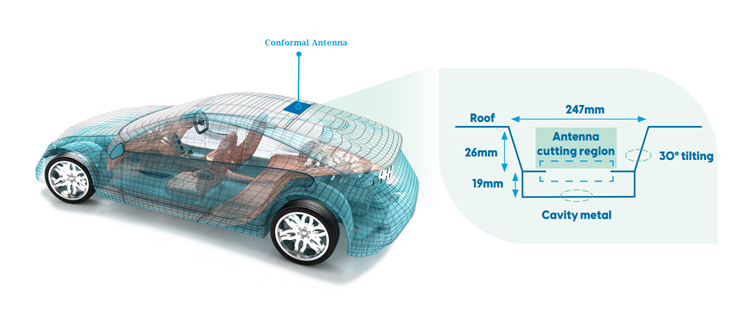
Conformal antenna in Samsung Company Car Model [Source: Harman]
Charles R. Goulding and Adam Friedman examine the use of 3D printing in producing conformal antennas.
Conformal antennas, also called phased array antennas, are antenna devices that are designed and produced on curved or pre-defined non-flat surfaces. Conformal antennas can group radio wave radiation in desired directions. Antennas can be applied to aerospace designs, wearable clothing, spacesuits, automobiles, military ships, and today’s mobile devices. The 3D surfaces and topographies of these applications have allowed for more frequent and high scale design.
The research and experimentation work of 3D printed conformal antennas has ramped up in recent years and has been a central research field at major research institutions. Some examples are from Dr. Eduardo A. Rojas-Nastrucci and his Wireless Device and Electromagnetics Laboratory at Florida’s Embry-Riddle Aeronautical University and Michigan State University’s Electromagnetics Research Group (EMRG) headed by Dr. Shanker Balasubramaniam and Dr. Edward Rothwell.
Conformal antennas are important because antenna devices can attach to structures, fully integrating with that structure without producing any drag force on the object on which it’s attached. Most people think of an antenna as the structure that protrudes out of satellite dishes, however conformal antenna products implant antennas so those are not visible for human observation. This allows antenna devices to be implanted with small antenna elements which together can transmit signals and electromagnetic communication in the frequency range that is commonly known as the Ka band.
The Ka band frequency range is a subsection of the microwave portion of the electromagnetic spectrum. This is a relatively novel frequency range and will have implications with making newer age performance-enhanced electronic devices. This has led to researchers, such as Dr. Craig Armiento of the Raytheon University of Massachusetts Lowell Research Institute (RURI), to conduct extensive research of microwave-based electronics integrating antennas devices.
Automobiles, Planes, and Ships
While there is still much research and development needed, existing conformal antennas manufactured for vehicles yield great radio communications power. Conformal antennas on top of automobiles are a perfect example of the technology. Conformal antennas are being utilized in automobiles receiving frequency waves for radio and satellite services.
There has become a noticeable decrease in cars’ drag as metallic antennas have been replaced by antenna element components inside car roofs. The new antennas conform to the surface of the car and are better able to receive radio signals for car radios.
In addition, the antenna capabilities are the reason that most United States military ships and aircraft are equipped with conformal antennas on the vehicles’ surfaces. Conformal antennas create more surface area for a moving body to transmit electromagnetic waves while also allowing vehicles to be designed with perfect aerodynamic curvature and with aquatic and hydraulic considerations. If military vehicles did not have conformal antennas, the amount of drag and subsequent fuel loss would be multiplied by the number of antennas these vehicles possess (upwards of 60-65 antennas on one vehicle).
Now, in 2020, producing conformal antennas with 3D printing and additive manufacturing technology is possible.
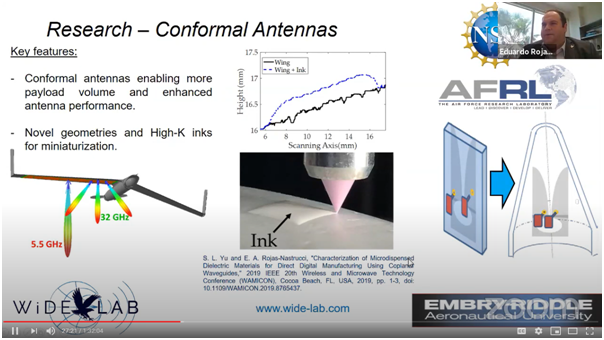
3D printing firm nScrypt together with its research group, Sciperio, has become the first company to 3D print a conformal antenna. The prototype that was installed in a drone device took 6 hours and research over the next decade will surely work toward and create a rapid prototyping model to 3D print conformal antennas in minutes.
Designers and manufacturers utilizing 3D printing technology to develop or produce conformal antennas may be eligible for R&D Tax Credits.
The Research & Development Tax Credit
Whether it’s used for creating and testing prototypes or for final production, 3D printing is a great indicator that R&D credit eligible activities are taking place. Companies implementing this technology at any point should consider taking advantage of R&D Tax Credits.
Enacted in 1981, the now permanent Federal Research and Development (R&D) Tax Credit allows a credit that typically ranges from 4%-7% of eligible spending for new and improved products and processes. Qualified research must meet the following four criteria:
- Must be technological in nature
- Must be a component of the taxpayer’s business
- Must represent R&D in the experimental sense and generally includes all such costs related to the development or improvement of a product or process
- Must eliminate uncertainty through a process of experimentation that considers one or more alternatives
Eligible costs include US employee wages, cost of supplies consumed in the R&D process, cost of pre-production testing, US contract research expenses, and certain costs associated with developing a patent.
On December 18, 2015, President Obama signed the PATH Act, making the R&D Tax Credit permanent. Beginning in 2016, the R&D credit has been used to offset Alternative Minimum Tax for companies with revenue below $50MM, and startup businesses can obtain up to $250,000 per year in cash rebates applied directly toward payroll taxes.
Conclusion
Conformal antennas are a technology that has been utilized for electromagnetic emitting devices. The architectural considerations and design elements for vehicles and devices have yielded great communication benefits. The ascent of 3D printing in this space continues the revolutionary technology that will increase electromagnetic communication without any interference.