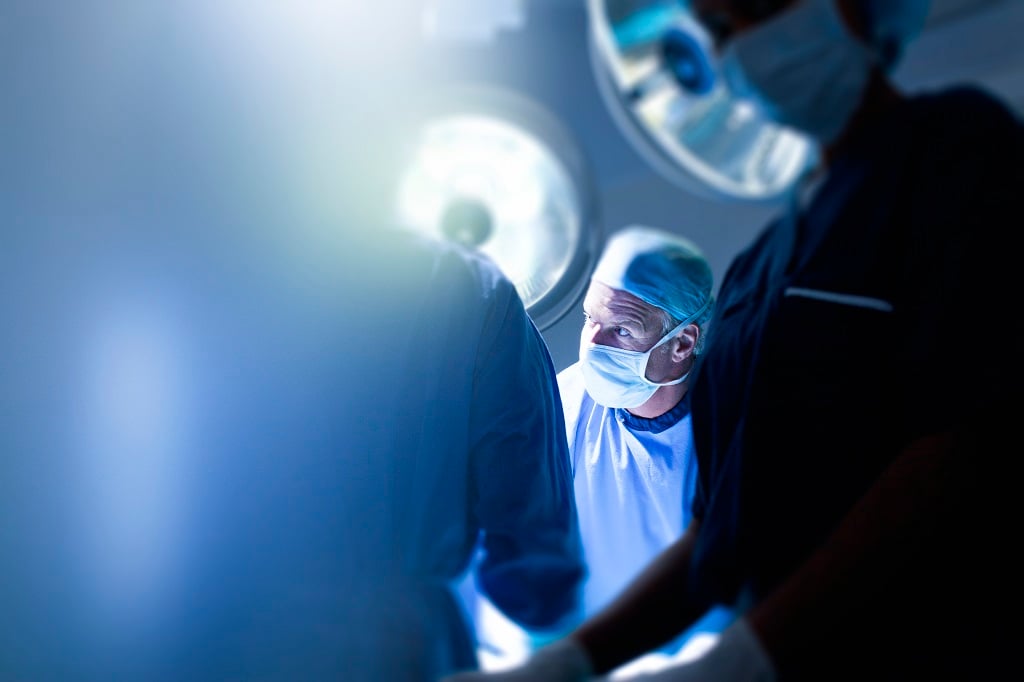
Charles R. Goulding and Ryan Donley explore a recent acquisition’s potential impact on medical 3D printing.
Medtronic, one of the global leaders in medical technology, announced in June 2020 it will be acquiring Medicrea, a spinal surgery company with 30+ FDA approved spinal implant technologies that have been utilized in over 150,000 spinal surgeries to date. Medicrea leverages software analysis tools and scientific data to streamline efficient spinal care solutions.
Medtronic operates across numerous medical technology networks including cardiac devices, cranial and spine robotics, insulin pumps, surgical tools, patient monitoring systems, and many more. The acquisition of Medicrea expands Medtronic’s already deep portfolio as this adds to their spinal solution profile as the advent of new digital technology will offer the ability to custom spinal implants. Medicrea’s dedicated 3D manufacturing facility will fit right into the flow of Medtronic’s activities as they expand upon their ability to develop custom medical products through the use of 3D printing. This is especially necessary for the field of spinal medical solutions due to the difficulty in fitting designated single products or procedures to a unique patient.
According to Medicrea CEO and founder Denys Sournac, “Spine surgery is one of the more complex procedures in healthcare because of the high number of different parameters to take into consideration, it is impossible for the human brain to compute all of them for one single patient.”
Investment in research and development in the Medical and Health sector far outperforms any other sector as spending grew by a total of 6.4% from 2018 to 2019 for a total of $194.2 billion. An example of R&D spending expense per employee is represented below for Medtronic and Medicrea:
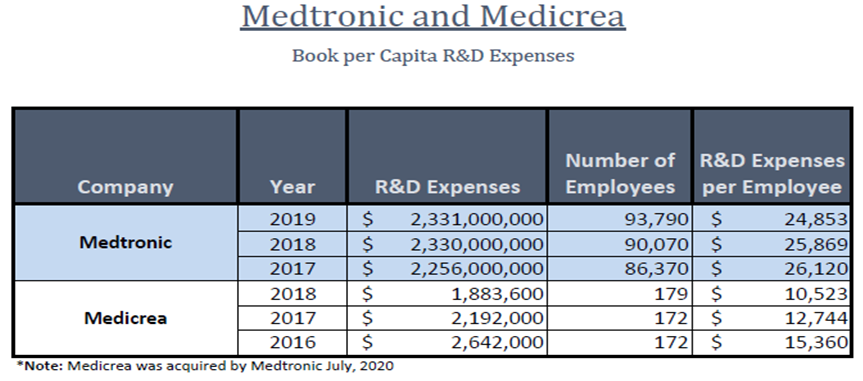
Examples of Medicrea 3D Printing Medical Practices
IB3D-TB
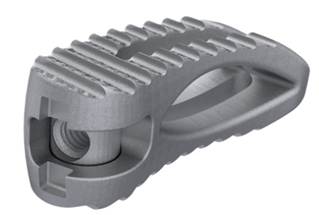
[Source: Medicrea]
The IB3D is a 3D printed titanium implant designed to facilitate cage insertion and placement. The optimized Hexalock design is a proprietary lock that possesses rough titanium to elicit stability and bone fusion. The implant features an increase of bone to implant surface by 40% and will increase the fusion visibility on imaging technology as well as maximize bone graft volume. The IB3D also features a self-articulating mechanism and Bullet Nose design that is smooth and tapered for advanced impact and insertion. Much of the IB3D capabilities and design would not have been made possible without extensive experimentation into 3D printing methodology and equipment.
Spinal Cages/Rods (UNiD ALIF)
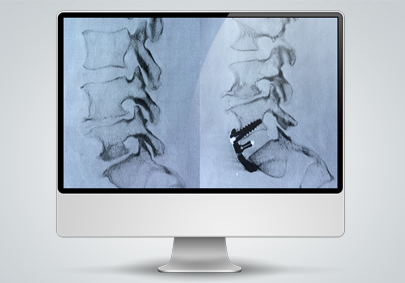
Medicrea was a large part of the world’s first spinal fusion surgery using customized 3D printed spine cages as they provided the spine cages which were 3D printed in house at a Medicrea facility. The unique spinal cages were customized to the patient’s needs for the surgery and the Research and Development team at Medicrea invested in R&D to come up with the spinal cage used in the surgery. Particularly, materials can be challenging to choose from as medical technology should be implanted in such a way to mimic what was previously there and perform as intended within the patient. The Medicrea team utilized a Poly Ether Ketone Ketone (PEKK) material that was capable of exactly reproducing the anatomical details of the patient’s vertebral plates.
Examples of Medtronic 3D Printing Medical Practices
TiONIC
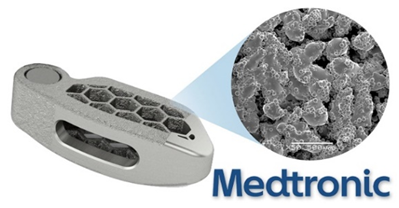
Medtronic has been heavily involved in the spinal implant medical technology area as in 2018 they launched their own line of 3D printed titanium spinal implants called TiONIC. The implants are developed with enhanced surface textures to promote bone response and osteoconductivity. The innate ability of 3D printing and additive manufacturing has allowed Medtronic to enhance interbody implants more so than traditional manufacturing methods. The Artic-L spinal implant from TiONIC was even found to distribute load across the implant far better than traditional implants. Dr. Colin C. Buchanan, a neurosurgeon at the Colorado Brain and Spine Institute commented on the implant, “Surface advancements, like TiONIC Technology, have emerged as a paradigm shift in interbody fusion implants, Implants utilizing newer surface technology can help stimulate a cellular response and give me greater confidence that the patient will have a successful fusion.”
Prototyping
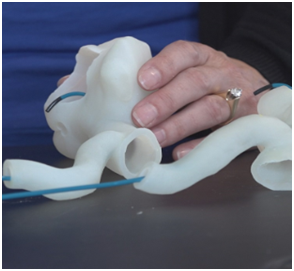
Medtronic has a large 3D printing prototyping practice where models of various human anatomies are developed for numerous applications. Some prototypes are developed to determine how the products can improve before being deployed and operated inside the human body. Other prototypes developed by Medtronic are being developed for testing of medical tools where surgeons can practice and utilize new tools on anatomical parts that look and feel similar. This allows surgeons a unique ability to go through procedures in abnormal physiologies with an added comfort as they benefit from the practice performance on prototyped parts.
Surgical Instruments
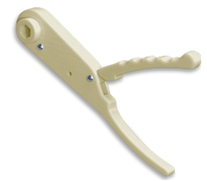
With advancements in additive manufacturing and 3D printing, prototype surgical instruments are being experimented with as well as being further developed into applicable tools for surgeries. An example of such a tool was a ratcheting counter-torque instrument that is used for screw fastening in implant surgery. Prior to the tool, surgeons were using multiple tools and both hands in order to perform the implant surgery, increasing the complexity and time to complete it. The goal of this new tool was to combine two tools used for the surgery into one. First iterations were developed in-house and sent out to hospitals for testing use. This allowed for feedback and changes to be updated on the tool quickly and facilitated rapid prototyping that would not have been achieved without the use of 3D printing.
3D printing and similar activities in the medical field may be eligible for the R&D Tax Credit, which is briefly described below.
The Research & Development Tax Credit
Whether it’s used for creating and testing prototypes or for final production, 3D printing is a great indicator that R&D Credit eligible activities are taking place. Companies implementing this technology at any point should consider taking advantage of R&D Tax Credits.
Enacted in 1981, the now permanent Federal Research and Development (R&D) Tax Credit allows a credit that typically ranges from 4%-7% of eligible spending for new and improved products and processes. Qualified research must meet the following four criteria:
- Must be technological in nature
- Must be a component of the taxpayer’s business
- Must represent R&D in the experimental sense and generally includes all such costs related to the development or improvement of a product or process
- Must eliminate uncertainty through a process of experimentation that considers one or more alternatives
Eligible costs include US employee wages, cost of supplies consumed in the R&D process, cost of pre-production testing, US contract research expenses, and certain costs associated with developing a patent.
On December 18, 2015, President Obama signed the PATH Act, making the R&D Tax Credit permanent. Beginning in 2016, the R&D credit has been used to offset Alternative Minimum Tax for companies with revenue below $50MM, and startup businesses can obtain up to $250,000 per year in cash rebates applied directly toward payroll taxes.
Conclusion
The acquisition of Medicrea by Medtronic presents a unique opportunity for further experimentation in the medical tools and technology field. Combining Medicrea’s 3D printing capabilities and spinal surgery expertise with Medtronic’s expansive portfolio of technology and data could lead to significant advancements in surgeries and patient care.