A row of Fortus 900mc 3D printers at work at Stratasys Direct Manufacturing in Belton, TX [Image: Fabbaloo]
This week I ventured to Texas to visit two Stratasys Direct Manufacturing facilities.
The contract manufacturer is an arm of Stratasys, so unsurprisingly 3D printing — and not only Stratasys technologies — plays significantly into their offerings.
Stratasys Direct on the whole is a large operation, comprising six manufacturing sites and one office: I went into two Texan production facilities, in Belton and Austin, to get a good look inside.
Stratasys Direct Manufacturing
[Image: Fabbaloo]
In 2014, Stratasys acquired and merged operations of several busy service providers, forming Stratasys Direct Manufacturing from previously separate entities Solid Concepts, RedEye, and Harvest Technologies.
Today, operations comprise around 550 employees total across the six manufacturing sites. Valencia, California houses the largest manufacturing facility, clocking in around 100,000 square feet of production space. Other sites are located in Tucson and Phoenix, Arizona; Poway (near San Diego), California; Eden Prairie (near Minneapolis), Minnesota; and an office in Detroit, Michigan.
The 40,000-square-foot Belton site employs around 100, including interns, and had originally been part of Harvest Technologies, and is a dedicated additive manufacturing facility primarily focused on production (with about a 70/30 to 60/40 split in production/prototyping), especially in thermoplastics. Metal prototyping operations are also performed on-site, including materials development efforts. The 30,000-square-foot Austin site is essentially the reverse, with focus in metal production.
High-Flying Applications
SLS 3D printers at work at Stratasys Direct Manufacturing in Belton, TX [Image: Fabbaloo]
The teams at both Belton and Austin were keen to highlight the lengths they go to for every order. We’ll focus first in this piece on the Belton team.
Those orders are substantial; in aerospace alone — a huge market not only for additive manufacturing in general but for Stratasys Direct in particular — Belton ships around 30-35,000 parts each year.
Greg Reynolds, Vice President of Additive Manufacturing, Stratasys Direct, walked me through some of the history the company has in aerospace. As we watched an EOS system 3D printing in FAA-certified FR-106 material, he noted that many of the laser sintered parts they make use this material.
“We’ve been running this material since 2007, the year of our AS9100 certification. We think we were the first with this certification in 3D printing,” Reynolds said. “2007 was a baptism by fire in aerospace for us. We had to learn to run a new material quickly and deploy it. Ever since then, we’ve been immersed in the aerospace flight part world.”
This has only been ramping up over the last decade-plus. In 2017, Stratasys introduced its Fortus 900mc Aircraft Interiors Certification Solution, for example.
Most aerospace customers still won’t publicly share details of their use of additive manufacturing. The Belton facility serves more than 80 customers in this space, but the company can name only a handful including:
-
Airbus
-
Lockheed Martin
-
GKN Aerospace
-
Penske
-
Aurora Flight Sciences
-
Bell (formerly Bell Helicopter)
The first of these, Airbus, has been especially vocal about its use of 3D printing in operations. While of course there are many application details that can’t be shared, that company has been willing to speak to some extent about their use of Stratasys’ technologies and services over the last few years.
Recent conversations with Stratasys execs have revealed more of the depth of their participation in the aerospace sector — but it was something else entirely to set foot on the ground where that participation happens.
In a lineup of Fortus 900mc 3D printers, all certified for use in aerospace applications, we watched several parts printing in ULTEM for Airbus. Along with these flight parts, as on every print-in-progress I saw during the day, were tensile bars.
Traceability
HP Jet Fusion 3D printers at work at Stratasys Direct Manufacturing in Belton, TX [Image: Fabbaloo]
When it comes to uses in demanding applications like aerospace, certifications and verifications are critical.
The tensile bars in each print are made using the same process, parameters, and materials as customer parts, allowing for batch-specific test parts. Accountability is crucial, and these physical parts are only a very, very small part of what Stratasys Direct does to prove out their process.
Each build is individually and uniquely tagged: a barcode sticker contains detailed information about employees handling the process, the machine used, the specific batch of material used, and all dates involved. These are all digitally logged in an extensive system that developed from need.
During the 2007-2008 ‘baptism by fire’ period in which Stratasys Direct was amping up its participation in aerospace, the team noticed “paper everywhere,” as Reynolds noted. So Director of Software Development Jason Morgan developed a digital system to track all information to provide the customer with “full information, even years later.”
Morgan ran me through an example with a customer part to detail the process of tracking metrics on a Certificate of Conformance. Customer and part history, including build scrap rates, full materials traceability, and much more information is detailed and neatly catalogued for quick access.
“You’ve got to plan the work, then work the plan,” Reynolds said. “It’s all planned before hitting go on the build.”
At the heart of building up the traceability system, Morgan continued, was the intent to “build quality into the system.” This includes personnel quality — training is, in a word, thorough at Stratasys Direct. Once any training is out of date, an employee will be locked out of systems until it has been renewed. Only those fully up to date on all of the latest processes have access at any point to customer build information.
More To See
Aerospace applications and attention to detail took a good deal of our time at Belton — but there was still much more to see and to talk about there.
From development to scaling to process agnosticism to facility solutions for chillers and an uninterrupted power supply, it’s a busy business indeed. Stay tuned for more looks from inside Stratasys Direct in Texas.
Via Stratasys Direct Manufacturing
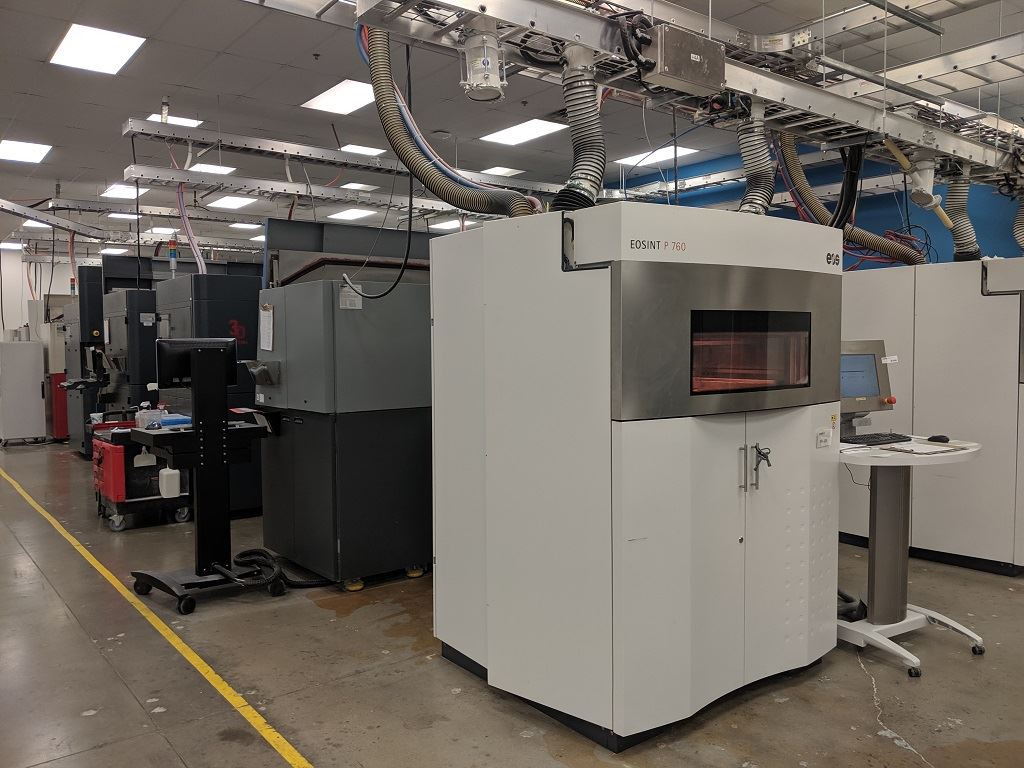
A lot goes into the business of contract manufacturing, and a recent visit to Stratasys Direct Manufacturing highlighted some major considerations.
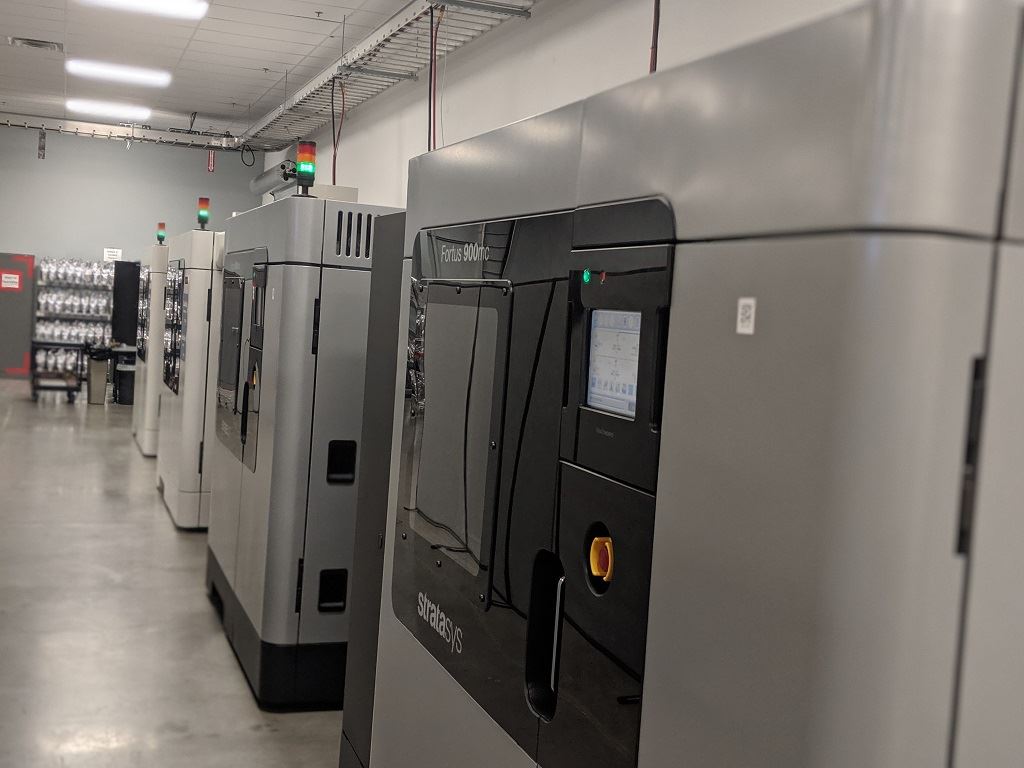
We visited Stratasys Direct Manufacturing in Texas for an inside look into operations including aerospace-qualiifed 3D printing.
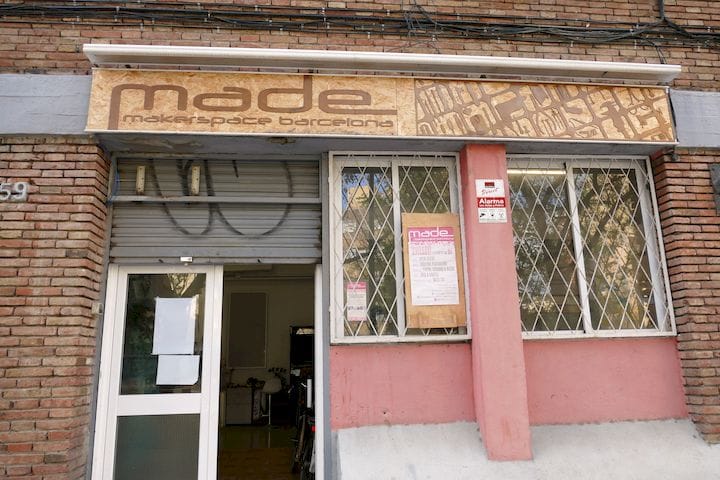
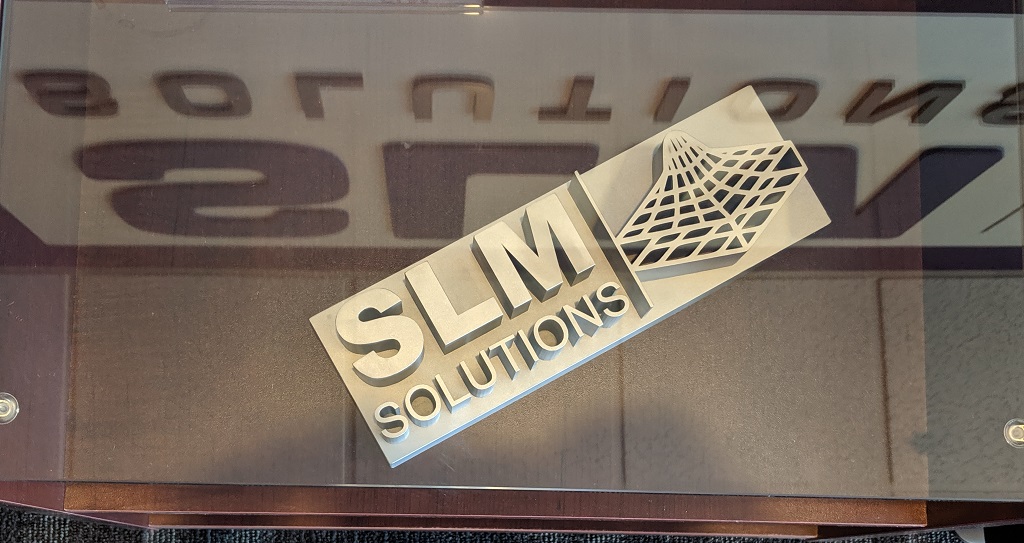
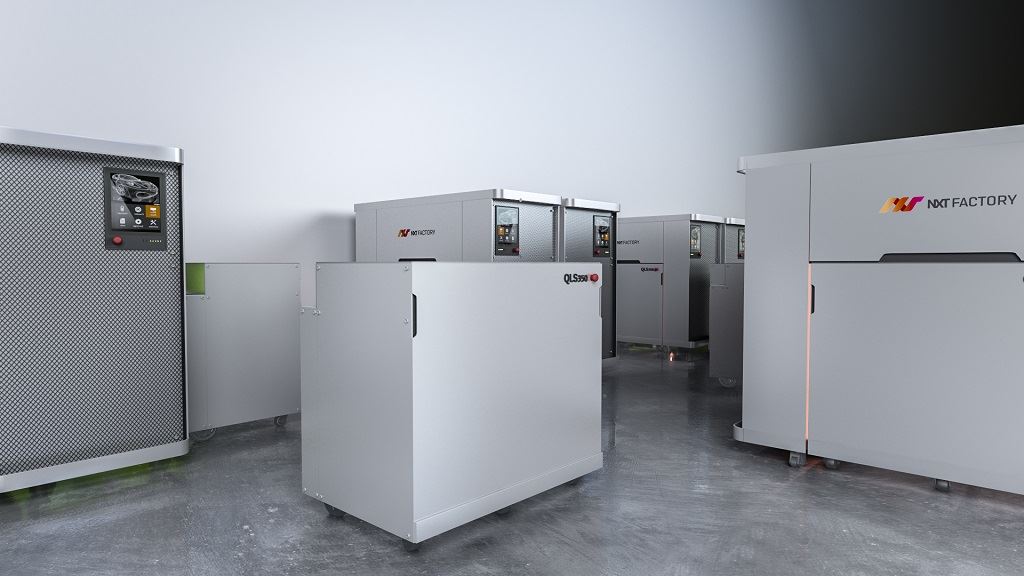
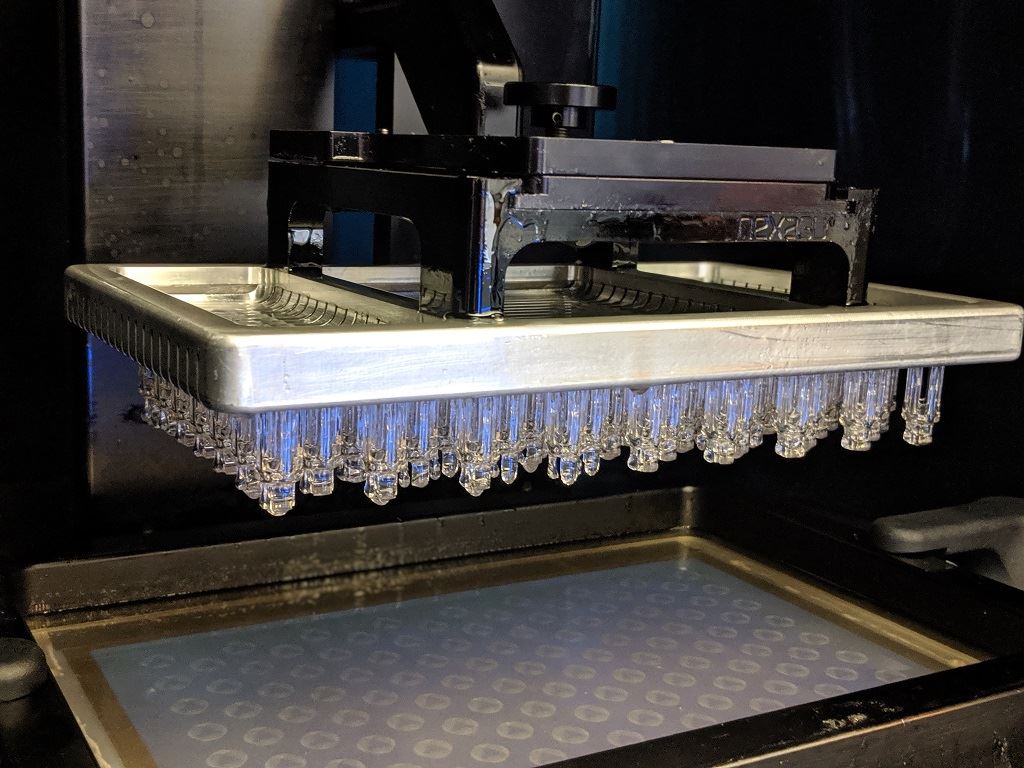
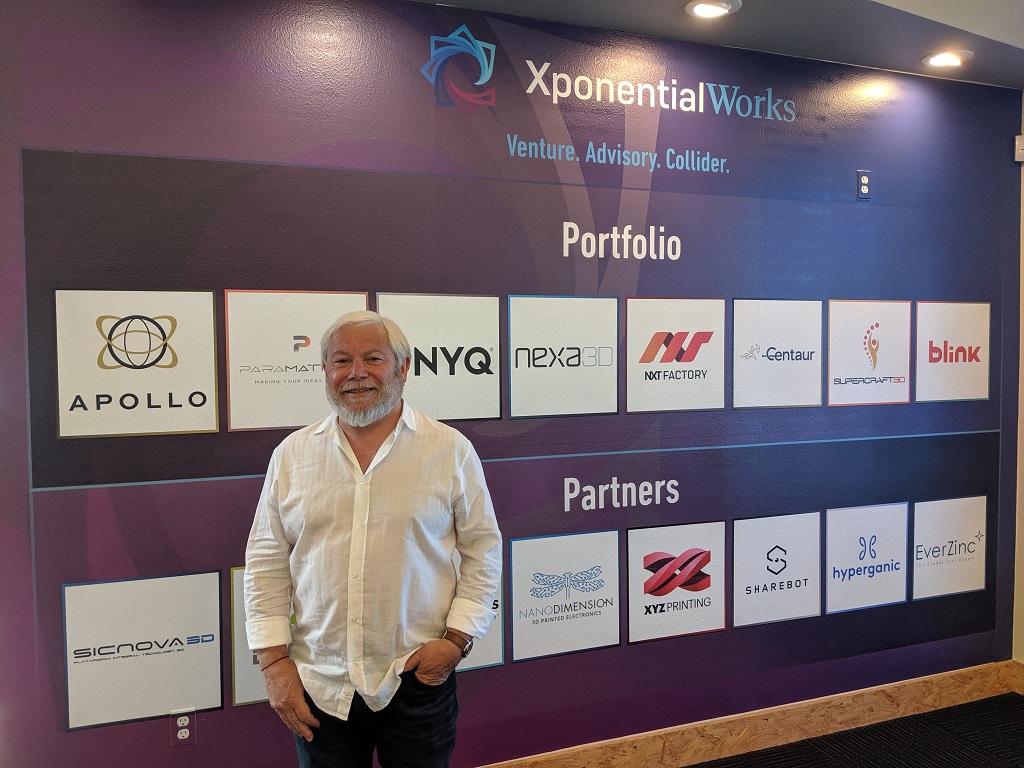

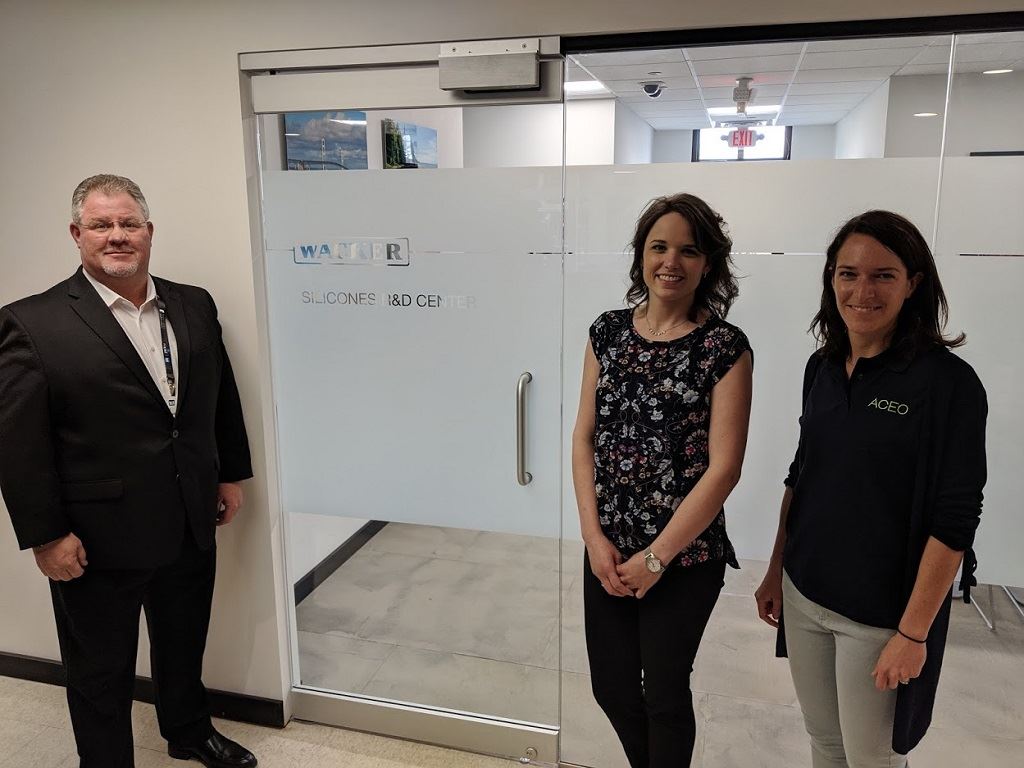
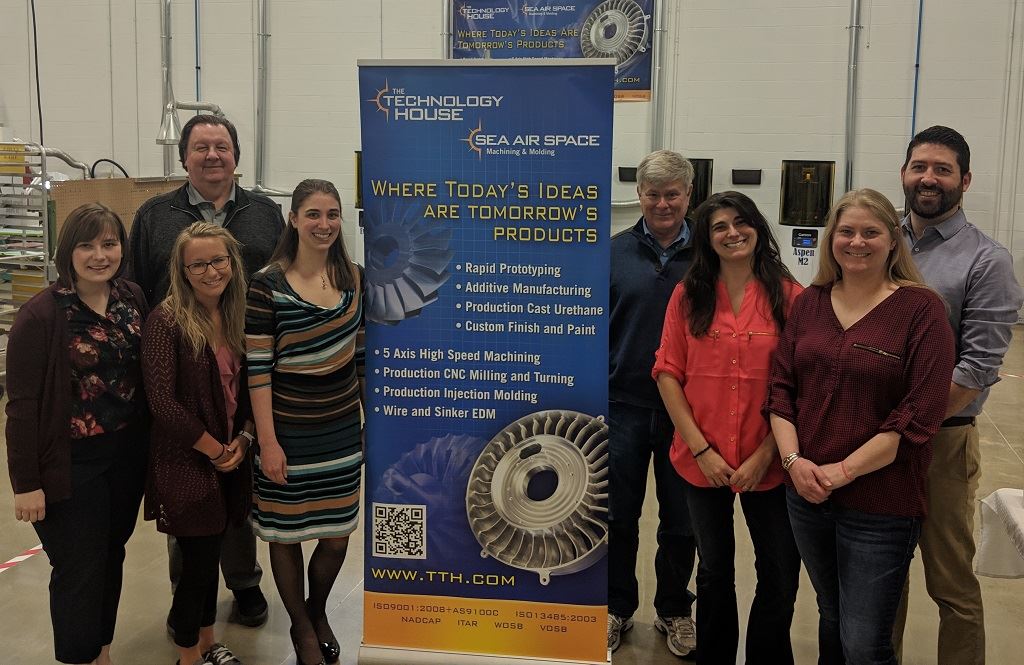