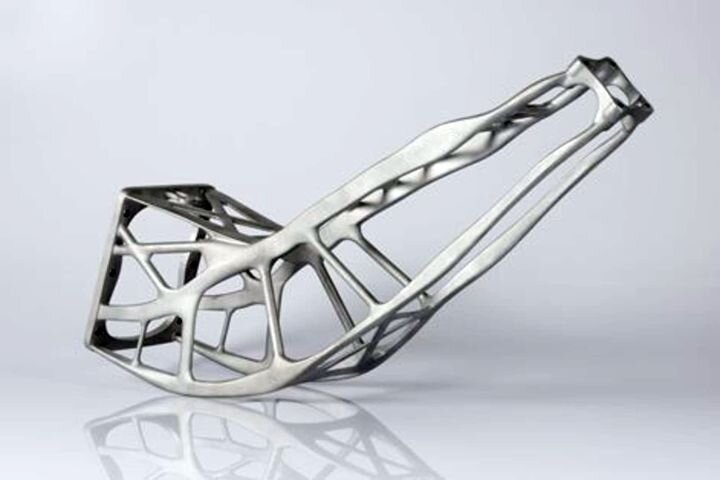
Additive manufacturing (AM) is gaining ground rapidly and is now being used to produce many certified aerospace components.
Initial concerns with density, porosity and grain structure have now been largely overcome. AM components now have microstructures equivalent to forged components, suitable for the most demanding structural applications subjected to high cyclic loadings.
A major driver for aerospace components is weight reduction, with operators willing to pay a premium for the reduced operating costs that come from greater fuel economy. AM components have more refined grain structures than cast components, comparable with wrought components. Another significant performance benefit of AM components is the ability to precisely control internal geometry to create cooling channels and heat exchangers with features such as turbulators which increase heat transfer.
An unresolved challenge for AM is surface finish. Components subject to fatigue must be fully machined or undergo some other surface modification, such as shot peening, to enable inspection. The additional processes add cost but more significantly this prevents the full benefits of AM from being realized. In theory, AM gives complete freedom to create complex shapes, such as those generated by topology optimization.
In practice, surface finish requirements often prevent this. If surface machining is required then the same limitations on form apply as for any other machined component. If shot peening is used then limitations are placed on thin and slender structures which may be vulnerable to this process.
Two AM processes are well established: Powder bed fusion (PBF) in which a laser or electron beam is focused to melt and fuse regions of powdered material contained in a powder bed; and wire fed directed energy deposition (DED) in which a plasma arc melts a wire feedstock as it is fed into the melt pool using technology closely related to welding. Both processes produce fully dense parts with high quality microstructures similar to forged components.
PBF is able to produce fine features with relatively well controlled surfaces for smaller parts. It achieves the best surface quality of any AM metal system, with the surface finish depending on powder particle size, typically ranging from 5 to 60 µm. A range of metal alloys suitable for aerospace components are available as well as high quality polymers.
Build volume is currently limited to 400 mm Ć 400 mm Ć 800 mm by the need to maintain a consistent gas flow over the build area to ensure sufficient quality as well as the requirement for the bed to be completely filled with heavy and expensive metal powder. Deposition rates are approximately 5ā20 cm3/h for a single laser.
Multi laser systems are currently able to achieve approximately 150cm3 in the fastest materials such as aluminum and around 30cm3 to 50cm3 in Nickel alloys Lasers are mechanically steered using mirrors meaning that multiple lasers are required to maintain multiple melt pools. Final surface finish is normally obtained by shot peening with machining only required for critical interfaces. The main disadvantages of PBF are the slow deposition rate and limited size.
Wire fed DED enables far higher deposition rates and virtually unlimited component size, but minimum feature size is several mm and the as-deposited surface finish is very rough. The large melt pool results in weld-bead shaped deposits which are normally machined to achieve the required dimensional accuracy and surface finish. Machining adds significant cost and means that achievable forms are limited to those which can be machined.
Read more at ENGINEERING.com