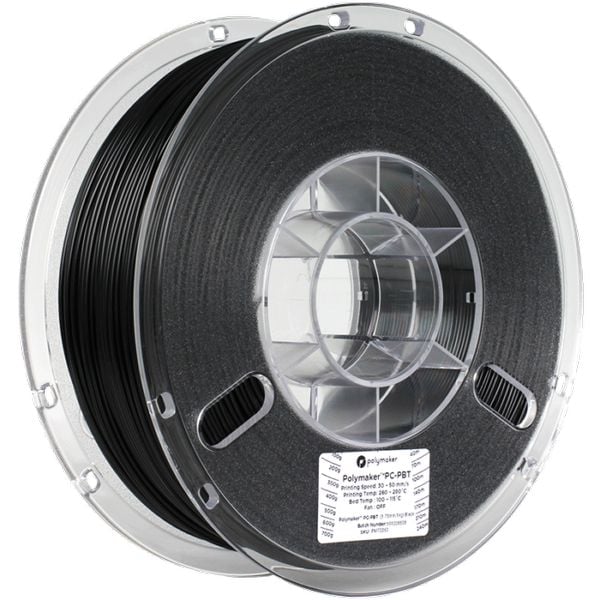
An announcement from Polymaker and MakerBot underlines the increasing importance of partnerships for 3D print materials.
MakerBot and Polymaker announced the certification of three new 3D print materials for the MakerBot METHOD line of 3D printers. All of the three are polycarbonate (PC) variants. They include:
- Polymaker PC-PBT: This polymer blend combines the good chemical resistance of PBT (polybutylene terephthalate) with the strength and toughness of polycarbonate. Compared to PC resins and PC-ABS compounds, PC-PBT offers better resistance to chemicals, which enables printed applications where resistance to intermittent contact with fuels, oils, lubricants, or cleaners is necessary. It performs well under extreme circumstances, whether in contact with hydrocarbon-based chemicals or operating at subzero temperatures. Polymaker PC-PBT is a specialty material that maintains good toughness and natural ductile fracture behavior at low temperatures.
- PolyMax PC-FR: A flame retardant (FR) polycarbonate material, PolyMax PC-FR meets the UL-94 V0 standard, an important fire safety specification. The material displays excellent toughness, strength, and heat resistance, making it ideal for applications within the automotive, railway, and aerospace industries.
- PolyLite PC: PolyLite PC is produced using a polycarbonate resin specifically engineered for 3D printing. This material demonstrates a high modulus, making it ideal for applications that require good stiffness and light diffusion, such as outdoor light housings. PolyLite PC is available in transparent color, showing good optical clarity, rendering parts with an attractive crystal shine.
This may sound like a routine thing, but in reality itâs not. Letâs look a little deeper at what actually is going on here.
MakerBot, now incredibly distant from its early days of seat-of-your-pants design and open source community, now focuses on the industrial and professional markets. These markets rightly seek the highest-quality 3D prints as their priority, and thatâs what the METHOD series has been designed to deliver. It includes a vast array of different sensors that allow the machine to tweak itself in real time to achieve the best possible 3D prints.
This is achieved by engineering control of the entire 3D printing sequence, including motion, thermals, software, print parameters and of course, material chemistry. This is why MakerBotâs print control software focuses on materials sourced from them: only when they know the exact material involved can they properly align the printing parameters to ensure the best quality.
But what if you want to use another material they donât offer? MakerBotâs answer to that is to use their experimental LABS extruder, which is designed to handle âunknown to MakerBotâ materials. Because of the âunknownâ, youâre basically on your own when it comes to 3D print parameters. MakerBot canât really help you because they donât know about the materials.
For many 3D printer operators, this approach is welcome, as they are comfortable iterating through test prints until the appropriate level of quality is achieved.
But for others, itâs problematic. They may not have the time, interest or skills to perform this iteration. Normally theyâd be limited to the known materials already included in MakerBotâs slicing software, but what if they require something different thatâs not in the normal MakerBot inventory?
Theyâre out of luck.
Fortunately, there is a way around this dilemma, and it is materials partnerships, of which the Polymaker / MakerBot arrangement is an excellent example.
In this case Polymaker was able to use MakerBot equipment to iterate through experimental benchmarks to derive the optimal print parameter settings. These are likely to produce better quality prints for most users than they could with their own settings. This is just what is required for professionals and industrial operations, where there is no time for experimenting.
The result is that these specific Polymaker products become part of the portfolio of MakerBot METHOD high-quality material options, just as if they were produced and sold by MakerBot themselves. Itâs a way to extend that quality bubble a bit wider in the material space.
This approach has been done by several other companies, some in unique ways. But the principle is the same: someone has to figure out the best 3D print parameters in advance, and itâs either you or your supplier doing it.