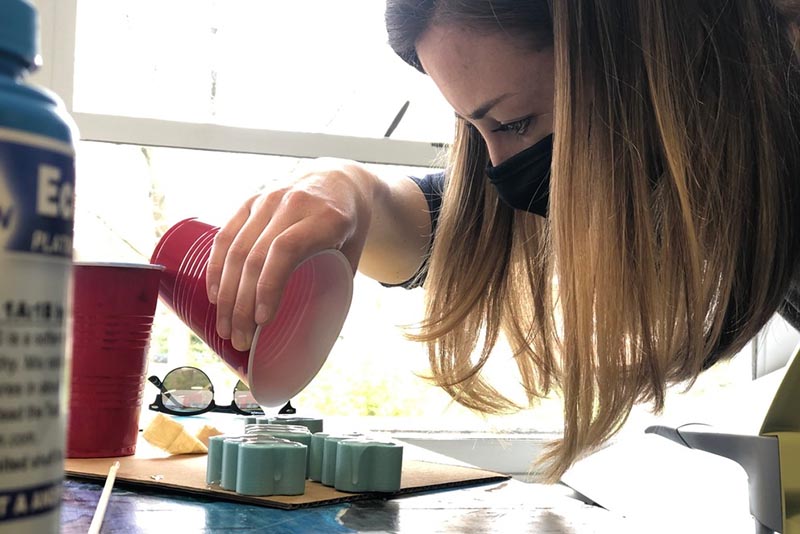
Another application for 3D printing in pandemic response has emerged with single-use stethoscopes.
This technology has been serving both stop-gap and longer-term supply chain needs for the last few months as the global spread of novel coronavirus has hit hard. Personal protective equipment (PPE) and nasopharyngeal (NP) testing swabs remain the heavy hitters in terms of 3D printed pandemic response, while ventilator splitters and other components continue to serve emergency-use needs, but of course demand for quickly-produced medical devices remains high beyond these well-known uses.
MASC Consortium
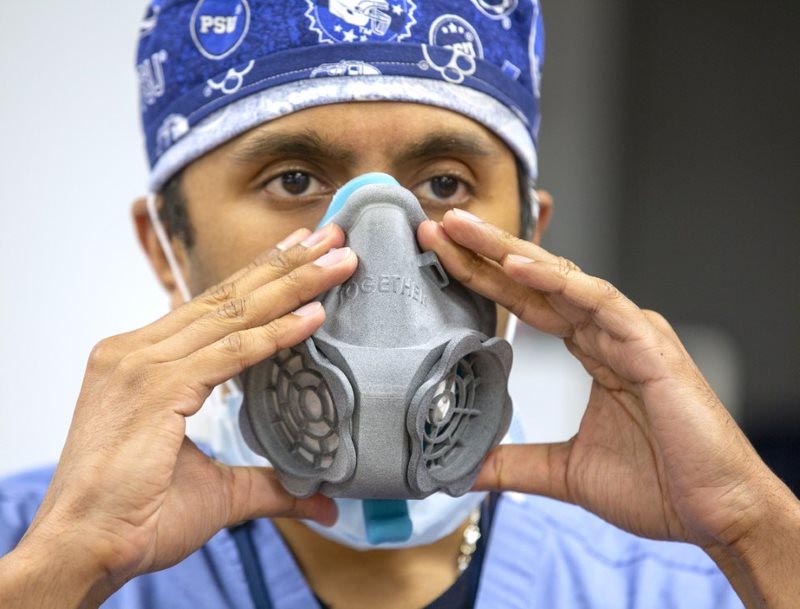
In March, Penn State launched its 350-plus-researcher-strong Manufacturing and Sterilization for COVID-19 (MASC) Initiative, bringing together expertise and resources with the tagline:
“Design, development, prototyping, testing, and validation to help win the fight”
The effort began, perhaps unsurprisingly by now, with 3D printing.
“It was going to be tough to run a hands-on lab when students weren’t allowed in the labs, so I started looking for ideas about 3D printing COVID-19 PPEs, which students can help design from their homes. My students jumped at the opportunity to focus their project on this pressing need,” said Tim Simpson, Paul Morrow Professor of Engineering Design and Manufacturing in the College of Engineering, who also co-directs the Penn State Center for Innovative Materials Processing through Direct Digital Deposition (CIMP-3D).
That initial plan, sprung from the need to move from physical to remote an undergraduate 3D printing course, quickly picked up steam — and support from other sectors of the Penn State community. By late March, MASC work focused on three areas, which Penn State described (emphasis theirs) as:
- Manufacturing activities are focused on developing fast and scalable approaches for making face shields, N95 masks, ventilator parts, swabs, gowns and other items as needs arise.
- Sterilization activities are aimed at evaluating techniques, such as ultraviolet radiation, vaporized hydrogen peroxide and plasma methods, for rapid and large-scale sterilization of PPEs.
- Legal and regulatory efforts involve tracking how the team’s solutions conform to regulations from the FDA, which are changing frequently as the COVID-19 pandemic unfolds.
By late April, the MASC team had developed a number of projects to address COVID-19-driven needs. A 3D printed filtration mask proved a notable victory for the consortium, and they also observed other milestones including:
- Safely recycling N95 masks
- Creation of intubation booth
- 3D printing test swabs
- Delivery and design of powered air purifying respirators (PAPR)
Single-Patient Stethoscopes
Recently, though, another sort of project has emerged based on medical provider need.
Work with the Hershey Medical Center introduced the MASC team to a request for stethoscopes that could be disposable, used for only a single patient, helping to avoid any potential for cross-contamination. Shortly after that need was communicated, design ideas were underway. A first design, Penn State College of Engineering News reports, consisted of “silicone food-grade tubing, typically used to make beer; hand-made silicone earpieces made via a 3D printed mold; automotive brake line, and a 3D-printed cover and diaphragm.”
Following feedback from an initial 100 such stethoscopes, the design continued to go through successive iterations over about two weeks “to improve acoustic quality while reducing the number of parts and assembly time,” as well as enhancing time and costs to lead toward larger-scale production. A few dozen prototypes later, and the MASC team is “now moving forward toward the mass production of a final stethoscope” as they work “with industry partners to finalize a manufacturable design that can be mass produced in a GMP facility to address the urgent need.”
“As someone who studies engineering design, I’m fascinated with the pace of the design processes needed to produce critical medical products for this crisis. The near-constant communication between MASC and the medical center is a real catalyst for engineering design innovation,” said Jessica Menold, assistant professor of engineering design and mechanical engineering and MASC member.
The Pace Of Design
Menold’s point regarding the pace of design innovation brings several factors front-of-mind as to how 3D printing and other advanced manufacturing technologies have been key to pandemic response.
Communication is, of course, critical, as the MASC members worked closely with medical professionals to develop, iterate, and effectively perfect a design for single-patient stethoscopes. Understanding the needs of the medical users is key to creating a viable product that both meets the needs of end users and can be created well.
The consortium aspect of what MASC does is also vital to its ongoing success stories. In this one project, the design came to being not from one mind but from many; named among project contributors are:
- Menold’s Technology and Human Research in Engineering Design lab
- Graduate students including Tobias Mahan, Daniel Spillaine, Lauren Ryan, Glen Williams and Pratima Saravanan
- Sarah Ritter, associate teaching professor of engineering design, Andrea Arguelles, assistant professor of engineering science and mechanics, Caitlin Grady, assistant professor of civil engineering, and Meg Handley, associate director of engineering leadership outreach
- Bill Genet and Robert McAllister, shop supervisors at the Learning Factory
- Dr. Anthony Tsai, a physician at the Milton S. Hershey Medical Center
- Barry Fell, a consultant for the Department of Surgery at the Hershey Medical Center and a member of the MASC team
From mini-hackathon participants to sub-group iterating to support and validating, every person here contributed in some way to the development of the specific tool that the medical center had specified.
Working together, communicating regularly, and with the help of fast manufacturing technology like 3D printing, these single-user stethoscopes are ever closer to patient use where it’s needed most.
Via Penn State News 1, Penn State News 2, Penn State News 3, and MASC