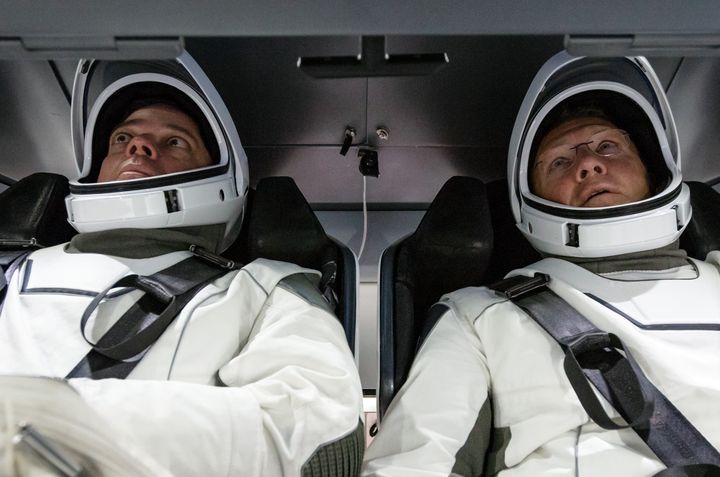
I’m seeing another reason companies will increase their adoption of 3D printing, and this time it’s at the top end of a rocket.
Last week NASA and SpaceX launched the first human mission onboard a commercial spacecraft, SpaceX’s Dragon capsule. As this was the first mission there were many new components being tested for the first time in action with real, live humans. Among these were the unusual spacesuits that have garnered both positive and negative reviews from fashionistas.
SpaceX 3D Printed Helmets
Another new component is the helmet for these futuristic space suits. They’re just as advanced, but perhaps less noticed because eyes are mostly aimed at the suit. According to a NASA press release:
“The helmet is custom manufactured using 3D printing technology and includes integrated valves, mechanisms for visor retraction and locking, and microphones within the helmet’s structure.”
This is the correct way to use 3D printing: design a complex structure that simplifies operational use and increases component quality, while ignoring the geometric complexities. Those complexities are less relevant if 3D printed, but critical if traditional manufacturing is being used.
Without the complex design this helmet would have had to include many separate parts, all of which would have to be separately manufactured and tested, assembled together and tested again. And at each joint there is the possibility of failure. The presence of joints can not only fail, they also require more weight and material to bind the parts together.
It gets worse: each separate part likely has an audit trail, instructions for use, assembly, disassembly, repair, etc. But by 3D printing the entire structure in a single object most of these concerns and effort evaporates.
That’s the essence of prototyping and production using additive manufacturing techniques: make something better because the design constraints have been removed.
While these helmets are clearly an interesting design, there’s much more at play here. The helmets were but one item among thousands that allowed SpaceX to achieve the unachievable: a private company literally built, in record time, a spaceship — and one that operates at vastly lower prices than existing players’.
SpaceX no doubt used similar advanced manufacturing and design techniques to produce the vehicle and all its support items, including extensive use of 3D printing, which I understand was also used in the production of their metal rocket engines.
3D Printing Competitive Drive
I’m thinking the total effect here on this particular industry could be profound. Here we have a number of established players in the rocket business, including Roscosmos, Boeing, ULA, ESA and others equipped now with apparently obsolete vehicles. Well, perhaps they still function, but their pricing is obsolete in the face of SpaceX’s vastly less expensive offer.
These companies will soon be forced into rethinking their entire operation, including their project management style, supply chains, manufacturing processes and certainly equipment design. They’ll want to catch up to SpaceX by developing similarly low-cost orbital vehicles, otherwise they’ll quickly be out of business.
In order for them to catch up they’ll surely adopt some practices pioneered by SpaceX in their industry. These practices will almost certainly include much more extensive use of 3D printing technologies. It’s possible a similar scenario could appear in other industries where one party pushes to the edge of the envelope with new technology like 3D printing.
It’s now clear this industry will rapidly change and that transformation will require many more 3D printers, and especially 3D designers experienced in DfAM — Design for Additive Manufacturing.
If I were running a 3D printer manufacturing company, I’d have a special squad of sales and business development folks heading to the rocket companies ASAP.
Via NASA