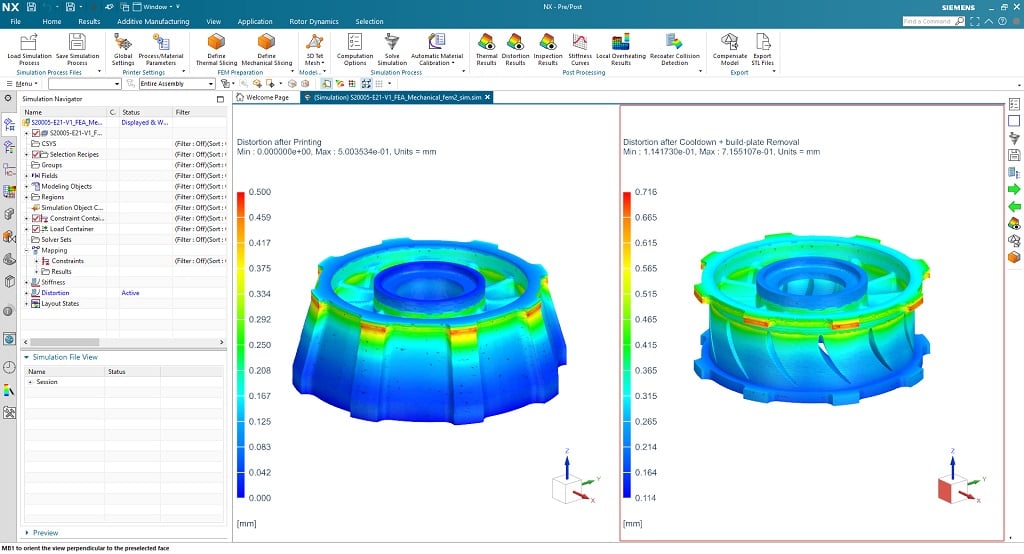
Sintavia and Siemens have announced a three-year agreement to collaborate on end-to-end additive manufacturing software targeting digital automation.
Florida-based Sintavia offers metal additive manufacturing targeting the aerospace, defense, and space sector, supported by its massive facility housing $25 million of 3D printing equipment that opened last year. The company has continued to grow its operations for end-to-end AM workflow, including the 2019 acquisition of quality control testing service QC Labs.
Siemens, of course, offers leading software solutions for industrial operations. The company has been increasing its focus on 3D printing in its software portfolio, expanding offerings both organically and via acquisition to better serve the ever-industrializing additive manufacturing sector.
This week, the two companies announced that Sintavia will provide Siemens Digital Industries Software “with software testing and technical feedback in exchange for access to pre-released additive manufacturing software.” The companies are set to develop their new solution “as a part of Siemens’ Xcelerator portfolio,” as Sintavia becomes a “preferred AM partner of Siemens.”
“The collaboration with Sintavia is vital to our efforts to develop an automated end-to-end solution that spans the entire AM lifecycle—from designing an optimized part, preparing it 3D printing and simulating its build, to planning serial production, executing on the shop floor, and delivering a qualified part,” said Aaron Frankel, Vice President of the AM Program for Siemens Digital Industries Software.
“With their depth of experience and track record in the market, Sintavia can provide the kind of technical feedback we need to build AM know-how into our digital twin and make the system the expert as opposed to the user. This is a critical step to making additive more widely embraced for volume production. Unlike traditional manufacturing, additive is a process where we don’t have decades of established knowledge that is readily communicated, whether in software or through technical education. Companies can’t afford to make everyone in the AM process an expert; they need the software to automate some tasks, work in the background, and make additive more of a push-button process.”
And so Siemens will leverage what Sintavia CEO Brian Neff refers to as “tribal knowledge” that the service company has developed in the delivering of “quality 3D printed metal parts”:
“But we recognize that we can’t just rely on individual expertise to meet the accelerating demand in aerospace for additive manufacturing. We need software to codify the processes we undertake, and not just connect them in a digital thread, but automate them, take our know-how and have it drive activities in the background, so we can achieve optimal efficiency.”
Sintavia and Siemens are set on a three-year collaboration course for joint sales and marketing, including events at Sintavia’s 55,000-square-foot metal AM facility. In terms of the marketing aspect, we can also expect to hear more focus on sustainability — not just a buzz word in advanced manufacturing, but key to Sintavia’s own operations. The company was among the co-founders of the Additive Manufacturer Green Trade Association (AMGTA), which emerged in November 2019; Siemens joined the nonprofit this year.
“Siemens’ additive manufacturing software contributes to greener additive manufacturing production not just by streamlining designs and reducing material usage, but also by leveraging simulation to help enable first-time-right 3D printing and optimize AM factory efficiency to eliminate waste,” notes Frankel.
Via Sintavia