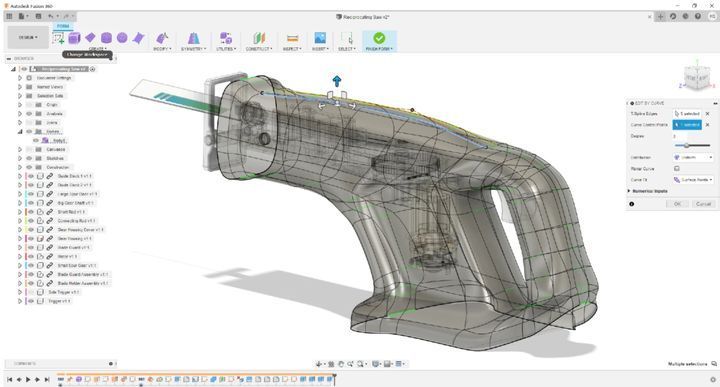
The discussion about subdivision modeling has opened up significantly since the start of this series.
The addition to Convergent modeling in Solid Edge is one example. Subd technology itself is well developed but has been applied mostly in computer graphics applications rather than in engineering. It’s a product of 1970s technology further developed in the 1990s. Subdivision modeling has traditionally brought us things like animated movies, game characters and scenes, as well as 3D CGI art. Software packages that have traditionally been used to create subd models include 3ds Max, Maya, Blender, Cinema 4D, and many others.
What’s relatively new here is the inclusion of subd-type data, tools and techniques in CAD software meant primarily for designing manufacturable parts. This article is going to look specifically at how Autodesk Fusion 360 has implemented T-Splines technology and how it plans to move forward with the technology.
For readers who aren’t up to date on the subdivision modeling tools being added to traditional mechanical CAD software, Fusion 360 is an online CAD tool (local executables, cloud data) from Autodesk. It includes all the major design techniques that you could want in a CAD product:
- Parametric history-based solids
- Freeform (T-Splines)
- Surface (history-based NURBS)
- Mesh (scan data)
- Direct (non-history based)
Each of these modeling techniques deserves an article of its own, but this time we’re focusing on T-Splines. T-Splines exists between subd techniques and NURBS data types. It enables you to switch back and forth between the two more easily.
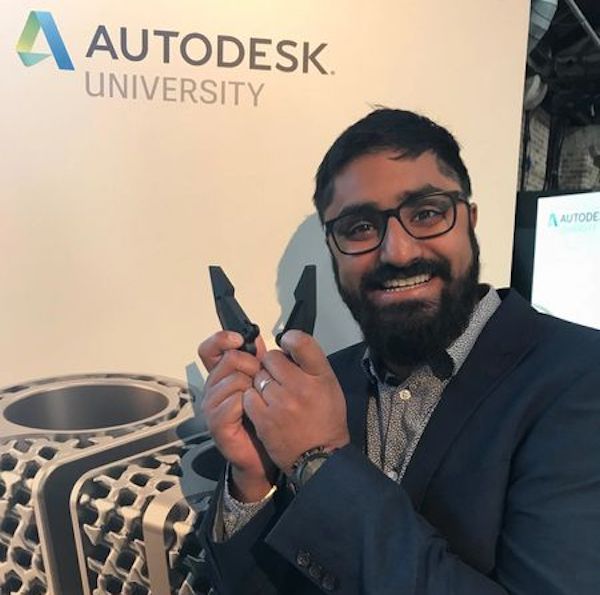
Harv Saund is a product manager on Autodesk’s Fusion 360 team. Saund answered some questions about T-Splines and subd modeling in Fusion 360:
Fusion 360 has T-Splines, which is subd type modeling. Do you still see people using history-based parametrics when tools like T-Splines are available?
Harv Saund: The short answer is yes. We believe that history-based parametrics is a super powerful way to create a design and make changes along the way. What we want to achieve with our current T-Splines/Form/subd modeling is the ability for customers to use a mixture of tools to create the final design. subd definitely has its place in traditional history-based parametric workflows, such as creating ergonomic surfaces, especially when the two can adjust and change as one. This is what we are working toward.
What are the barriers to picking up subd techniques if you’re steeped in 20 years of doing things with sketch-feature-history models?
Harv Saund: There are two big barriers to adoption of T-Splines/Form/subd:
- Dimensional control—traditionally, surfaces are controlled using dimensions and sketches, so in our Form toolset we can apply a dimension to the adjustment; however, we cannot control any of the geometry created using the traditional sketches and dimensions associated with traditional surfacing.
- Methodology—T-Splines/Form/subd is a very different way of working compared to traditional surfacing and the sketch feature history modeling. It takes a bit of getting used to and a strong understanding about the impact you’re going to make to the surface and the flow of the surface.
Having subd available, what type of work do you still recommend people do in history-based traditional surfacing?
Harv Saund: We don’t see T-Splines/Form/subd replacing traditional history-based workflows. We see both as approaches to create the final product that a customer wants. There are times when history-based makes more sense, i.e., when the model needs parametric changes made to it—dimensional variations, small curve manipulation, etc. And there are areas where T-Splines are so much faster and easier to complete the task, as with ergonomic shapes such as grips and organic shapes.
Form also has also been used a lot to convey a concept and rapidly iterate on it to get to a final idea where a more developed model can be created.
Traditional surfacing is also widely used to create the A side surface of a design using standard tools.
For Autodesk, we want to be at a point where a customer uses the tool that will get them to the most efficient design fastest and with the highest degree of accuracy. That’s why we believe that creating a bridge between T-Splines and history-based toolsets is key.
Read more at ENGINEERING.com