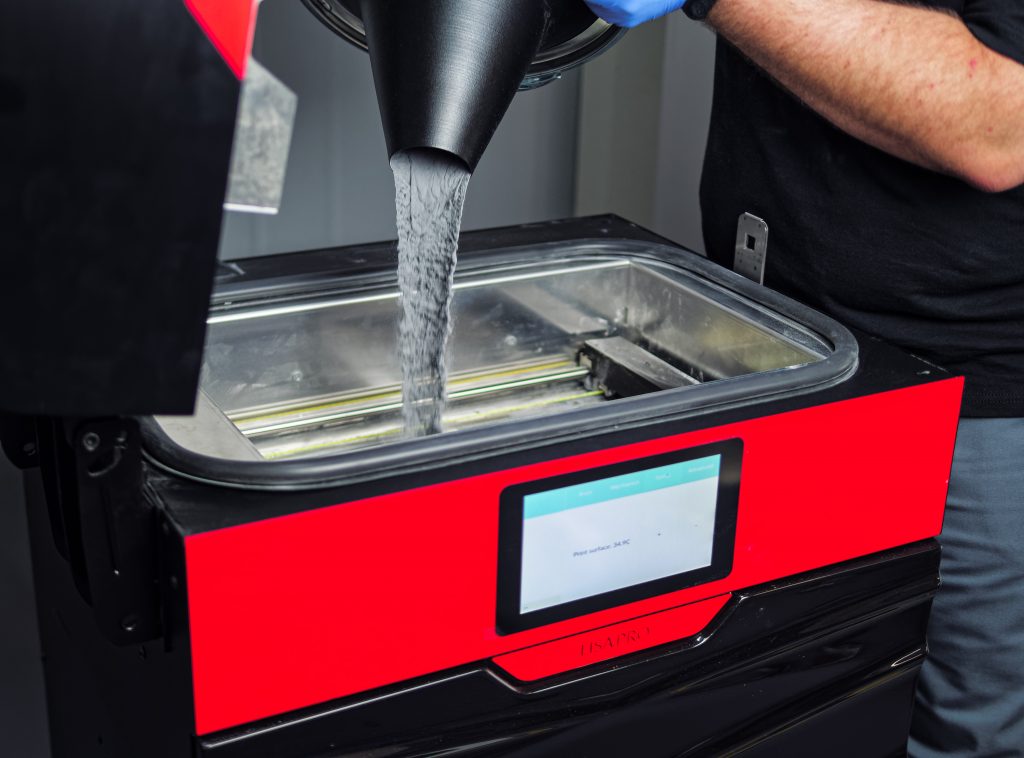
SLS 3D printing becomes more cost efficient as more powder can be reused.
Poland-based Sinterit has always been focused on enhancing the price point of powder-based 3D printing. They proved this with their very first market introduction, the desktop Lisa SLS 3D printer, in 2015. Whereas most SLS 3D printing happens on large industrial machines, and so is priced accordingly, the Lisa introduced us to a lower-cost approach to this technology. Other desktop SLS options have emerged since, but Lisa remains a high point in this small area of the 3D printing market, along with the follow-up Lisa PRO system.
This past March, when Sinterit moved to a huge new HQ, the company said it “ends the startup stage of the company.”
Sinterit SLS 3D Printing
Sinterit has been focusing on the serious business of running a more mature operation, and we’ve been seeing more indications of that maturity.
As our readers well know, the actual 3D printer is by no means the end-all of 3D printing. To create an effective solution, the full end-to-end workflow must be addressed. This includes not only the system, but its full use, including software, materials, and post-processing and other needed equipment, in addition to trained personnel. Once solutions exist in each of these areas, then the real work can begin: improving it all to the best it can be, at every step.
In April, Sinterit introduced new accessories to create a cleaner, safer SLS environment.
This month, they’ve already announced Industry 4.0 readiness, as a software update has enabled the Lisa and Lisa PRO to provide information needed for automated integration with factory logistics. Through this new “print monitor” function, the systems provide output communication of job status in its Sinterit Studio Software.
“The total cost of using the machine is the purchase of equipment, service, and material. We’ve just improved this third parameter, by lowering the amount of powder in the refreshing cycle. We’ve already revolutionized the cost of the system and service, now it’s time for reducing the cost of printing,” said Sinterit Co-Founder Konrad Głowacki, who is responsible for powder development.
SLS Powder Refresh
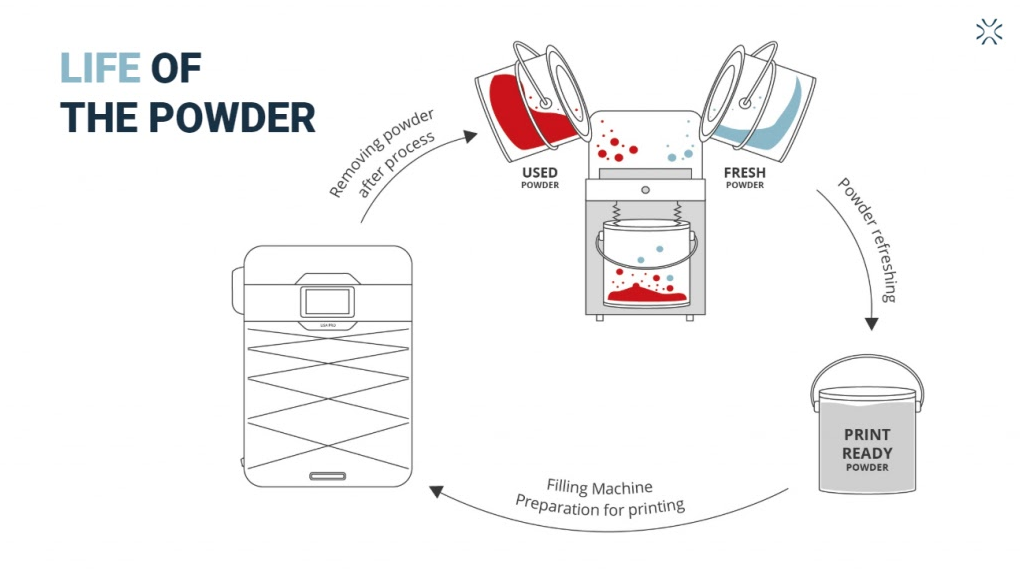
SLS 3D printing is a powder-based process. That powder represents a major expense, as does any consumable in an industrial workflow. Because not every bit of powder is sintered, though, much of it can often be reclaimed and recycled.
After initially running a new operation with only virgin material, ongoing SLS use can see a mix of material used, with both reclaimed and virgin powder together. A lot of materials science R&D is going into the exploration of just what those ratios must be for good quality results, as some virgin powder must still be used. Sinterit explains:
“What is important: not all the powder is sintered during the process. Only the part which builds the object. The rest of it works as a natural support. The unsintered powder can be reused in other prints just after adding some fresh powder.
The needed amount of the additional refreshing powder is responsible for the final costs of 3D printing in this technology. As you can easily assume, the lowest ratio of refreshing powder means the best ROI. Sinterit was always a leader in this aspect, but now the company lowered it even more to 26 percent.”
Sinterit lays out the pricing structure for its materials capabilities pretty clearly here:
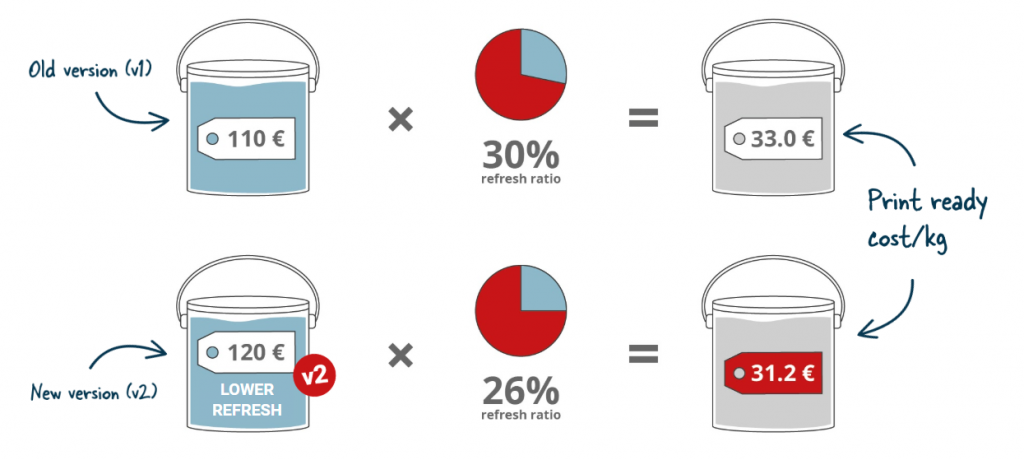
Previously, the first version of their PA12 powder cost €110 per kg; when mixed with reused powder at a 30% refresh rate, the material would be reduced to €33.
In version two, though, fresh PA12 costs €120 per print-ready kg. At a 26% refresh rate, that kg of PA12 powder now costs €31.20.
“Our way is to make 3D printing technology more accessible,” said Sinterit CEO Maxime Polesello, before hinting at more to come: “Lowering the cost of prints is just the next step. Not the last.”
Via Sinterit