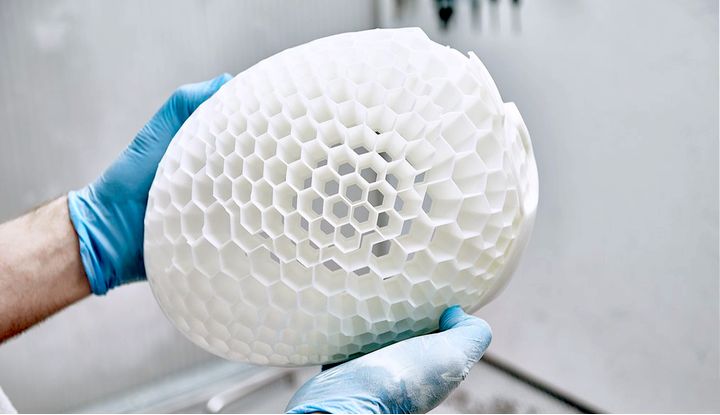
A helmet manufacturer is using distributed 3D scanning technology to produce bespoke products for customers.
HEXR is a London-based manufacturer of advanced premium cycling helmets. Helmets are a critical component for the high-end cyclist, as they not only provide protection, but also add weight and can disturb the thermal environment around one’s head. Thus it’s important to select the best possible helmet for competitive scenarios.
The company’s flagship product is a custom-fitted cycling helmet that is in fact partially 3D printed. We knew something about this previously, as they had been reported to be working with EOS on “digital foam“.
The key words here are “custom-fitted”, as this is an optimal use case for 3D printing. The technology is best used for unique products that would otherwise be too expensive to produce using conventional manufacturing methods. A 3D printer can simply print any geometry if provided with a suitable 3D model without delay.
Custom 3D Printed Products
Because of that we’ve seen a number of initiatives attempting to capitalize on that concept. One was a system to automatically generate eyeglass frames based on a 3D scan of a client’s face. These would, in theory, fit perfectly.
There have been multiple efforts in the footwear industry to develop custom-fitted shoes. Superfeet, Voxel8, OESH, and others have been working in this area. I should point out that there have been other non-custom-fitted shoes and footwear components also being 3D printed by companies like New Balance and Adidas. However, those ventures were simply seeking to mass produce highly complex components that could not easily be made otherwise, as opposed to fitting a shape to an individual customer.
The custom-fitted applications, however, have an additional problem beyond producing a 3D model and printing it: they must somehow capture the geometry of the customer and adjust their base model to create a custom version.
Scanning For Custom Products
This can be quite difficult to do, as 3D scanning has traditionally been a process that requires special equipment and expertise to operate. This required customers to physically appear at a scanning station, which obviously is detrimental to sales as many people can’t access them easily. However, things seem to be changing.
One approach has been to install a kiosk with the necessary capture equipment and software present. An example of this is the eyeglass system mentioned above. However, that again requires a participating retailer to install the kiosk and any time you have distributed hardware, there’s a management price to pay to keep them operating.
Some ventures capture the necessary information by having the customer take a couple of images of the body part involved. Then the company’s advanced software somehow interprets the images provided and maps them to known 3D models for production.
But as mobile devices increase in capability, specifically the ability to capture 3D scans, this can change. That seems to be what HEXR is doing.
To produce a custom-fitted cycling helmet, they need a rather detailed scan of the subject’s head. Obtaining such a scan is quite difficult because even if you built an app to do the scan, many clients’ hair would prevent successful captures. This problem was seen specifically during our recent review of the Calibry 3D scanner, where we were unable to 3D scan hair at all.
Somehow you have to remove the hair from the equation before the scan can take place. Perhaps you could momentarily consider asking the client to shave off their hair, but that’s a big ask.
HEXR Manufacturing Process
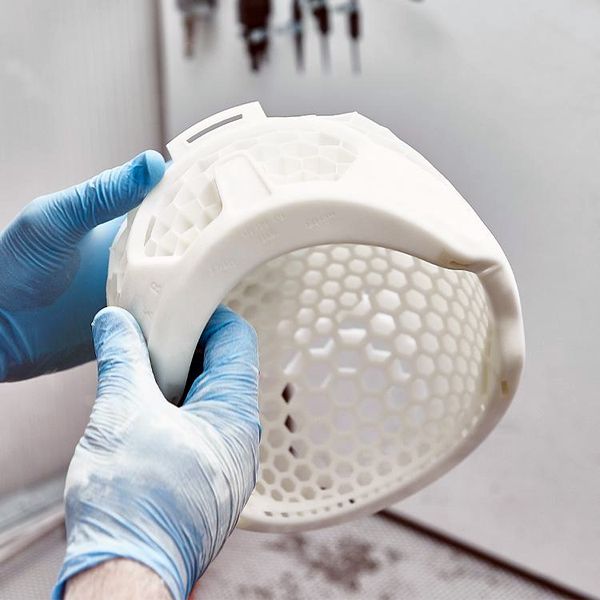
Instead, HEXR has come up with a unique approach to obtaining the head scan. Here’s how it works:
- You place an order for one of their custom fitted helmets
- They send you a “scanning cap” by courier
- You wear the cap tight to your head, which flattens your hair (and likely ruins your hairstyle, too)
- You use their mobile app to scan your head
- The app makes use of markings on the scan cap to assist in the scanning process
- The app sends the 3D model to HEXR
- HEXR maps the data into a custom 3D model
- HEXR 3D prints the model at their provider, 3T Additive Manufacturing, a UK-based 3D print service, on EOS equipment in nylon material
- HEXR adds a shell and packages it up for delivery
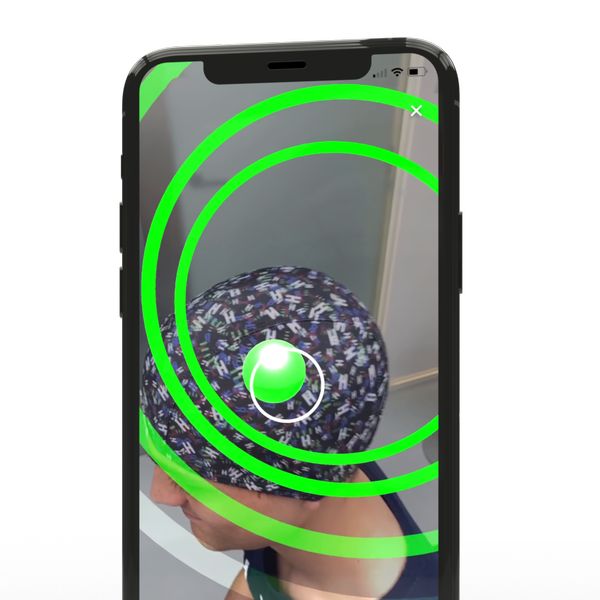
The key to their process is the scanning cap. It is a simple and inexpensive apparatus they can easily send to serious clients that vastly increases the probability of scanning success. Thus the process is a combination of an app AND a separate device.
I’m wondering if this approach could be used in other areas to increase the scanning capability and thus make it feasible to provide other types of custom-fit products.
What are your ideas? What kinds of custom-fit products would you like to see on the market?
Via HEXR