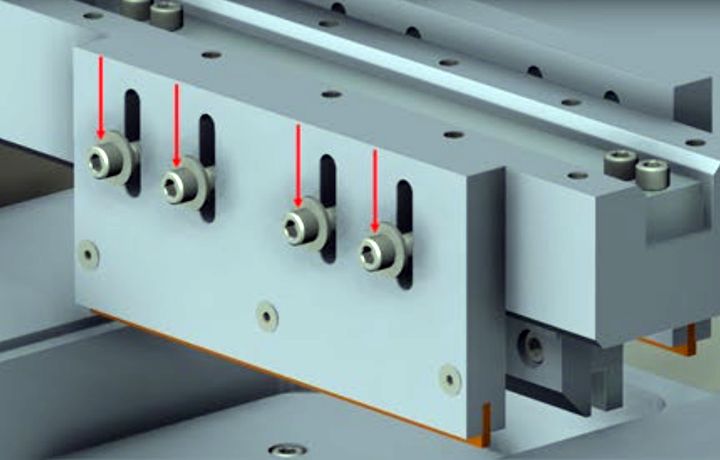
The world of 3D printer recoaters is even more complex after learning more about Open Additive’s approach.
Earlier this week I wrote a story about the complexities of 3D printer recoaters after reading a detailed discussion by Additive Manufacturing Consultant Michael Wohlfart. If you’re not familiar with the concept of recoating, you’ll find out more in that story. However, to quickly recap here I can tell you “recoating” is the process by which a fresh, thin layer of fine powder is distributed over the print surface in powder bed fusion 3D printers.
The “recoater” is the mechanism by which this process occurs, and it’s usually some sort of blade. The blade pushes and levels powder by moving across the build surface. However, there’s a number of issues that occur discussed in my previous story that cause one to choose between hard or soft blades. The decision depends on your intended outcome.
Open Additive PANDA
I thought that was the end of the tale, but then I read a very interesting comment on the story by Paul Hollowaty, the Global Sales Manager at Open Additive.
Open Additive is a 3D printer manufacturer that produces “open” powder bed fusion machines for 3D printing metal objects. Their fascinating machine focuses on the principle of “open” in every imaginable way. Their boxy PANDA device can be configured in so many different ways that they really call it a “platform”, rather than a “3D printer”. It includes a dizzying array of configurable items that seems to be far more than I’ve seen on any other metal PBF 3D printer.
You can read more about the PANDA and Open Additive in two of our previous stories where we discuss Open Additive’s background and an interview with Paul Hollowaty.
In his response to our post, Hollowaty said:
“Our PANDA recoater assembly includes a unique 3-blade design, compatible with both hard and soft blades. The recoater is designed with versatility in mind, and the user has the ability to use one or more blades at once, raise and lower the blades to preferred heights, use alternate blade materials and geometries, and even mount add-on mechanisms to the spreader using the provided set of threaded holes.”
Wait a second here — you can use MORE THAN ONE BLADE for recoating during a single 3D print job?
Multiple Recoater Blades
I took a further look at Open Additive’s documentation on their PANDA machine (PDF) and found the illustration shown at top, where you can clearly see multiple blades on their recoater. Evidently they have a mechanism to raise and lower them, which would obviously allow for selective use of a blade during a print job.
Many different types of blades could be used with this mounting system, including soft, ceramic, steel or other materials. Here’s a diagram of how blades are attached to the recoater:
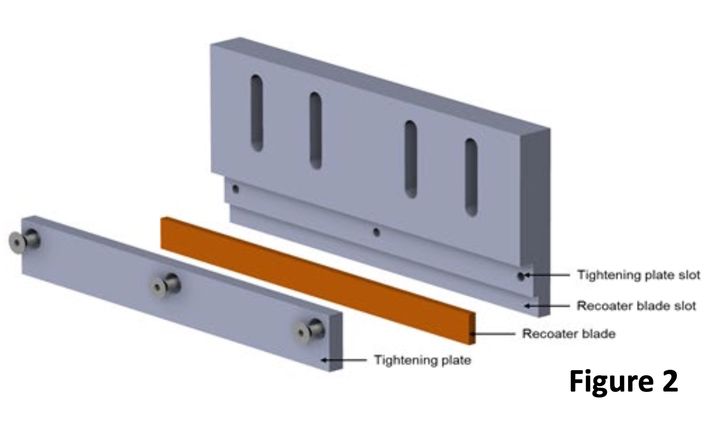
Why is this important? It’s because of the previous discussion on recoater blades, where one must decide which blade to use on a given print job. But wait, with Open Additive’s PANDA you don’t have to choose only one blade, you could use BOTH!
This means a 3D printer operator could examine the geometry of a 3D model and determine which blades would be best suited for each group of adjacent layers within a print job. In other words, you could get the best of both worlds. You don’t have to decide in advance which blade to use for the entire job, and in the process potentially compromise a portion of the 3D print.
While the PANDA has an incredibly long list of features, the multiple-blade recoating system is visible only in the fine print if you look through the documentation. This feature could be quite important for some users, so the moral of the story here is to always look through ALL of the specifications.
Via Open Additive