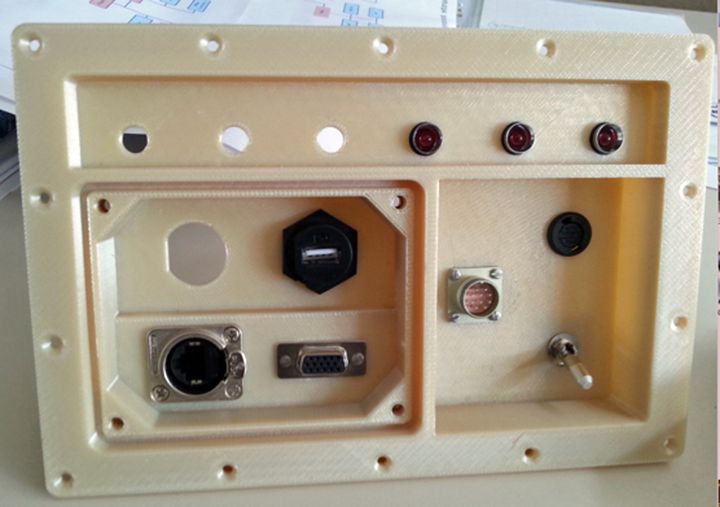
Weāve learned that the Italian National Institute for Nuclear Physics (INFN) has been producing 3D printed parts for end-use on the International Space Station.
3D Printed Mini-EUSO
What did they build? Apparently INFN 3D printed the mechanical structure for a new telescope called the āMultiwavelength Imaging New Instrument for the Extreme Universe Space Observatoryā, or āMini-EUSOā. This device is intended to observe ultraviolet emissions from both the surface of the Earth and beyond. Apparently its first task will be to produce a worldwide UV map.
While this may seem to be just another application of 3D printing, as plenty of projects have 3D printed the mechanical structure for a mechanism, this one is a bit different.

Being mounted on an external-facing window on the ISS, Mini-EUSO had to undergo perhaps the most rigorous of certifications a component can withstand in manufacturing.
Along with all the usual mechanical, thermal, vibratory and electrical testing, the part had to undergo even more tests, such as emissions testing: in the closed space of the ISS, air pollution is simply not acceptable. The parts absolutely cannot emit gases or particles in expected scenarios.
The parts were developed and 3D printed on a Stratasys Fortus 450mc in ULTEM 9085 material. This FDM process is widely used for prototyping but also for end-use parts with appropriate materials, as is the case here.
3D Printed Parts For Space

The designers at INFN found the 3D printing development process to be exceptionally beneficial, as it reduced their development time by over a year and reduced their costs in a similar manner.
Beyond the administrative benefits, the parts were actually lighter than aluminum alternatives, which would have been the choice before the introduction of 3D printing options. ULTEM also offers high heat and chemical resistance, and is quite strong. Itās typically used in the aerospace industry, for the same reasons itās being used on the ISS. However, gaining acceptance for an ISS application is a bigger deal than it is for most aerospace applications.
This is one of the first times Iāve heard of end-use parts being produced for installation on the ISS. Yes, there have been several experiments onboard using space-adapted 3D printers of various styles, but those were not intended to make end-use parts. Astronauts did make themselves a wrench at one point, but this was not a planned activity.
3D Printed Space Parts Economics
Thereās an interesting economy taking place in this scenario that is not something that would take place on ground-based applications.
First, consider that many times 3D print options are discounted by designers because the cost of 3D printing exceeds the end-use value of the part. Why 3D print a jar lid for US$2 when you can make an injection molded lid for US$0.01?
But in aerospace the equation is a bit different.
Weight counts, and counts a lot. Every gram that is placed aloft requires energy to put it there, and that energy costs, and sometimes costs a lot.
How much? Letās figure it out. Currently SpaceX charges around US$60M per Falcon 9 flight, and those vehicles can carry up to 22,800kg to low Earth orbit (LEO). Usually the payload is less than the maximum capacity, but letās go with that for calculative purposes.
This suggests a per kg cost of US$2,632 to LEO, or a per gram cost of US$2.60. In reality the cost per kg will be higher than that due to the less-than-100-percent launch capacity used. Thatās far more than the cost of the Stratasys certified ULTEM 9085 material, which goes for something close to US$0.37 per gram these days, seven times less.
In other words, the cost of the material literally doesnāt mean anything in this equation!
It may be that this project could demonstrate a breakthrough for 3D printed parts on future ISS components or other space missions. If these benefits could be obtained by other projects, then why not?
We may be seeing a lot more 3D printed items above our heads in years to come.
Via Stratasys