![[Image: EOS]](https://fabbaloo.com/wp-content/uploads/2020/05/EOS_Material-Part-Content_img_5eb0977374724.jpg)
Industrial 3D printing continues to march toward serial production.
EOS is among the companies invested in leading that charge and is consistent in their messaging: additive manufacturing is ready for production. For EOS, developing the industry is a critical consideration as emerging technologies gain ground in scale manufacturing operations.
‘Developing the industry’ entails not only ensuring that the technologies and materials are able to deliver in the lab, but stepping up to the stringent requirements of full production environments. That is: standardization.
With its latest materials release, EOS is introducing four new metal materials for additive manufacturing — with full comprehensive data on each material’s properties.
The comprehensive data release fits in exactly where the 3D printing industry should be focusing, as traditional manufacturing begins to make room for the newer processes. We recently saw, for example, that the Aluminum Association has released its first new material registration in nearly two decades, for aluminum materials for additive manufacturing.
Metal powders for additive manufacturing are not drop-in equivalents from previously existing metal powders for other processes; metallurgists and material scientists have been very hard at work in developing 3D printable metal materials that can deliver the expected qualities of each metal. When we talk about limited availability of materials in 3D printing as compared to traditional manufacturing, it’s because of that lack of drop-in sameness. Each material has to be developed specifically for additive manufacturing, able to survive the process and meet quality needs.
And this week, EOS has introduced four such materials: one stainless steel, one aluminum, and two grades of titanium, all designed for use with DMLS 3D printing.
Each metal material comes with data that includes such detail as “the number of test specimens on which the mechanical properties are based on” and “detailed scanning electron microscope (SEM) images that provide an insight into the material quality.”
EOS explains of the materials:
EOS StainlessSteel CX is a new tooling grade steel developed for production with the EOS M 290 that combines excellent corrosion resistance with high strength and hardness. Components made from this material are easy to machine and enable an excellent polished finish.
EOS Aluminum AlF357 is the ideal material for applications that require a light metal with excellent mechanical/thermal strength. Components made from this material are characterized by their light weight, corrosion resistance and high dynamic loading. EOS Aluminum AlF357 has been specially developed for production with the EOS M 400, but it is planned to also make the material available for the EOS M 290 system in the near future.
EOS Titanium Ti64 Grade 5 has been specially developed for its high fatigue strength without hot isostatic pressing (HIP). Suitable for production with the EOS M 290, the material also offers excellent corrosion resistance, making it ideal for aerospace and automotive applications.
EOS Titanium Ti64 Grade 23 has also been specially developed for its high fatigue strength without hot isostatic pressing (HIP) and for production with the EOS M 290. Compared to Ti64, Ti64 Grade 23 offers improved elongation and fracture toughness with slightly lower strength. Thanks to these properties, it is particularly well suited to medical applications.
Below are SEM images of each of the new materials, top to bottom/left to right in the same order as above:
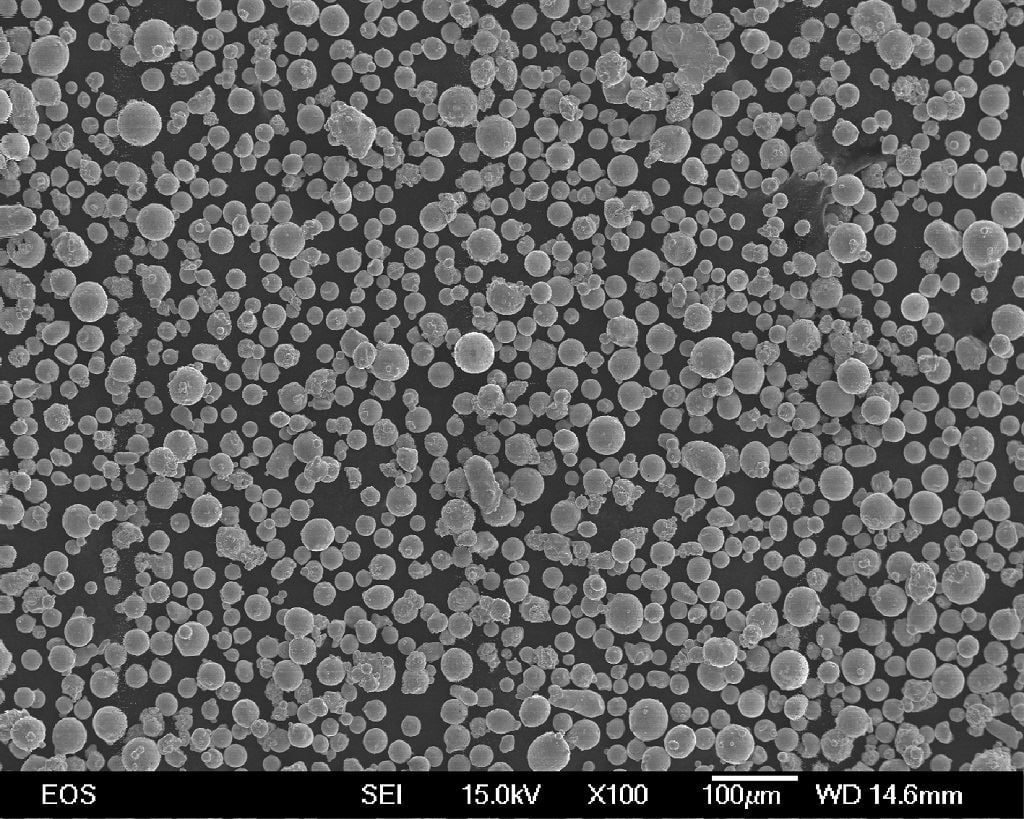
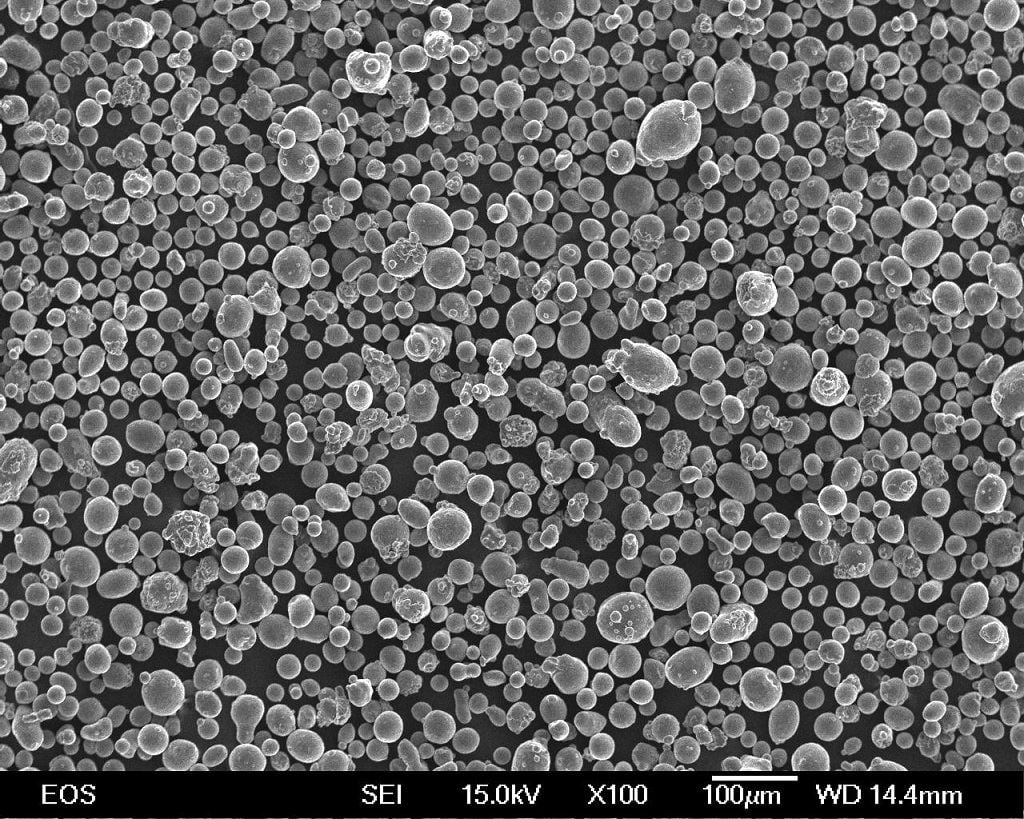
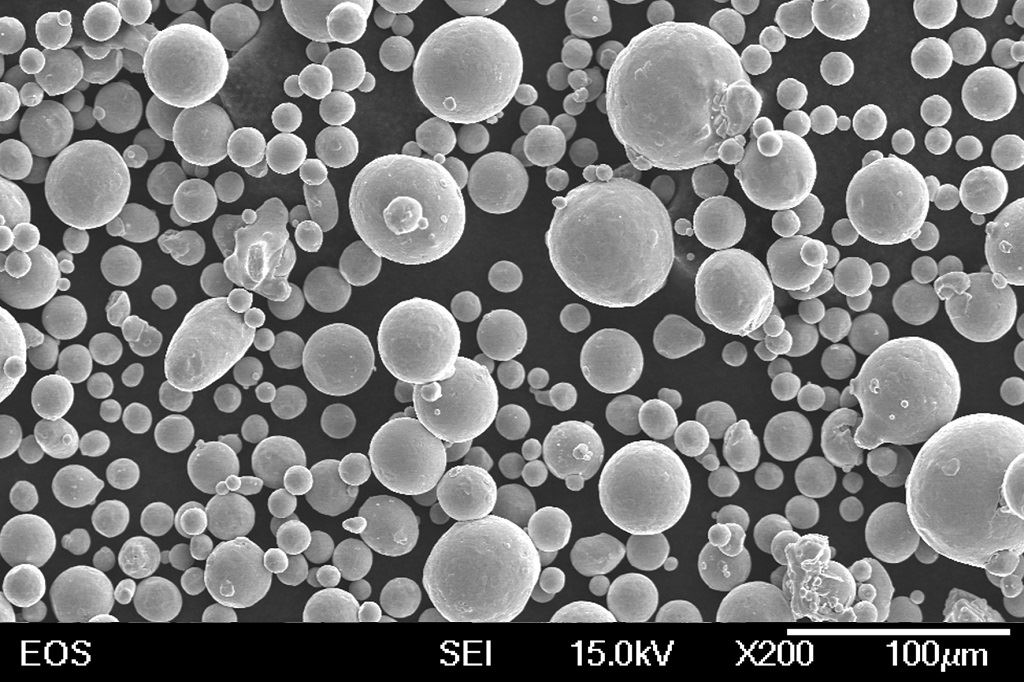
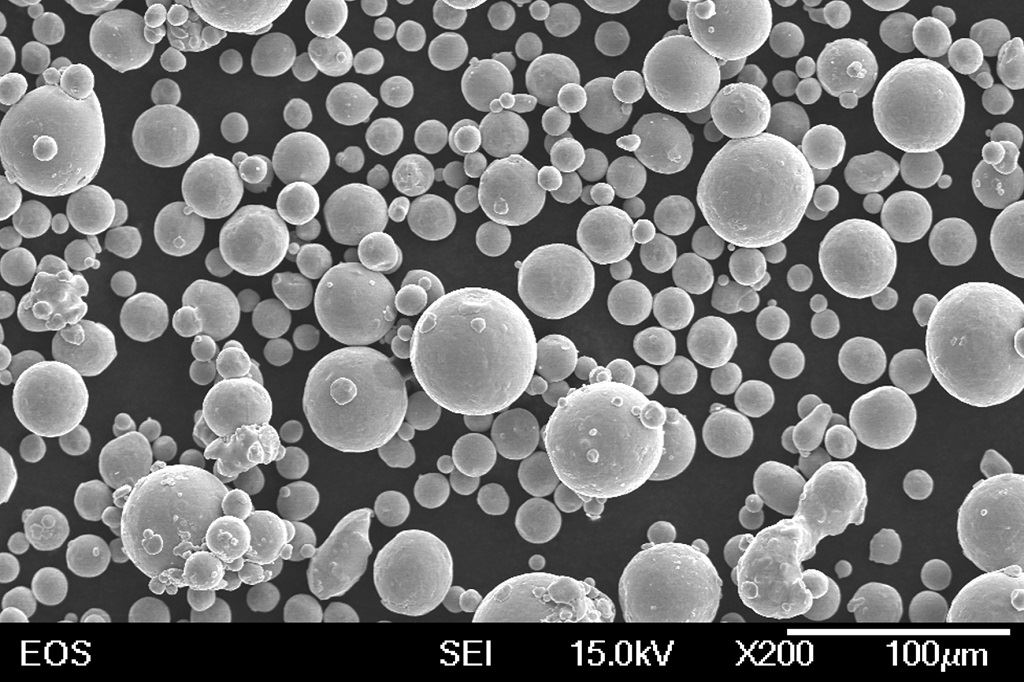
Going deeper into their materials focus, EOS further classifies its polymers, metals, and processes by Technology Readiness Levels (TRLs), a concept NASA developed that has extended to several industries. The levels go up to 9, which “refers to full production capability with extensive statistical data documentation”; level 5 is a verified technical solution.
These TRLs are then further broken down, with TRL 3-6 EOS’ “CORE” products and TRL 7-9 their “PREMIUM”. The new materials are all PREMIUM, with the two titanium grades and the aluminum a TRL 7, and the stainless steel at a TRL of 8.
Granted it’s by their own rankings, but it sounds like these new metals are ready for realizable market solutions.
EOS does maintain stringent material focus, including the operations of EOS Oy in Finland, where the company says it “has a complete location that concentrates solely on the development, qualification, and quality assurance of metal materials and processes.
With 30 years in additive manufacturing, EOS has well established itself as an industry leader, claiming more than 25 years of experience working with metals.
“At EOS, the development of systems, materials, process parameters, software, and services have always gone hand in hand. All of the elements are perfectly aligned to each other. The result is reproducible high-quality parts at a competitive cost per part. This combination is of crucial importance, particularly for series manufacturing,” said Hannes Gostner, Director Research and Development, EOS.
Via EOS