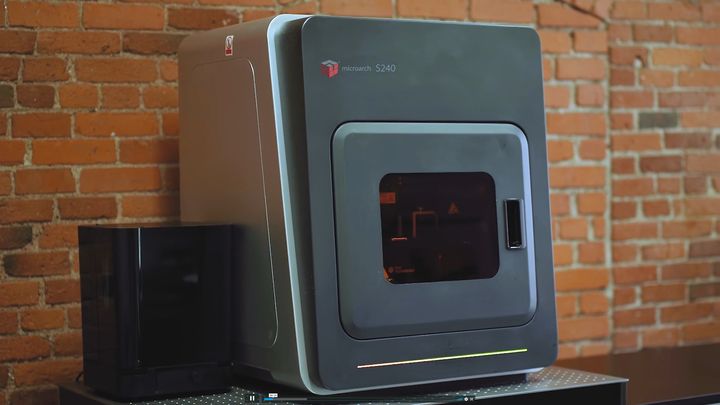
BMF released details today about an industrial 3D printer targeting the micro parts market.
Projection Micro-Stereolithography
The Boston-based company has been on our pages earlier this year when they revealed their technology. The resin-based 3D printing process they use is called āPμSLā, for āProjection Micro-Stereolithographyā. PμSL is able to achieve an astonishing resolution of 2μ, or 0.002mm. This is accomplished due to some technological magic that allows them to project UV light in extreme resolution.

Evidently theyāve created several different resins that can be used in the PμSL process, including:
- GR — Hard
- HEK — Strong & Tough
- HTL — High Temp, Low Viscosity
- UTL — Tough
- BIO — Biocompatible
These offer a variety of engineering properties, allowing BMF clients to select the right material for the job. Presumably they are developing additional materials to add to their portfolio in the future.
microArch S240

Now the company has released a new device, the microArch S240. This is designed for short-run industrial production.
What does āproductionā mean? Generally itās the ability to run continuously to produce volumes of objects over a longer period. We tried defining āproduction 3D printersā in a previous story, and I think the microArch S240 hits a lot of the characteristics necessary for that classification.
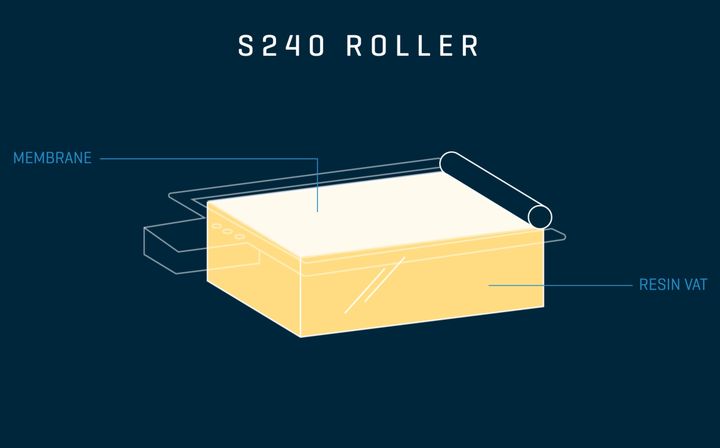
BMF says the new device includes these features to allow for production use:
- Larger build volume of 100 x 100 x 75 mm (their previous largest machine, the P150, had a build volume of 48 x 27 x 50 mm)
- Print speed increase of up to 10X, while maintaining high resolutions, apparently accomplished by a new resin spreading mechanism
- Ability to handle higher-density materials, meaning it should be possible to 3D print stronger parts
- Ability to 3D print in composite materials, for far stronger parts
- Ability to 3D print ceramic materials
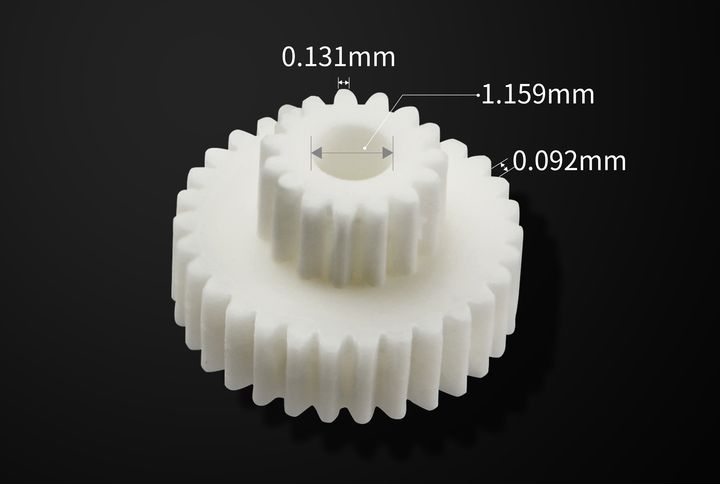
The first two attributes, when combined, offer a tantalizing proposition: print faster in a larger volume. This could allow for either production of larger single parts or larger quantities of smaller parts in a single build.
microS240 Resolution
This machine produces parts with incredible resolution. These images show some of the possibilities of the microS240 3D printer. Note in the images above, each 3D printed part is sitting on a US penny!
This machine should be of considerable interest to companies currently producing detailed small parts. Typically these are produced using molding techniques, and thus are somewhat constrained in terms of possible geometries. The ability to 3D print such small, detailed parts introduces some new possibilities.
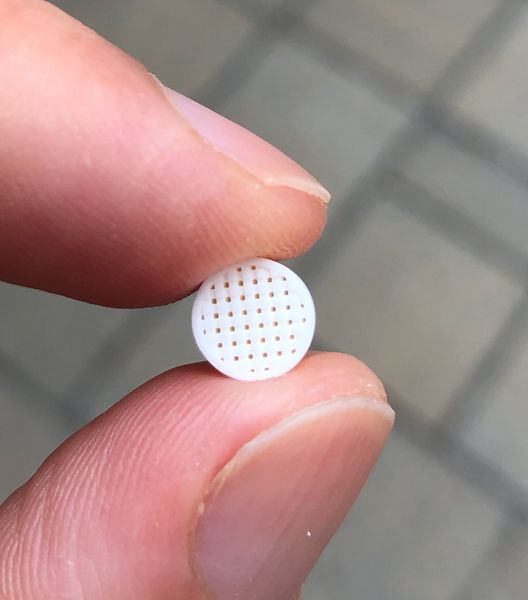
It would be possible, then, to 3D print small volumes of unique or customized parts. This would obviously require the creation of suitable unique 3D models for printing, and that could be the next challenge for BMF.
Itās likely this particular market is set in their ways as has every other 3D print market. In other markets some 3D printer manufacturers have gone to great lengths to āeducateā their markets on the possibilities enabled by 3D printing. This can be a very challenging step, as it requires users to change how they think about designing parts.
It will be interesting to see how BMF approaches this opportunity.
Via BMF