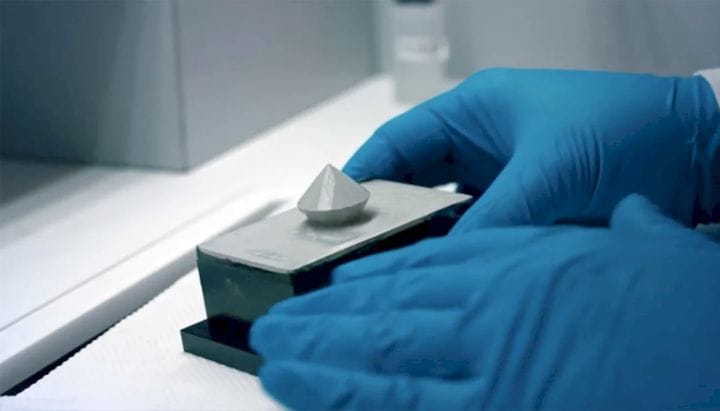
Without materials, no manufacturing process would be able to do… well, anything.
For the additive manufacturing (AM) industry, materials are one of the key ingredients to widespread industrial adoption. For this reason, numerous chemical companies, from BASF to DSM, have jumped into the game.
This couldn’t have been clearer at RAPID + TCT 2019, where a slew of partnerships and products were announced, indicating the continued industrialization of 3D printing. As a follow-up to our wrap-up on hardware and software, here are some of the most important materials stories from this year’s show.
BASF Supports New 3D Printing Technologies
BASF is now a mainstay of the 3D printing industry, not just manufacturing materials but also investing in companies like Materialise. It’s also begun partnering with companies to accelerate the development of materials for unique technologies. At RAPID, the chemical giant’s list of partnerships included Paxis LLC, which has developed what it calls Wave Applied Voxel (WAV) 3D printing.
BASF will provide its tough Ultracur3D ST 45 urethane resin to Paxis for its technology, a scalable photopolymer AM technology said to be capable of printing large-scale parts at four, eight or even 24 times the speeds of existing vat polymerization technologies.
BASF is also working with Impossible Objects to make its Ultrasint PA6 (polyamide 6) powder available for the startup’s CBAM technology, making it possible to 3D print carbon fiber-PA6 composite parts. The composite is meant to be stronger and have greater temperature performance than PA12, but at a lower cost. The carbon fiber-PA6 material is described as being four times stronger than fused deposition modeling parts and twice as strong as Multi Jet Fusion parts made with PA12.
DuPont’s New Plastics
You can’t discuss plastics without also mentioning DuPont, which has also firmly entrenched itself in the world of 3D printing. At RAPID + TCT, DuPont Transportation & Advanced Polymers introduced six new Zytel polyamide (PA) and Hytrel thermoplastic polyester elastomer (TPC-ET) pellets, as well as two new Hytrel filaments for 3D printing.
The new Zytel materials include glass fiber- and carbon fiber-reinforced, as well as unreinforced, PA. These represent additions to the company’s existing Zytel resins, which have been in existence for over 70 years. DuPont’s new PA pellets are meant to be strong, stiff and resistant to heat and chemicals, while displaying low shrinkage, warpage and moisture absorption when compared to PA6.
The Hytrel TPC-ET pellets and filaments are made from a flexible yet strong copolyester with high heat and chemical resistance. The new products vary in terms of hardness that can be matched up with injection molding shore grades.
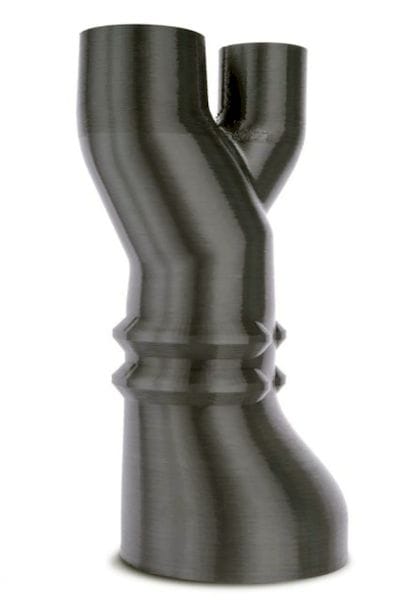
These releases are representative of an important shift taking place in the AM industry. Whereas, when the field was first emerging, systems manufacturers were also usually materials suppliers, with some exceptions in metal AM, since the 2012 desktop boom, the entire 3D printing field has opened up and grown, drawing in a greater number of giant chemical companies.
For 3D printing to enjoy widespread industrial adoption, traditional manufacturers want to be able to use materials and physical properties they’re familiar with in other processes, such as injection molding. The pelletized materials, typically found in injection molding, are less expensive and 3D printers that use them will make the process of transitioning from prototyping to production.
Solvay Teams with Stratasys
Belgium’s Solvay is yet another chemical company that is now a mainstay of 3D printing. This year, the firm announced a partnership with AM stalwart Stratasys to adapt its Radel polyphenylsulfone (PPSU) polymer into filament form for use with F900 3D printers. Radel PPSU meets Federal Aviation Regulations (FAR) 25.853 standards for use in aerospace, making it a complement to Stratasys’s existing ULTEM material. In particular, Radel PPSU have been used over the past 25 years to create parts for aircraft interiors, exhibiting chemical resistance and toughness, as well as all of the necessary properties necessary for aircraft usage.
Royal DSM Partners with Startup
Dutch chemical maker Royal DSM was among the first companies to begin manufacturing third-party resins for vat photopolymerization 3D printing. After investing in Texas-based startup Adaptive3D, Royal DSM will now manufacture, distribute and sell the firm’s Soft Tough Rubber photopolymer. The material is designed for applications such as medical models and consumer goods, with the properties of silicone.
Diamond Composites from Sandvik
In addition to their beauty, diamonds are known for their immense strength (58 times stronger than anything else in nature). Sandvik Additive Manufacturing, the AM-focused division of the larger Swedish engineering and tool maker company Sandvik, has developed a diamond-based polymer composite.
The material is made up of a diamond powder suspended in a photopolymer resin. A specialty post-processing step is then employed to produce what the company claims are the properties of diamond composites.
Read more at ENGINEERING.com
An inventive designer has developed a method for producing 3D paper objects using recycled paper and 3D printed molds.