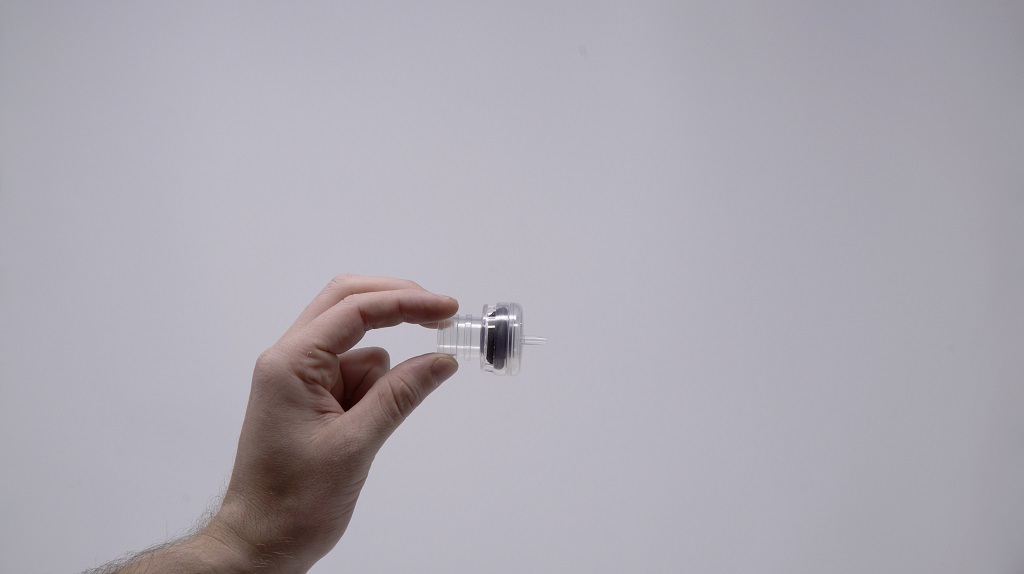
The 3D printing industry has been a beacon of manufacturing hope during the pandemic outbreak — thanks in large part to materials that have proven up to the task.
While some of the most widespread 3D printing efforts have been centered around personal protective equipment (PPE), one application that has been on a meteoric rise to the tune of millions of pieces produced has been nasopharyngeal (NP) swabs. These swabs are used in the uncomfortable up-the-nose test to determine whether an individual has COVID-19 — an all-important testing piece that was initially in far-too-short supply from traditional suppliers.
Resin-based 3D printing processes have proven up to the task of creating the thin, strong, flexible swabs needed for this testing. The swabs must be comfortable enough for patient cooperation, especially with so many test sites using self-testing — and they must be long enough to reach to the back of the nasal cavity, flexible enough to navigate the route back there, and strong enough to not snap inside a person’s head.
Ventilators too have required more parts to be developed and made to help those patients suffering some of the worst complications of this new virus. 3D printed diaphragms offer faster development and turnaround time to keep these life-saving devices operable. There’s a good amount of finesse that’s gone into these pandemic-response designs.
But it’s not just about the design: those qualities require a high-quality material to make such devices. And that’s where companies like Adaptive3D come into the conversation.
I spoke recently with Adaptive3D’s Dr. Walter Voit, CEO and Founder, and Kial Gramley, Vice President of Sales and Marketing, to catch up on the premium additive manufacturing polymer resin supplier’s creation of 3D printing elastomers for COVID-19 response.
Adaptive3D
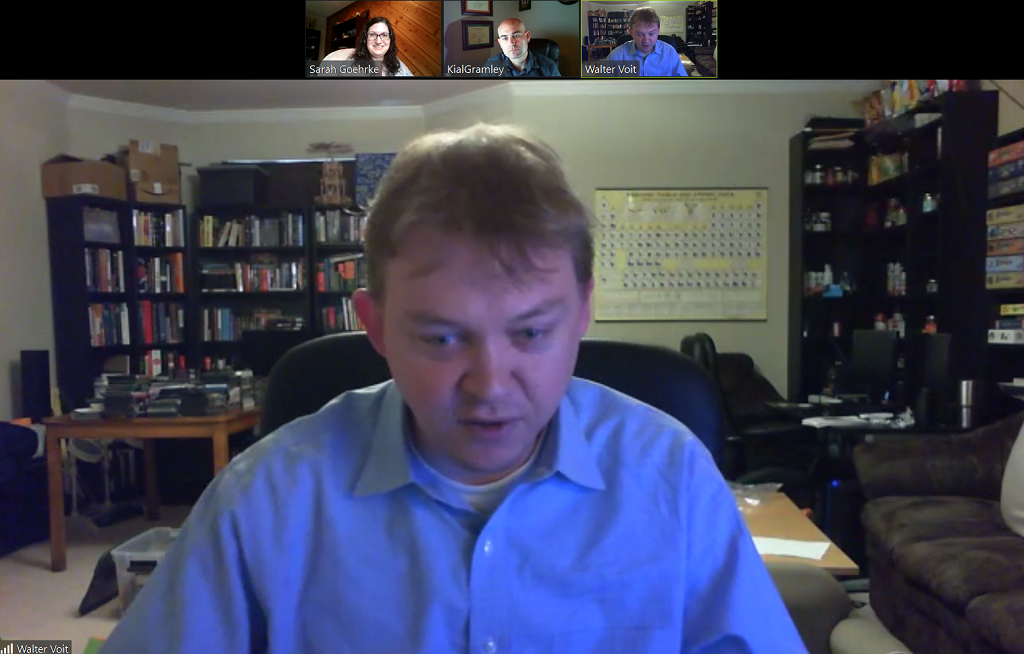
Dallas-based Adaptive3D was founded in 2014, based on a technology Voit developed at the University of Texas, Dallas.
The company is now in a high-growth state of its lifecycle, Gramley noted, adding that Voit has been “focused on growing the company, developing the management team, taking the technology platform developed and commercializing it at scale.”
Adaptive3D saw its original funding from DARPA, and spent its first few years as an SBIR company. At the end of the SBIR lifecycle, Gramley said, the team “had spent a lot of time developing this technology platform and was ready to go to market and capitalize,” and during that time of building up toward commercialization was when he joined the team.
“We have a proprietary chemistry that imparts properties of softness and high strength,” Gramley continued. “We can take a common acrylate material for DLP, make it very tough, give it high strength, make it very flexible. Our materials are essentially elastomeric. We have two off-the-shelf materials to highlight in these efforts: Soft ToughRuber, which mimics silicone-like properties with a ShoreA of 28, and is a very soft, pleasurable feeling material designed for auto parts, wearable parts, and anatomical modeling. At Formnext, we introduced Elastic ToughRubber 90, a higher-durometer rubber. ETR has a ShoreA of 90 and is excellent for footwear, tough enclosures, for any type of part trying to mimic polyurethane or rubber, where ETA will excel with very high wear resistance, durability, strain, and elasticity.”
These properties are where Adaptive3D “really excels,” he said: “those elastomeric-type materials leveraging DLP printing technology.”
Such property capabilities have drawn attention from the likes of materials giant DSM, which has invested in Adaptive3D.
3D Printing For COVID-19 Response
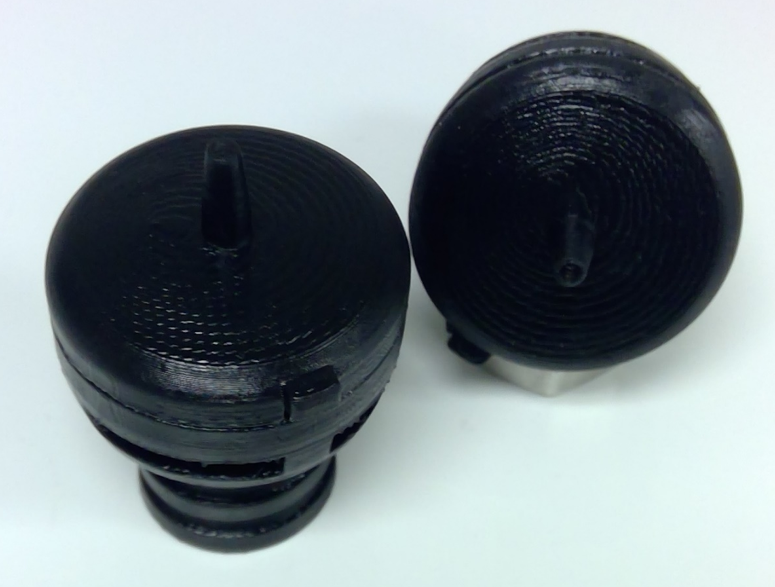
Those material properties have been proving their worth lately, as Voit examined with Adaptive3D’s work toward pandemic response.
The team worked closely with UT Southwestern and a medical center in Parkland, he noted, as they examined pieces made traditionally using rubber and took them back to UT Dallas, “where we ran them through micro-CT scanners, got high-resolution models, and reverse-engineered that, showing functionality based on industry-standard designs.”
They then built their own parts and submitted them to the FDA for emergency use approval. Adaptive3D has also worked with UT Dallas to set up a test facility with Texas Instruments, and “built air handling systems that could do air handling tests.”
“We had components designed for LTV1200 ventilators that can be used for COVID or other patients where they’re in short supply. In three weeks, we built devices that function like standard devices that are in short supply,” Voit said.
For NP swabs, Adaptive3D has been working with the 3D printing community, including conversations with EnvisionTEC, Carbon, and Formlabs — all of which are 3D printing test swabs at scale. “We’re all in this together,” Voit said of these conversations.
“Our ETR material becomes important here. Published studies have shown that PU rubbers have the fewer false positives and false negatives compared to traditional swab materials, and we seek to demonstrate similar results with our materials. We’re working to rapidly build these out of functional rubbers, we’re among the only companies that can simultaneously develop stiff and strain capabilities,” Voit said. “Our technology lets us print in this golden zone on the stress/strain curve that medical device customers want for highly functional rubbers that are stretchy and tough. Elastic ToughRubber90 has low-temperature survivability down to -60C, which is great even at the lowest temperatures for shoes, and has tear strength about double that of some of the other competitive photoelastomers out on the market. It’s a highly tough material.”
For COVID-19 response, the company was able to rush through the ISO 10993-5, where they “passed with flying colors,” as well as NAMSA cytotoxicity tests for ToughRubber HT to use it for rapid pandemic response, Voit added.
For Adaptive3D, the pandemic has certainly been a disruption — but as with so many in the 3D printing industry, it is also a proof point of technological validity.
“We have interesting designs for swabs and other things,” Voit told me. “We are an emerging, high-growth company with strategic investors including Applied Materials, DSM, and Chemence, and are getting to know our customers. We are working not just to sell a material, but to develop and position materials for high-throughput additive manufacturing.”
For more detail on some of the Adaptive3D response to COVID-19, Voit also spoke at the Functional Elastomers for Additive Manufacturing webinar hosted by SME, discussing the development of a life-saving rubber diaphragm for ventilators:
Via Adaptive3D