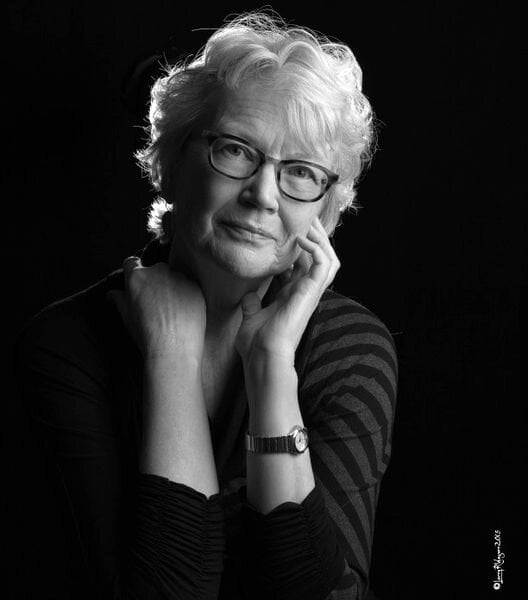
This weekās question is from an artist requiring metal 3D prints.
Kim Thoman is a California Bay Area artist and art professor who has been working for over 30 years. She has been 3D printing some sculptures for a few years, but now wishes to 3D print in metal. She asks:
āIād like to 3D print tree branches in metal. I work with a technician to create the files for 3D printing. These tree branches only need to be about 30 inches in length and about 3-4 inches thick.
I read about the new A1 company and type of printer and find that extremely exciting but I understand they are brand new. Yet, sometimes small new companies are interested in working with an artist to print something of interest.
Any other suggestions that you might have would be very helpful.ā
[Note: Thoman is referring to a recent story in Fabbaloo where we looked at a new Russian startup company, A1 (or is it āAIā?) producing a highly unusual metal 3D printer they call Roll Powder Sintering. While promising, they are nowhere near making a commercial product yet, as far as I understand the state of affairs at AI.]
Here is a look at the work that Thoman wishes to 3D print, or at least the branchy-portions of the sculpture:
![This artistic work needs to 3D print the branches in metal material [Source: Kim Thoman]](https://fabbaloo.com/wp-content/uploads/2020/05/image-asset_img_5eb08b9a39476.jpg)
This is quite an interesting design. From the looks of the scene, it appears that each branch could be individually 3D printed, and then attached to the central frame to create the illusion of an entire tree. Itās quite an amazing!
I can certainly understand why youād want these in metal, as they are quite lengthy and might snap if made from typical thermoplastics when moved or abusively touched by careless gallery visitors.
Powder Bed Fusion Metal 3D Printing
It seems the 3D print job to be done here involves producing around 15 metal parts. Iām guessing based on the scale provided by the chair in the image that some of the parts could be as long as one meter, and thatās pretty big as far as metal parts go. In fact, most metal 3D printers would not have a build size that large.
It perhaps doesnāt need to be said, but 3D printing metal on an occasional basis does not justify the acquisition of metal 3D printing equipment. Operating a metal 3D print facility is an incredibly expensive venture and can only be attempted if convinced you are able to feed customer print jobs for the many years it will take to pay off the equipment and other setup costs.
By the way, the cost of a proper metal 3D printing setup would include not only the 3D printer, but the materials, powder handling equipment, finishing equipment (Wire EDM, 5-Axis CNC, etc) and an air-controlled building to put it all in. Oh, and a squad of engineers to figure out how best to configure the jobs. Thatās not an option for almost anyone, and thus this work should be left to metal 3D print services who have the equipment and know what to do.
The problem, however, is likely to be cost. The cost of fine metal powder in these machines is terribly expensive and can be as high as US$500 per kg for titanium. While you could probably get away with a less expensive material, itās still going to be US$100 per kg or more. And thatās just the material cost; a 3D print service will also include the cost of equipment, staff, etc, as above.
I am thinking that if you were to contact a metal 3D print service with the request there would be issues. One would be the size of the parts, as they wouldnāt necessarily fit into the build volume on the typical equipment. Thus the 3D models would have to be chopped up into smaller parts and then assembled (welded?) together afterwards, at additional cost.
And then there would be the cost. I canāt say precisely what the cost would be, as youād have to work with a provider for a proper quote. However, I can say that the cost to produce these at a typical metal 3D printing facility would be many thousands of dollars. Itās probably too expensive to consider.
I should have mentioned that these parts should definitely be hollowed out to reduce the cost of metal used in the prints. If you have prepared āsolidā 3D models, then there are ways to extract the inside of them using CAD software.
There are other options.
Inexpensive Metal Prints
An option might be to use one of the lower-cost metal 3D printing processes, such as those from Desktop Metal or Markforged. Whereas the traditional equipment can cost millions to set up and operate, this type of equipment is only a tenth of that to set up and operate, and thus part costs would be correspondingly lower, too. However, the results are not necessarily of the same aircraft-ready quality of the more expensive options.
The problem is I am not aware of any 3D print service that operates Desktop Metal or Markforged equipment for hire. These companies may know of one, but I do not. If a metal 3D print service could be located that uses more inexpensive equipment, then the cost might be more in line with your objectives.
Thereās one more option that might be the best way forward.
Electroplating 3D Prints
![An electroplated 3D printed part [Source: Fabbaloo]](https://fabbaloo.com/wp-content/uploads/2020/05/image-asset_img_5eb08b9a7f4a7.jpg)
It is possible to 3D print these parts using standard thermoplastics. It could even be done using inexpensive desktop equipment, if you were to segment the 3D models to fit into the machineās build volume, and assemble them later.
The problem is that the thermoplastic prints might be too fragile, as discussed above. But there is a way to fix that: electroplating!
It is entirely possible to electroplate thermoplastic 3D prints to give them a āskinā of metal. This would not be as strong as a fully metal object, but far stronger than mere plastic. Thereās one catch with this approach, however: if the prints are heated they will droop just if they are plastic ā because they are still plastic underneath the skin.
An electroplating approach would be far less expensive than any other method and might result in parts that are sufficiently strong for this artistic purpose.
Where do you find electroplating services? In most cities there are already electroplating services for industry, and you would merely have to find one. I am aware of one service being developed specifically for 3D prints, Metallizr, but it is not quite launched yet. Some of the multi-process manufacturing services may offer electroplating, and I believe RePliForm used to do so.
If I were doing this, I would look for a large-format plastic 3D print service and an electroplating service, possibly at a contract manufacturing service. But Iād first do one single part through the two services to see if it meets all requirements before ordering all of them.
I hope that helps you understand your options!
[UPDATE] We were contacted by RenƩ Backx of Amsterdam-based MX3D, who provide a metal deposition solution for 3D printing that might be applicable in this case. He says:
āDefinitely an interesting design of the week on the 3D printed metal tree branches by Kim Thoman. We would suggest to also include WAAM (wire arc additive manufacturing, DED) in the article as a feasible technology for printing this design in metal. WAAM is able to print this large scale design more flexible, faster and for sure cheaper than the other technologies mentioned in the article. Considering the design of the organic tree, the more “rougher” surface of WAAM compared to SLM could actually fit the design better. It would be great if you could include this in the article as a technology to consider for this design.ā