![Hanan holds XJet material in front of the Carmel 1400 system [Image: Fabbaloo]](https://fabbaloo.com/wp-content/uploads/2020/05/XJetHanan_img_5eb09633f0595.jpg)
XJet’s CEO shares a look into operations and applications in metal and ceramic 3D printing.
I appreciated the chance recently to catch up again with the XJet team. The Israeli company is certainly very busy, and as Founder and CEO Hanan Gothait and I sat down to chat, the team had recently unveiled some impressive new customer applications — and some developments of their own.
Business operations are “in good shape” just now, Gothait said as we began our chat. The company remains supported by shareholders, and is always keeping an eye out for opportunity.
When it comes to customers, XJet is “developing quite a list, which is nice,” Gothait said with a smile. More than a dozen of their unique Carmel systems have been installed, and “more are coming.” These are now in use in Europe, the US, and of course in Israel, where the company is based. “Maybe next year we will start in China,” Gothait said of future plans; all capacity at present, though, is dedicated to Europe and the US.
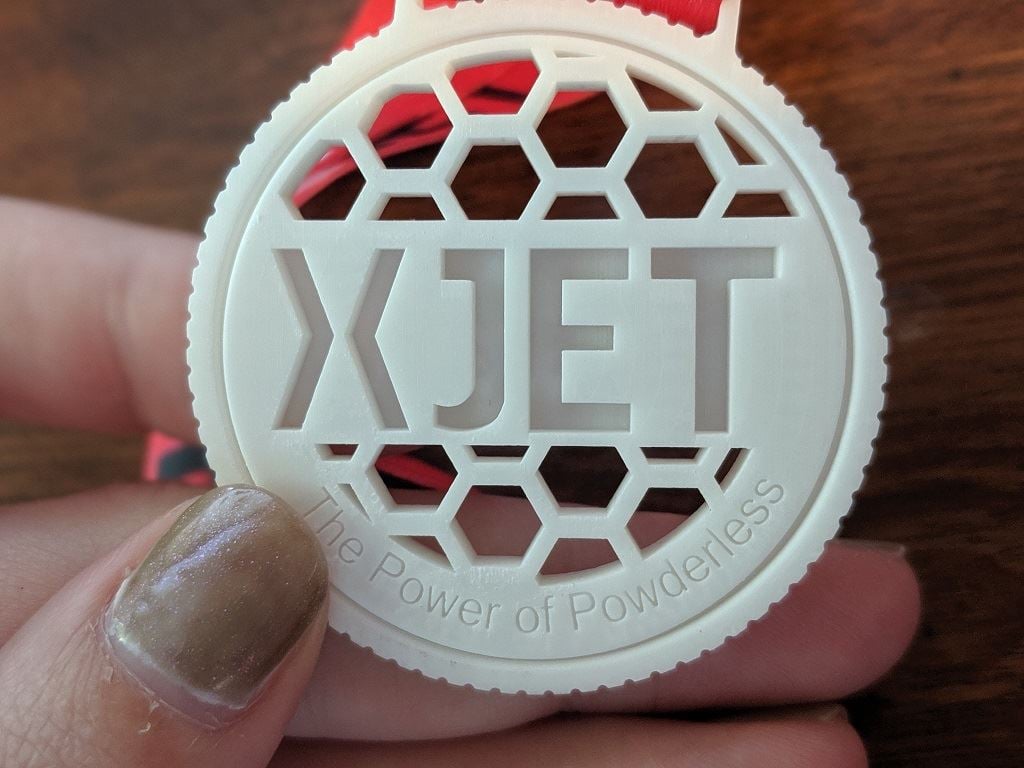
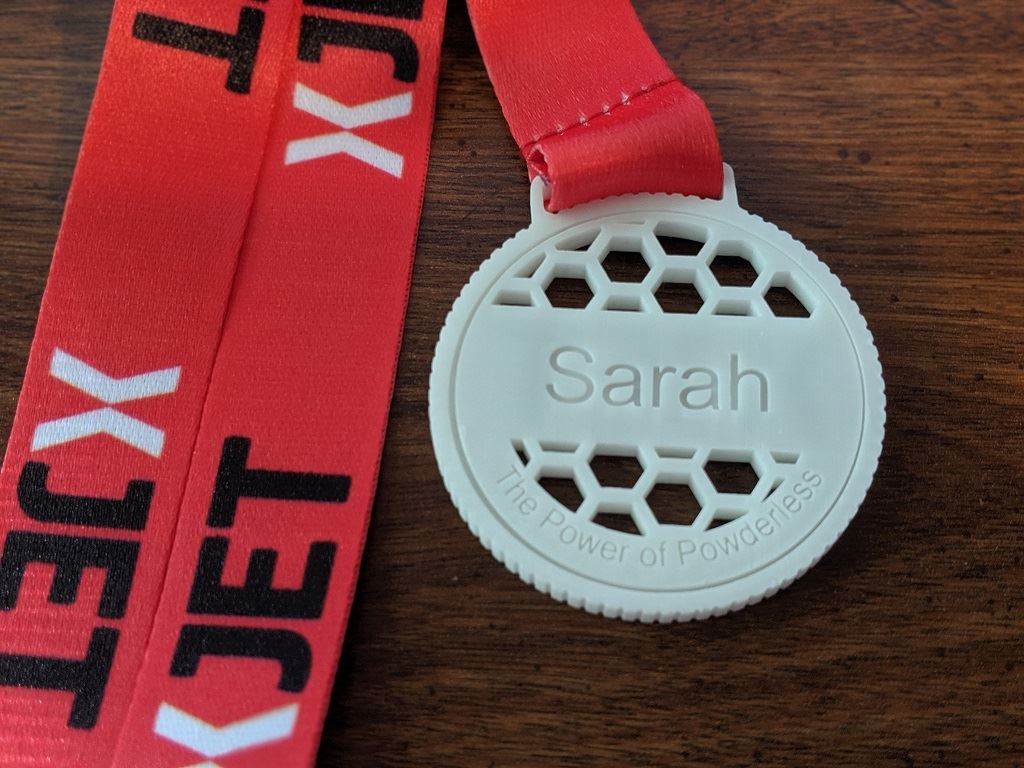
At RAPID + TCT, the XJet team wore 3D printed ceramic medallions with their names on them; they thoughtfully made me one of my own. The center spins. [Images: Fabbaloo]
Naturally, many of XJet’s customers wish to remain confidential — but some are willing to share their use of the Carmel. The company’s customers include medical device companies, automotive suppliers, and research institutions. Among those able to be named now are Oerlikon, the Youngstown Business Incubator (YBI), and the University of Delaware; “we hope to release more customer information at formnext,” Gothait added.
And what are they using NanoParticle Jetting (NPJ) technology to do? That usage, Gothait said, “is all coming from our customers.”
“The printers give capabilities to do very smooth surfaces, very accurately, in any geometry, and with high density,” he said.
So accurately, indeed, that support structures will dissolve even in internal structures, allowing for more complex geometries. They have reached “99-point-something percent density in both ceramics and metals, which gives more abilities to customers.”
XJet recently released news of intriguing applications that they were able to highlight during RAPID + TCT.
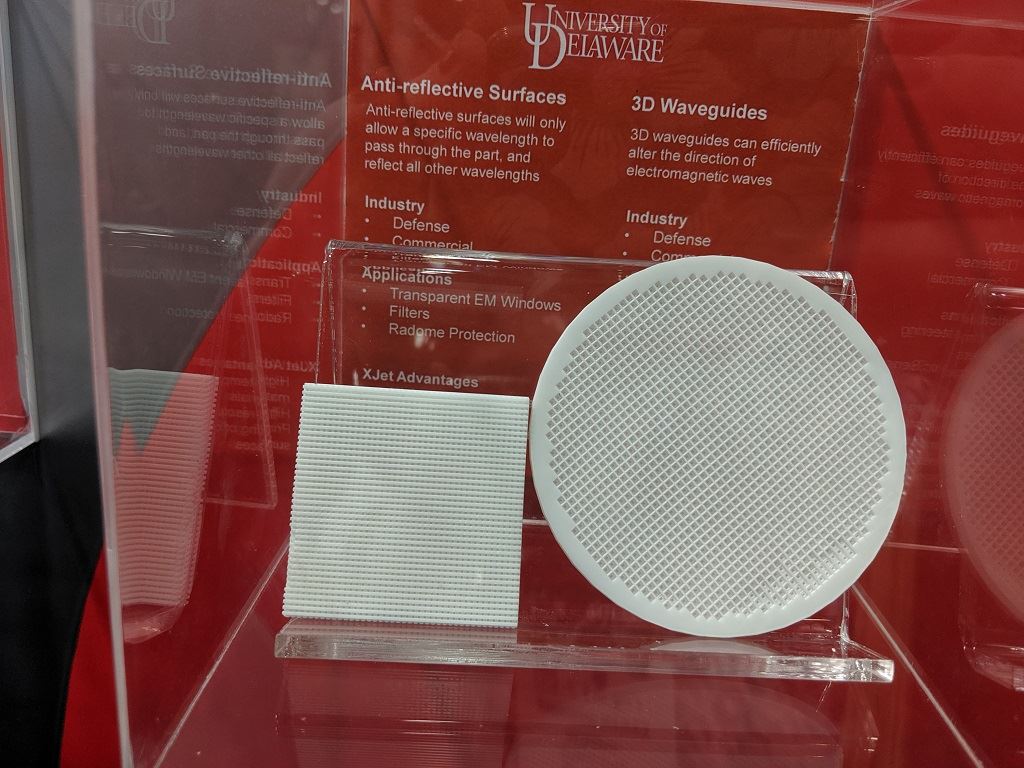
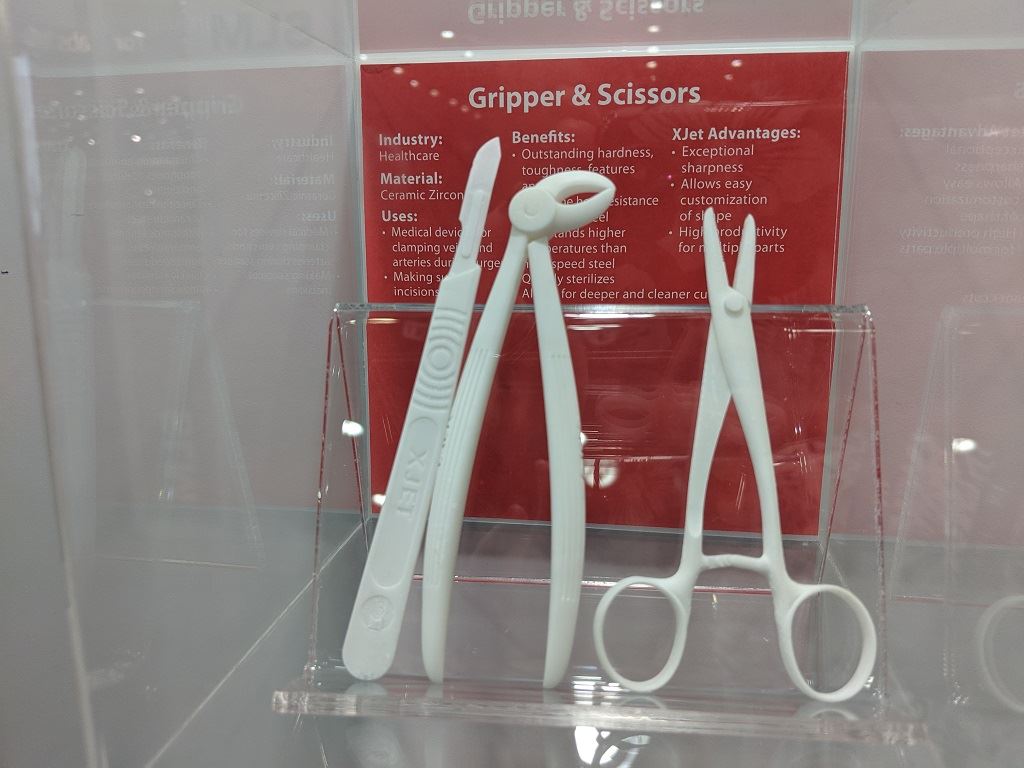
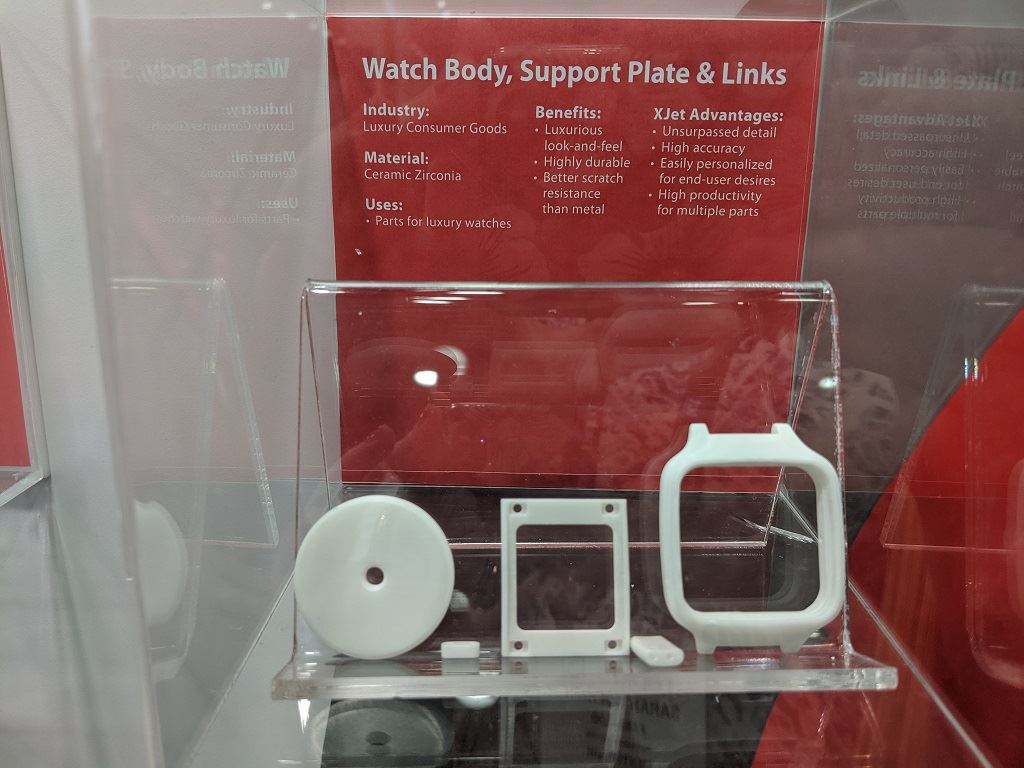
L-R: University of Delaware, Marvel Medtech, and watch parts [Images: Fabbaloo]
In one, through an installation at Marvel Medtech, a 3D printed ceramic cryotherapy probe — which Gothait describes as looking “like a ceramic pen” — is used in a new approach to breast cancer prevention. The team will have a full case study detailing the usage soon for more details. Gothait noted that the device “has to be made of ceramics,” as it must be used within an MRI machine. Surgical tools made of sterilizable materials like ceramic open up more opportunity for medical providers to ensure they have exactly what they need.
“This opens up a whole world of new tools, small-series specialized tools. These are not made in the millions,” Gothait added.
For the University of Delaware, the Carmel 1400 has come into play to create a 5G antenna. The university is doing significant research in communications, Gothait explained, including in 5G communications that typically require “very expensive antennas.” The faster signals of a 5G network generally require sensitive antennas — and a lot of them. But a precise, isotropic, 100% dense ceramic antenna made to exacting specifications can “produce the lens with the complex structure, small channels and material properties required,” as the release details.
“They printed, instead of a $15-20,000 antenna, a $1,000 antenna. Instead of needing $300 million to cover Manhattan, it would be $1 million. This is a big revelation for 5G,” said Gothait.
We also looked at precise watch parts “for a very big company” made for luxury watches that we should “think of as small computers.” Because the high-end watches “are not made in high quantities, molding doesn’t make sense.” 3D printing often comes into play for such uses, Gothait noted, as “customization enables things they couldn’t dream before, perfect for high-margin, low-quantity products.”
“It’s amazing to me that our customers are always developing, always coming up with all these ideas,” Gothait said.
Indeed, those are very disparate uses for the same piece of machinery.
Along with its applications and customer bases, XJet itself is growing. The team is now 130 members strong, and “growing fast.” The new Additive Manufacturing Center in Israel now houses the whole team, and there is a “good vibe, good energy” there as they continue to grow.
XJet CBO Dror Danai also dropped in on our chat to catch up. He showed me the first successful multi-material ceramic-and-metal prints, which Kerry and Marney also had the opportunity to examine.
![Dror holds a proof-of-concept square made for the University of Delaware to ensure density [Image: Fabbaloo]](https://fabbaloo.com/wp-content/uploads/2020/05/XJetDror_img_5eb096368080a.jpg)
3D printing metal and ceramic on the same machine was attention-grabbing; doing so in the same actual build is, well, huge.
“A big automotive company had been gluing together metal and ceramics, and the glue failed,” Gothait said. “They needed one piece for high temperatures.”
![The first successful metal-and-ceramic prints [Image: Fabbaloo]](https://fabbaloo.com/wp-content/uploads/2020/05/XJet4a_img_5eb09636e174e.jpg)
So XJet made it possible. It’s still very early days for this type of multi-material 3D printing, but Danai noted that the prints he showed me were from six weeks before, and progress has continued with results that are “much better now.”
Via XJet
Coronavirus is on the rise, and so are efforts to deploy 3D printing to combat infection.