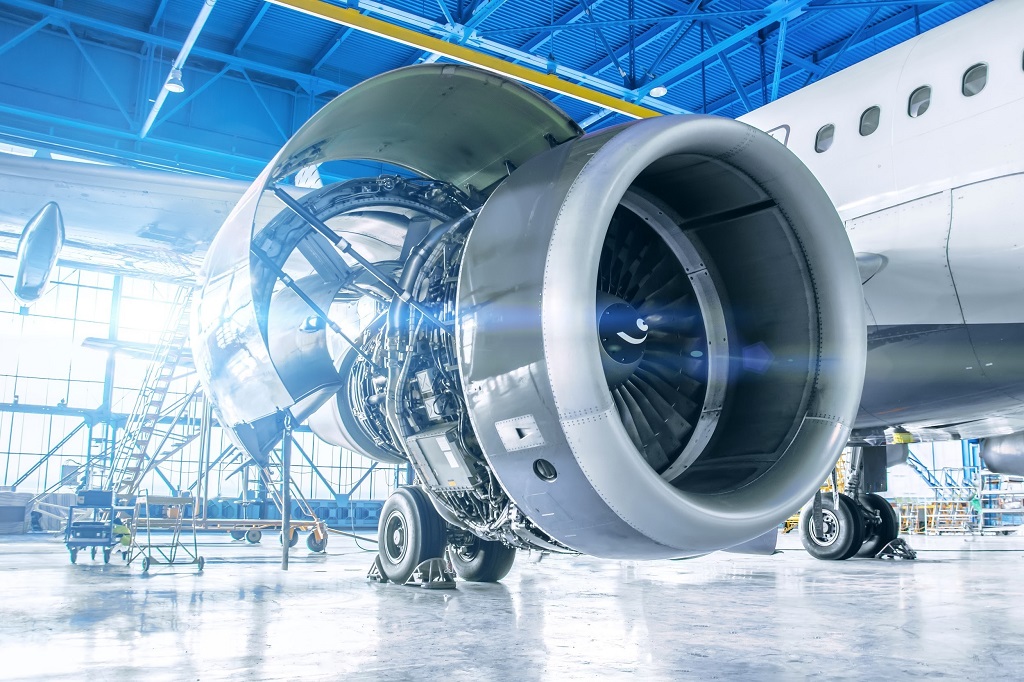
If real-world usage serves as a proof point, Optomec has just shared 10 million proof points in support of the validity of metal additive manufacturing.
Directed energy deposition (DED) metal 3D printing is a unique technology. Like other additive processes, it builds up — but it also offers the ability to build onto, and so can be used to repair and refurbish objects like turbine blades.
Optomec’s 10 Million Refurbishments
Optomec, which offers DED capabilities through its LENS metal 3D printers and Huffman-branded 5-axis Laser Cladders, has often targeted the repair market.
“There’s a lot of interest in repair, which suits DED best. Customers are interested in going to a digital maintenance warehouse instead of physical,” Marketing Director Mike Dean told me last year when we spoke about Optomec’s opportunities. “There are a lot of growth opportunities in repairing high-value metals: think oil and gas, with corrosion-resistant parts and repairs.”
And so those opportunities are proving out. The company recently surveyed more than 100 customer installations using their DED systems for gas turbine component repair. From that analysis, “Optomec has calculated that over 10 Million turbine blades have been refurbished.”
Just what are they repairing? Optomec explains:
“Common production applications include the repair of turbine blade tips, seals and wear surfaces; compressor blades, including titanium alloys; vanes, shrouds and other high value components.”
They also touch on why DED makes sense as a more cost-effective repair solution:
“Optomec’s automated solution typically replaces manual operations, such as Tungsten Inert Gas (TIG) welding, and drastically reduces the cost of routine maintenance. The ROI of Optomec’s machinery has been recently calculated to be in excess of 180%. In addition, Optomec’s laser-based processing provides superior mechanical performance due to its optimal metallurgy and minimal heat input, compared to manual operations.”
With 15 countries having approved Optomec’s metal 3D printers for us in aviation maintenance, Dean now says:
“Chances are that if you fly much, you’ve probably flown with an engine that was maintained with an Optomec laser cladder.”
Milestones In Additive Manufacturing
While anecdotally we often hear reports that metal additive manufacturing is an increasingly viable solution, often parsed in marketing language as being a “game changer” (*please stop saying this), there’s something substantially more…substantial when there are numbers attached. That’s why we pay attention to milestones: they speak, in numbers, to the realities of real-world installations and usage.
With additive manufacturing maturing as a technology suite, we don’t need more big claims. As Taylor Swift might say, we need the receipts. As my creative writing professor loved to say, show, don’t tell. In other words: prove it.
Real-world use cases prove out the claims of new technologies. With more customer success stories, the industry as a whole can continue to move forward.
The additive manufacturing sector is still something of a mysterious newcomer to the overall manufacturing industry. While those of us working with 3D printing day in, day out — in whatever capacity, be it writing, designing, 3D printing, post-processing, buying, selling — are by now familiar with the big claims (save time and money on tooling and labor, moving toward production capabilities, etc.), we’re still a minority in the broader manufacturing picture.
Substantiated numbers, hundreds or thousands or millions of successful real-world applications, are needed to continue to outwardly prove that, yes, additive manufacturing is viable today.
Also it’s a nice trophy for the shelf: congrats, Team Optomec, you’ve hit a great milestone with these usage numbers.
Via Optomec