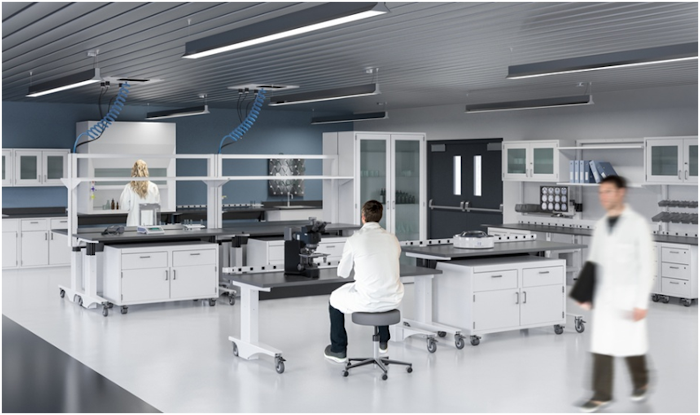
Charles R. Goulding and Preeti Sulibhavi consider 3D printing applications for wet labs.
The nationās major cities have advanced clinical care talent that is internationally unparalleled. But for these clinicians to be able to convert their untried ideas into actual medical and biotechnology products, local wet labs become vital. The problem then becomes getting clinicians in large metropolitan cities connected with wet labs, which are generally in more remote areas. The reason for the remote location of most wet labs is the large laboratory and equipment requirements that historically prohibited development in more urban, densely-populated cities where there are both spatial and economic constraints.
However, now, particularly after the global Coronavirus pandemic, ideas for better medical equipment and laboratory products are being designed and devised. And, to bring these ideas āto lifeā so-to-speak, wet labs are being developed and constructed.
While landlords are losing tenants in this Covid-19 economy, and city offices and residential apartment buildings are being vacated en masse, an opportunity emerges for wet lab space conversion.
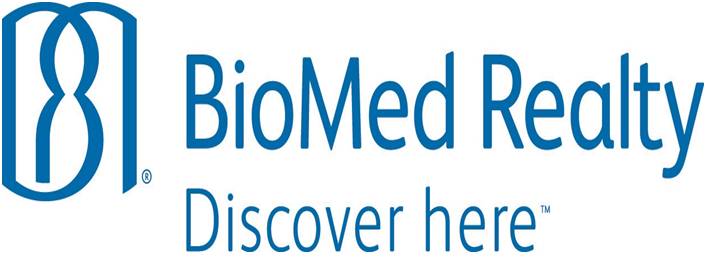
The real estate industry is witnessing this trend. The life science business has grown exponentially since 2016. Blackstone Group, Inc. acquired BioMed Realty and is expanding its portfolio to include 11 million square feet in life science markets throughout Boston, San Diego and Seattle. Brookfield Asset Management has purchased a 50% interest in Harwell Campus, a 700-acre life sciences campus near the University of Oxford, UK, for more than $251 million. Clearly, this trend is not limited to the US and is not going away.
Some do warn that there are hidden costs and expenses associated with life science properties that do not immediately meet the eye. Buildings for medical and scientific experimentation have to have sophisticated ventilation, gas, and water delivery systems that are far more complex than those of a common office building. That being said, not just anyone with a building in a city can convert their property into a fully-functioning wet lab.
These wet labs will be the workspace of many clinicians and will need 3D printed medical and laboratory equipment as well.
Wet Laboratories and 3D Printing
Wet labs require specialized equipment and supplies that are optimally produced via additive manufacturing or 3D printing. The global pandemic resulted in a myriad of 3D printed lab equipment. This includes masks, centrifuge tube/holders, conductivity testers, USB microscope stands, voltmeter/ammeter cases, etc.
Activities associated with 3D printed wet lab equipment design and/or development indicate research and development activity and may qualify for tax benefits.
The Research and Development Tax Credit
Whether itās used for creating and testing prototypes or for final production, 3D printing is a great indicator that R&D Credit eligible activities are taking place. Companies implementing this technology at any point should consider taking advantage of R&D Tax Credits.
Enacted in 1981, the now permanent Federal Research and Development (R&D) Tax Credit allows a credit that typically ranges from 4%-7% of eligible spending for new and improved products and processes. Qualified research must meet the following four criteria:
- Must be technological in nature
- Must be a component of the taxpayerās business
- Must represent R&D in the experimental sense and generally includes all such costs related to the development or improvement of a product or process
- Must eliminate uncertainty through a process of experimentation that considers one or more alternatives
Eligible costs include US employee wages, cost of supplies consumed in the R&D process, cost of pre-production testing, US contract research expenses, and certain costs associated with developing a patent.
On December 18, 2015, President Obama signed the PATH Act, making the R&D Tax Credit permanent. Beginning in 2016, the R&D credit has been used to offset Alternative Minimum Tax (AMT) for companies with revenue below $50MM and, startup businesses can obtain up to $250,000 per year in payroll tax cash rebates.
The Right Formula
While many are finding difficulty paying their rent (i.e. hotels, residential apartments, professional offices, etc.) most life science properties appear to be current with their rent, according to landlords such as Blackstone. Conversion of vacant residential apartment buildings and office spaces might not be the panacea for all Covid-19 related problems. But it does appear to be the right formula at the right time for many real estate developers.