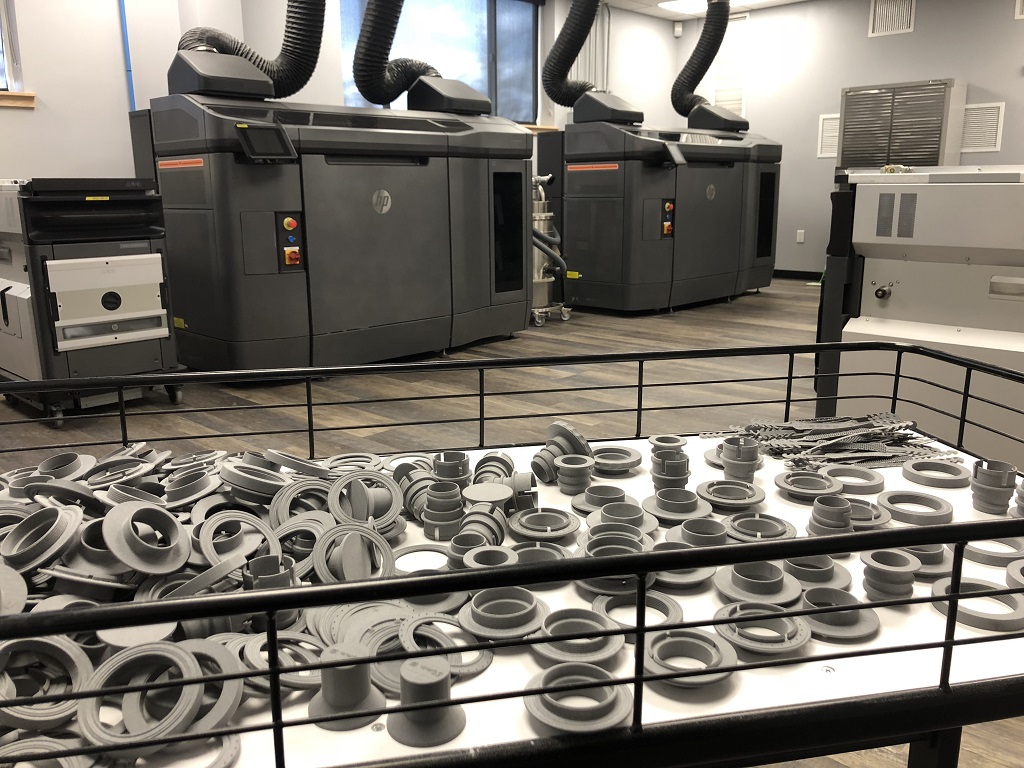
HP shares details of their internal and external teamwork to bring 3D printing into play to join the fight against COVID-19.
We’ve looked into a bit of HP’s strategies and approaches to pandemic response, and I recently had the opportunity to connect with a company exec outside of the HP 3D Printing business to dig further into the mechanics behind their mobilization.
HP Response Mobilization
One of the benefits of working in a massive multinational corporation is internal access to a breadth of technologies and expertise. One of the drawbacks tends to be actually accessing them, as red tape tends to be plentiful.
Extenuating circumstances tend to cut down barriers, though, as a strong united message and mission can expedite access. For HP, that rapidity was well in evidence with a two-day turnaround from a request to first shipping.
Dr. James Kirby of Beth Israel Deaconess Medical Center (BIDMC), part of Beth Israel Lahey Health, reached out to Annette Friskopp — Global Head & General Manager of the Specialty Printing Systems (SPS) group in the HP Inc.’s Graphics Solutions Business — on March 17th. The shortage of nasopharyngeal (NP) testing swabs was a major problem, and he thought perhaps HP might be able to help.
The SPS group has developed such technologies as the HP BioPrinter, which is among the technologies the company has been highlighting in its pandemic response, and one with which Dr. Kirby has experience. While that device wasn’t itself what was needed to respond to this request, Friskopp connected the dots internally at HP and quickly brought together internal leadership — from within HP’s CTO office, HP Labs, and the 3D Printing and Digital Manufacturing teams — to meet with BIDMC’s Dr. Kirby and Dr. Ramy Arnaout, associate director of the Clinical Microbiology Laboratories, as well as the BIDMC Chief Academic Officer and a member of their supply chain.
Two days later, on 19 March, the first swab prototypes made on Jet Fusion 3D printers were sent over to Dr. Arnaout for testing. Following close teamwork to iterate and develop a viable NP swab, the 3D printed design has been clinically validated.
HP shared the story themselves in a worth-the-read rundown here — and for more details on what’s been happening, and how, I spoke with Friskopp for the inside scoop.
HP Leadership Coming Together
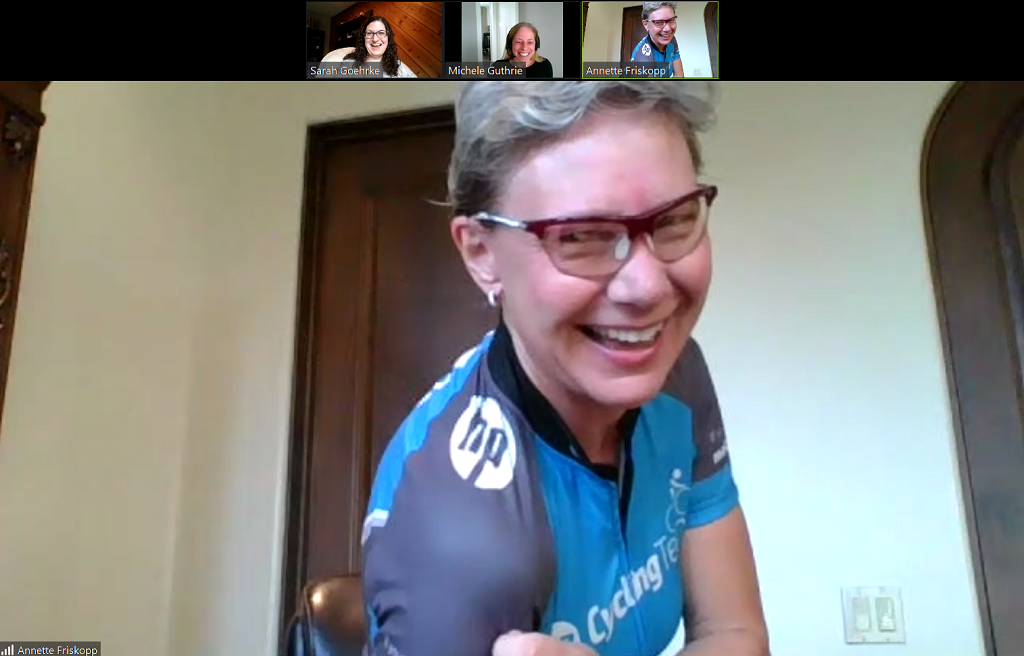
Friskopp has been with HP for just over a decade now, and has “had the joy of being involved in a lot of interesting projects along the way,” she explained.
Her SPS group is focused specifically on inkjet technology, working in the larger Graphic Solutions Business to “take inkjet cartridges you may find in other printers and put them into our massive web presses that are the size of a truck.” (She’s not exaggerating, either; I’ve stood next to those monster machines at HP’s Barcelona site.) The team also works on projects like printing expiration dates onto packaging, as well as the HP BioPrinter (the D300e Digital Dispenser).
“That’s what got me the background of working in the life science space and aware of FDA regulations, aware of the large players in the marketplace” she told me. “When COVID arose, we quickly were very involved — in the beginning of March, there were shortages, there were no tests. I received a call from my customer, Dr. Kirby, who has been working with the D300e, who told me about their shortage. I said certainly, I’ll help you find swabs. I put a call out to all my top senior contacts to customers who make swabs and they said, sure, we’ll help — but within 24-48 hours, we had confirmation there were no supplies to meet their needs. So we went to Plan B: we’ll see if we can do this as a 3D printed product.”
Friskopp then reached out to Ramon Pastor, who is heading HP 3D Printing and quickly got her in touch with the right people in their global operations. This quickly turned into a call with HP personnel and medical centers, with “probably 65 people on this call, looking at every aspect of this: we spoke with the head of surgery, the head of cardiac, the head of infectious diseases, on and on.”
To rapidly mobilize an effort like this one required a massive effort. Not only the technology to 3D print NP swabs and clinically validate them, but the supply chain to scale it all up to an effective solution and act effectively on a global scale.
The many people working together broke into work groups to address PPE shortages. Within 48 hours, the first samples of printed swabs were made: “The team just swung into action.”
“We pulled together this team of design, materials science, finishing and printing, and partners outside HP,” Friskopp said.
Following internal testing to nail down the design, test for compatibility, and get feedback from respiratory therapists, doctors, and patients, as well as clinical trials inserting the NP swabs into actual patients’ nosies — “the report came out by April 15 that we had notice our swabs had passed clinical trials.”
See part two of our discussion for more details in how HP worked together internally as well as with its global partner network to scale up these efforts.
Via HP