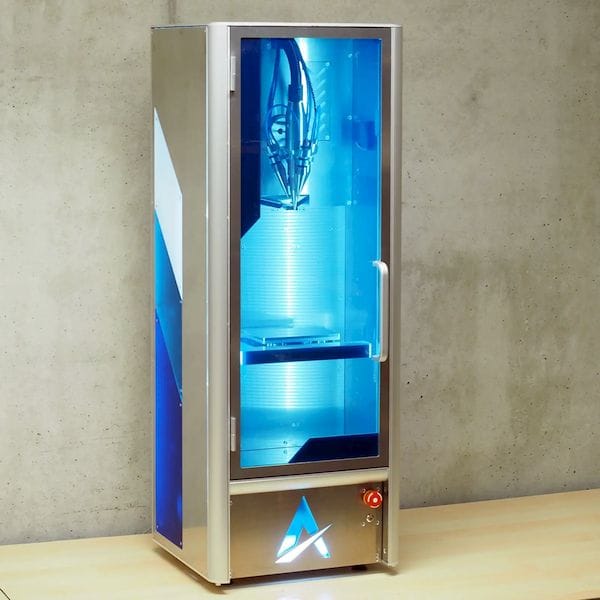
Some startups jump into public view with a big splash.
Others simply get in and start quietly swimming. This is the case for Las Vegas-based ADDiTEC, which introduced a comparatively low-cost desktop metal 3D printing system to no fanfare just six weeks ago.
Unlike other firms that have garnered significant media attention and investment, but have been slow to ship actual products, ADDiTEC is entirely self-funded and is already delivering its directed energy deposition (DED) 3D printer to customers. Moreover, the technology is capable of printing both metal wire and metal powder, separately or in a hybrid fashion, which is, as far as we are aware, previously unseen in the industry.
To learn more about ADDiTEC and its technology, we spoke to the companyās CEO and founder, Brian Matthews.
Desktop DED
Before we jump into the backstory of the company, you may want to know a bit more about the desktop DED technology that ADDiTEC is manufacturing. Dubbed the μPrinter (read aloud as āmicro printerā), the system is a $90,000 machine capable of 3D printing both metal wire and powder.
While the overall size is compact (390mm x390mm x 1100mm), its build envelope is actually pretty substantial at 160mm x 120mm x 450mm. It features three 200W diode lasers for a total of 600W of power (two more lasers are available as an upgrade for 1kW of power). Printing takes place within an argon chamber that only requires a small amount of gas, according to the company.
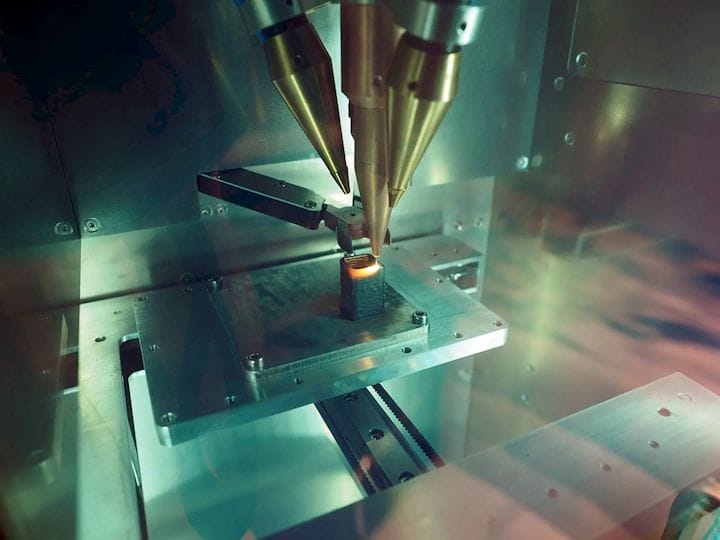
The system features āactive process control,ā which automatically sets the nozzle to part distance for each layer and also manages process parameters throughout the print based on sensor feedback.
A built-in wire cutter can be used during print failure, with the controller automatically returning to the point where the issue occurred, cutting the metal wire and continuing the print process.
Applications of Desktop DED
One of the potentially larger users of a desktop DED system, such as the μPrinter, is researchers in universities or labs. Matthews estimates that roughly two-thirds of inquiries for the system have come from universities from all over the world.
The μPrinter makes sense for experimental applications, both as an entry into larger DED systems and as a means of performing material development and hybrid metal 3D printing. Before embarking on a large-scale DED machine, the desktop printer can be used to determine if the technology is even right for a given application. The ability to combine materials, using wire feedstock for one metal and powder for another opens up a world of possibilities for material experimentation.
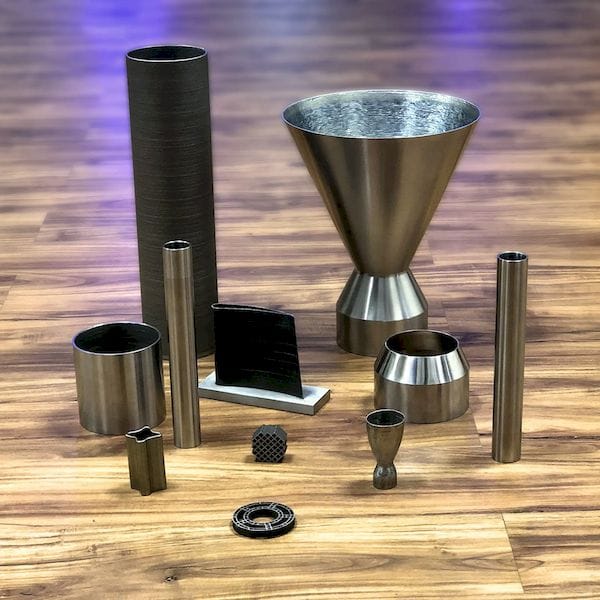
Matthews used the nuclear and aerospace industries as examples of where such hybrid parts might be of interest.
āThe nuclear industry has a really complex and expensive set of materials they use,ā Matthews said. āA lot of those materials in certain cases are borated: materials that contain neutron-absorbing material like boron carbide. Those materials are very expensive to work with. The benefit of our system is that you could print with one metal to create the structure and then you can apply the boron carbide to the structure youāre printing in an as-needed manner. The powder flow is turned on and off in the gCode.ā
As for the aerospace industry, metals with good structural properties could be coated with those with good thermal properties.
ā[Printing with wire and powder is] a no-cost option,ā Matthews said. āItās a standard feature of our system that you get powder and wire deposition capabilities.ā
Read more at ENGINEERING.com
FELIXprinters has released a new bioprinter, the FELIX BIOprinter, which is quite a change for the long-time 3D printer manufacturer.