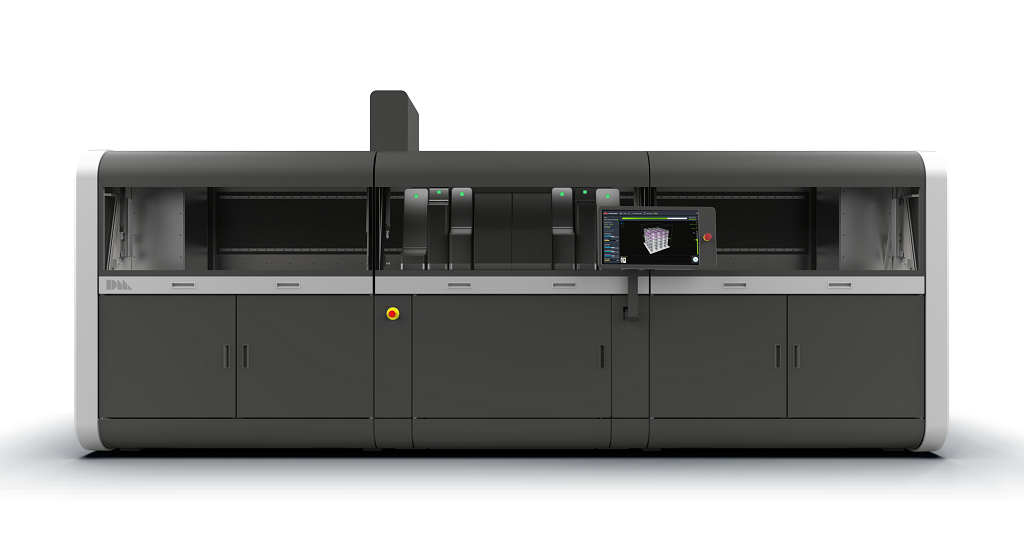
As additive manufacturing continues to work toward high-volume applications, major institutions have taken notice — not just in industry, but in government departments.
This week, Desktop Metal announced its awarding of a three-year Department of Defense grant. The DoD is setting $2.45 million toward funding the development of a high-volume additive manufacturing process focusing on mass production of Cobalt-free hardmetal parts.
Desktop Metal seems a natural fit for such a development project, as production is so integrated into their operations it’s the name of one of their key metal 3D printing systems. Desktop Metal’s Production System has captured our attention for years, and the company continues to focus on making it an ever-more-capable additive manufacturing system.
Part of those capabilities include working closely with traditional metal manufacturing technologies, like metal injection molding (MIM). To that end, Desktop Metal announced a MIM-focused partnership last year; more on that partnership here.
This week’s announcement may have wide-reaching implications that touch several sectors, from cutting tools, oil & gas, off-road transportation, and construction to aerospace and defence and consumer products. The release explains:
“Desktop Metal…announced today it has been awarded Phase I of a three year $2.45 million dollar project from Department of Defense (DoD) to develop a sophisticated Additive Manufacturing (AM) process capable of mass producing Cobalt-free hardmetals, developed by the U.S. Army. The company’s Production System with Single Pass Jetting (SPJ), a proprietary AM technology developed by Desktop Metal, will mass manufacture complex shaped Co-free hardmetal parts without tooling and is expected to lead to the development of a dual use technology with numerous applications in DoD as well as in the civilian sector.”
And:
“Successful investigations by the U.S. Army in developing a novel iron-based nano material as the matrix in WC-based hardmetals, replacing Cobalt, has resulted in the development of a patented, novel Co-free WC-(Fe-Ni-Zr)-based hardmetals. In tandem with the creation of this promising new material for commercial and DoD applications, the ARL has been in search of a cost-effective, high volume process capable of manufacturing the new Co-free hardmetals into complex, net or near-net shaped parts without the use of any tooling.”
They add that goals and requirements include:
- Development of a feedstock and binder system for novel cobalt-free hardmetal
- Using the Desktop Metal SPJ process to print a sufficient quantity of components of at least 200,000 parts in one day from a single machine
- Delivery of a cost analysis for scaling up its advanced SPJ binder jet manufacturing technique to successfully manufacture at least 500,000 prototype pieces
In short, this is a technologically advanced, results-oriented project with high expectations for performance.
The intent is to bring the speed of Desktop Metal’s production SPJ 3D printing technology into cost-effective, high-volume Co-free hardmetals manufacturing that can produce “complex, net or near-net shaped parts without the use of any tooling.”
So, no pressure.
It’s just a three-year project that sounds like a proof point for almost every major selling point of additive manufacturing overall. Complexity, tool-less production, speed, accuracy, application-specific — and, naturally, environmentally friendly with better properties than traditional solutions.
“The novel Co-free hardmetal grade is expected to yield a high strength, high toughness, high hardness, and high wear resistance material,” said Dr. Nicholas Ku, Materials Engineer, CCDC Army Research Laboratory. “We believe combining this novel material with Desktop Metal’s Single Pass Jetting technology will have major applications not only in the defense sector but also in the commercial sector. Further, we believe this combined method will dramatically improve sustainability, reduce the use of a conflict mineral and provide an environmentally-friendly process to mass produce parts with superior properties.”
This announcement covers Phase I of the three-year project, which was issued by the U.S. Army Contracting Command – Aberdeen, Research Triangle Park, on behalf of U.S. Army Research Laboratory to the National Center for Manufacturing Sciences (NCMS) Advanced Manufacturing, Materials & Processes (AMMP) Consortium.
Via Desktop Metal