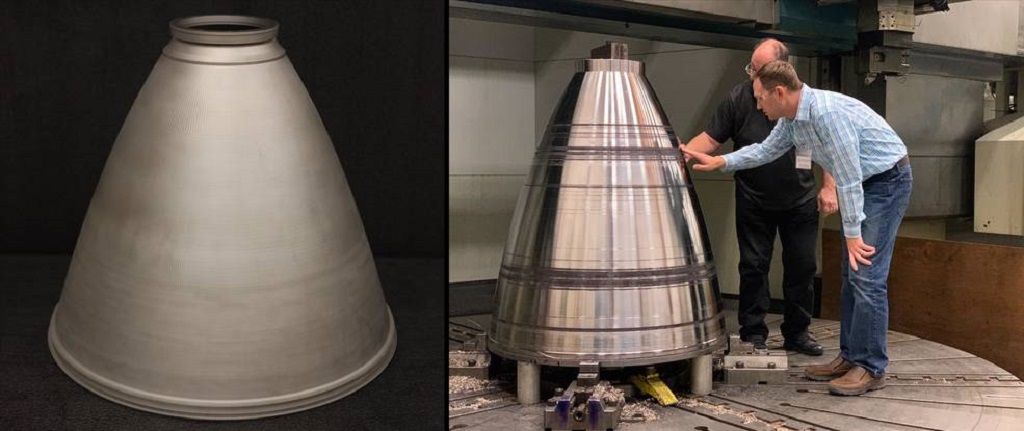
As NASA continues to ramp up its work to explore space, 3D printing is taking its place among the stars — or at least the rockets that will get us there.
RAMPT
NASA’s Rapid Analysis and Manufacturing Propulsion Technology (RAMPT) is a project designed to improve manufacturing methods and consequentially the performance and production costs of rocket thrust chamber assemblies. These assemblies are typically the most expensive and time-consuming parts of rocket engines to develop, due to not only their complexity, but also their sheer weight (every ounce costs money when it’s being put into space). Being composed of a combustion chamber, nozzle, and joints, they power rocket engines by mixing fuel and an oxidizer in the combustion chamber to produce hot exhaust, which is then passed through a nozzle to accelerate the flow and produce thrust.
Novel manufacturing methods could cut both costs and production time for NASA missions, greatly increasing their efficiency. To cut down on both time and cost, RAMPT replaces some traditional metal pieces on the thrust chamber with composite material, uses advanced 3D printing techniques to print the combustion chamber and nozzle, and uses innovative methods to fuse these two together instead of using joints that can be points of weakness.
Imagine being able to produce the most difficult and expensive rocket engines in a fraction of the time required, and for a lower price tag. According to Drew Hope, manager of NASA’s Game Changing Development program (which funds the RAMPT project), NASA’s new technology advancement does just that. He even goes on to say that:
“[This technology advancement] will allow companies within and outside of the aerospace industry to do the same and apply this manufacturing technology to the medical, transportation, and infrastructure industries.”
The Development
The new development to the RAMPT project looks at using blown powder directed energy deposition to 3D print metal rocket parts using metal powder and lasers. Use of DED technology could significantly reduce costs and lead times for producing large, complex engine components like nozzles and combustion chambers. Although previous developments in additive manufacturing featured similar techniques, this emerging technology promises large-scale applications that haven’t yet been achieved.
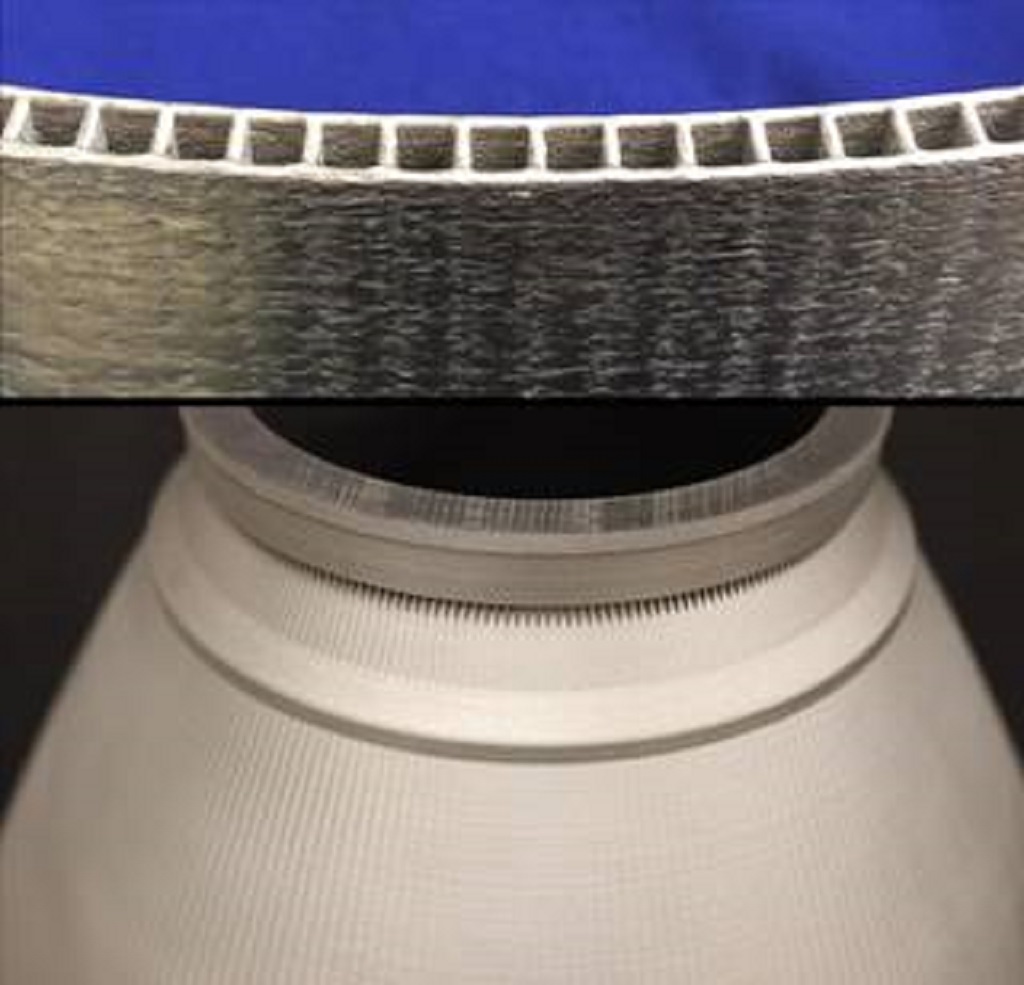
[Source: NASA]
Their Results
The RAMPT team used DED to 3D print one of NASA’s largest (printed) nozzles yet, scaling 40 inches in diameter and 38 inches in height with fully integrated cooling channels. The nozzle took a mere 30 days to fabricate in comparison to one year using traditional welding methods — putting the project a full year ahead of schedule due to rapid tech advancements.
The success of this project has caught the eye of NASA’s Space Launch System (SLS) rocket team who are researching the application of this fabrication technology — adding to the 3D printing processes used in the SLS — with the aim of certifying it for spaceflight. Alongside RAMPT, the team hopes to build and evaluate a channel-cooled nozzle that’s even larger — 5 feet in diameter and about 7 feet in height.
Via rigorous hot fire tests, engineers plan to expose a subscale version of the produced nozzle to the 6,000 degree combustion temperatures and sustained pressures it would face during launch to investigate the durability of this new technology.
As part of the Artemis program, NASA hopes to utilize this technique to send astronauts to the moon, where they will prepare for human exploration of Mars.
Partnerships And The Private Sector
By way of an agreement between NASA and Auburn University in Alabama, RAMPT joins forces with specialty manufacturing companies to ensure that the technologies developed by this team are available to the private sector.
These partnerships are valuable to NASA in that partners share some of the development costs.
Via NASA