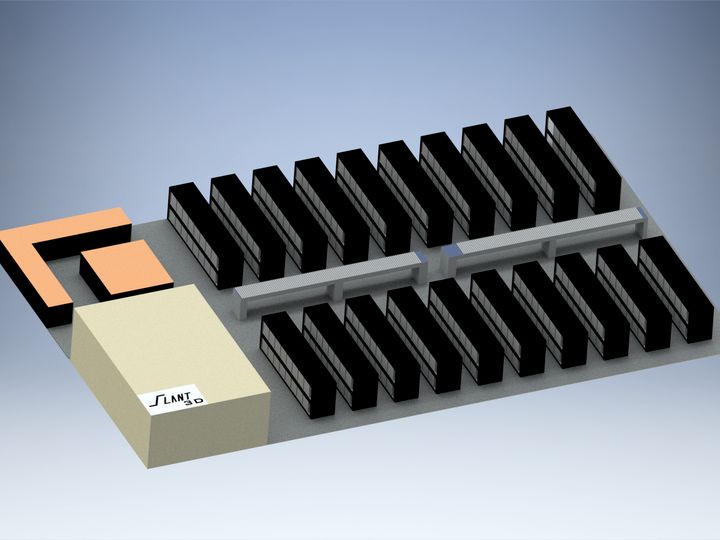
The idea of parallel 3D printing is incredibly powerful.
The rap against 3D printers has long been that they are monumentally slower than traditional manufacturing equipment to produce finished units, even though they are able to make objects of any design on the next print job.
This slowness has sometimes been the reason for not considering 3D printing as a manufacturing option, along with the unavailability of desired materials. However, in recent years the breadth of material selection has widened considerably, and now includes many popular engineering materials.
Itâs now possible to make many types of end-use parts on 3D printers, but they are still slow.
But that constraint can be overcome with parallelism. If a single device takes two hours to produce a part, then 100 devices can produce 50 parts per hour. Slant 3Dâs Gabe Bentz explains this well in his 2018 TEDxBoise talk:
I spoke with Bentz recently to find out more about this concept and specifically what is being done at Slant 3D.
Bentz explained that his company, Slant 3D, is attempting to produce a large-scale manufacturing operation based solely on 3D printing technology. He says they now operate the âlargest 3D print farm in North Americaâ, with a âcouple hundred machinesâ all capable of operating in parallel to produce thousands of parts on demand.
Bentz says they currently are focused on jobs ranging from 10-20,000 pieces, and even take on jobs requiring 100,000 parts.
This is all part of a larger plan, according to Bentz, who is approaching this in stages. âPrint Farm Alphaâ, which is now complete, was the stage where they developed their farm system technology.
Mason 3D Printer
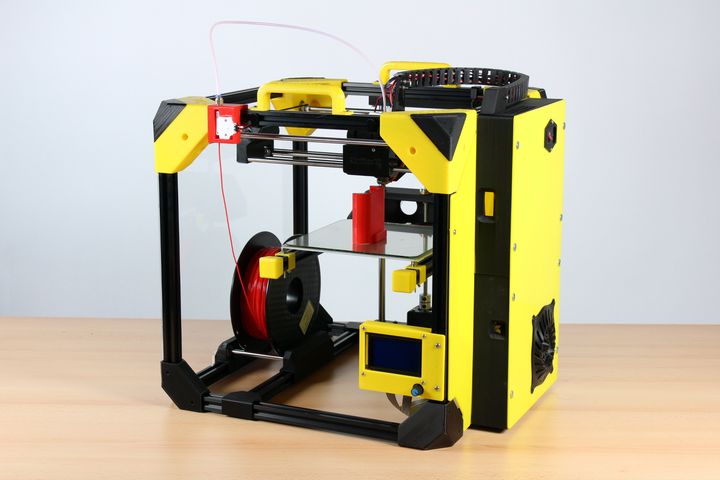
This includes a custom-made 3D printer, the Mason 3D Printer, which has an ability to eject completed parts all by itself.
I asked Bentz to reveal the secrets behind this ejection mechanism, but he wouldnât say much, as itâs a key strategic advantage. I was able to determine that it has to do with a sophisticated bed adhesion system that allows the part to be released under some form of control. Ejected parts can land on a conveyor belt for collection.
Slant 3D has created a custom software solution that manages all the farm devices at once. Theyâve been able to develop an automated process that allows an incredible 150 live 3D printers to be managed by a single operator.
Print Farm Beta
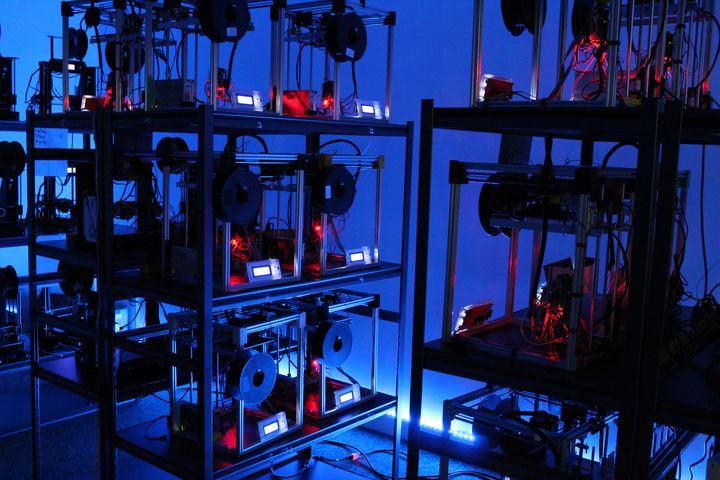
Currently Slant 3D is in the midst of building âPrint Farm Betaâ, which is a vastly scaled-up version of the equipment and process they developed during Print Farm Alpha. The goal here is to have an incredible 800 3D printers simultaneously in 24/7 operation. By Bentzâs arithmetic, this suggests theyâd need only half a dozen people to manage such a site.
When complete, Print Farm Beta might well be the largest 3D print facility in the world, possibly exceeding Prusa Researchâs 500 machines. A concept diagram appears at top. Bentz says:
âOver the next year we will be completing Print Farm Beta. Which will give us a break even with injection molding of nearly 100,000 parts on average.â
3D Printing vs Injection Molding
This is an intriguing result, as Slant 3D would then be able to take on a massive order immediately, since competing injection molding operations would have to wait for molds to be designed, tested and produced. Meanwhile, arrays of 3D printers need only be sent the next job to execute.
I asked Bentz whether they sell the Mason 3D Printer, and the answer is basically no. However, they will sell individual units to customers so they can test prints to simulate what theyâd receive from Print Farm Beta.
Bentz says the array configuration will solve the speed problem, but now the industry still faces the design problem. Before committing to such massive amounts of 3D printing, parts will have to be properly designed for production on 3D printers, and thatâs a skill thatâs still pretty rare these days. Bentz says:
âIf youâre designing for 3D printing you want to minimize surface area and donât worry about part volume; thatâs just the opposite of what youâd do with injection molding!â
FFF For Array 3D Printing
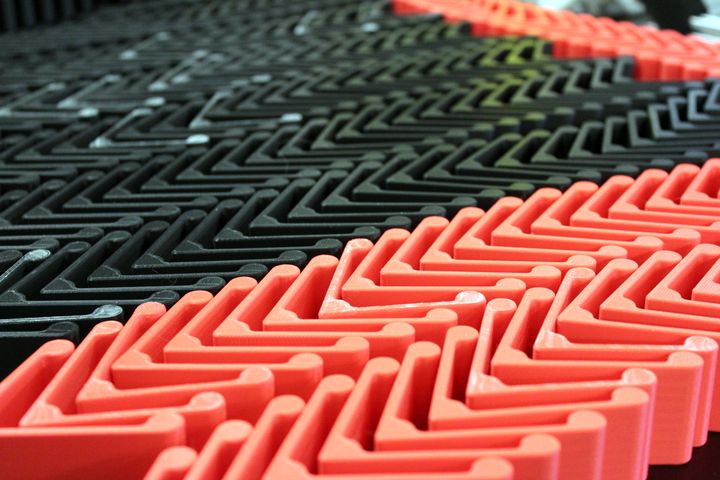
I asked Bentz why focus on FFF-style 3D printing when there are other 3D printing processes available that can supposedly achieve high throughput. He believes that âFFF is the only 3D printing technology that can achieve production scale at a good cost.â
Print Farm Gamma
I asked Bentz whatâs next for the company, and he explained a rather dramatic leap for the next stage of company development:
âWe will be building Print Farm Gamma to serve as a full digital warehouse and distribution center. That will be able to print and ship individual parts at the same cost as if they had been made with traditional manufacturing by the millions. This will mean that anyone in the world can design a product and have it manufactured and delivered to potentially millions of people for basically the cost of hosting a website.â
Many years ago I wrote about a futuristic concept I called the âAnything Factoryâ, where a static factory can run 24/7 making literally anything requested.
It may be that Slant 3D is building one.
Via Slant 3D