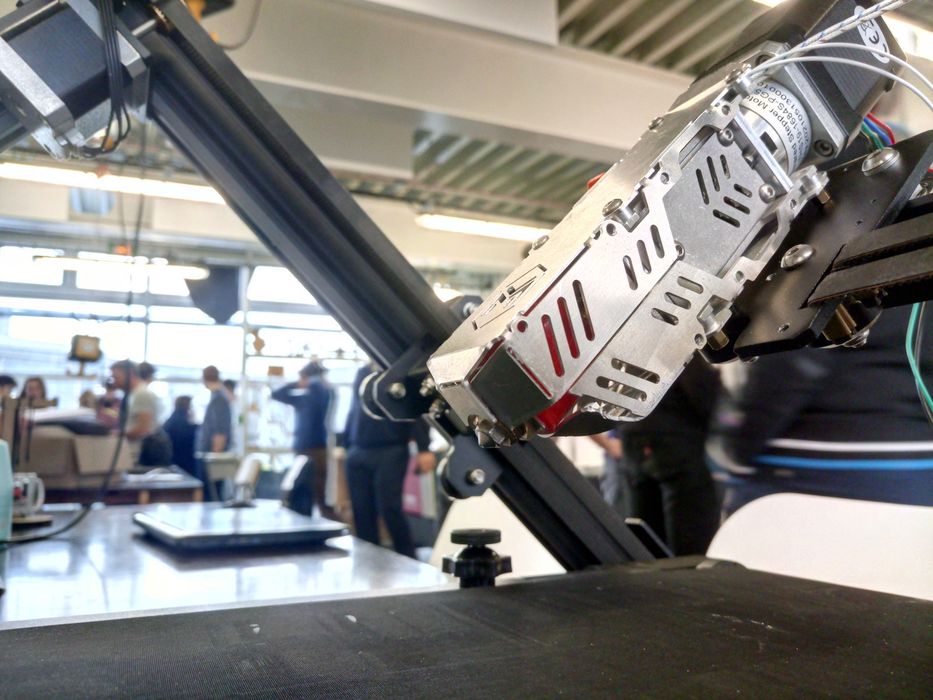
A most interesting 3D printer experiment could show how desktop 3D printers may work in the future.
Emmanuel Gilloz is a maker who is the manager of FabLab Caen in France. Gilloz undertook the fascinating job of adapting a belt 3D printer to use a pellet extruder.
The belt 3D printer in question is the Creality CR-30, which is perhaps the most popular belt device right now. Also known as the ā3DPrintMillā, the device was launched by Kickstarter in 2020 and promoted by super maker Naomi Wu, who exclusively spoke to us about the CR-30. (Note: Wu is no longer working with Creality.)
Creality sold around 2000 CR-30ās through the Kickstarter campaign, and certainly added many more afterwards through direct sales. Itās still available today, and is the most frequently seen belt 3D printer.
Belt 3D printers have a significant advantage over ānormalā 3D printers in that the print surface moves and can automatically eject prints when complete. This means that the belt 3D printer effectively becomes a mini factory that can continuously produce objects without attention ā aside from reloading the filament spool once in a while. They can also produce long objects that exceed the dimensions of the printer itself.
One problem with mass producing objects with belt 3D printers is the unit price of the parts. Even though you may have purchased the printer, you still must pay for the cost of materials. Filament can be expensive when mass producing parts. For example, if you spend US$20 on a spool, and you can make 20 parts with it, then each part costs at least US$1.00. The cost of an injection molded equivalent part would be only pennies.
Why so much cheaper? Itās because of the nature of the material. 3D printer filament requires precise manufacturing to ensure the filament is of uniform diameter, along with spooling, cooling and packaging.
Filament is made from resin pellets that are normally sold at rock bottom commodity prices. So why not 3D print from pellets instead and skip the whole filament sequence?
Thatās easier said than done, as it requires an entirely different kind of extruder. Instead of pulling a filament, it must melt, and then push thermoplastic. Normally this is done with a screw mechanism that pulls pellets down into a hot end.
If one could use a pellet extruder on a belt 3D printer you would have a highly economical way to produce quantities of parts. Typically the price of pellets is at least 10X less than the same weight of filament from the same material.
The resulting parts would be lower in cost to produce, and could indeed financially enable many more use cases.
Unfortunately the CR-30 comes with a filament extruder.
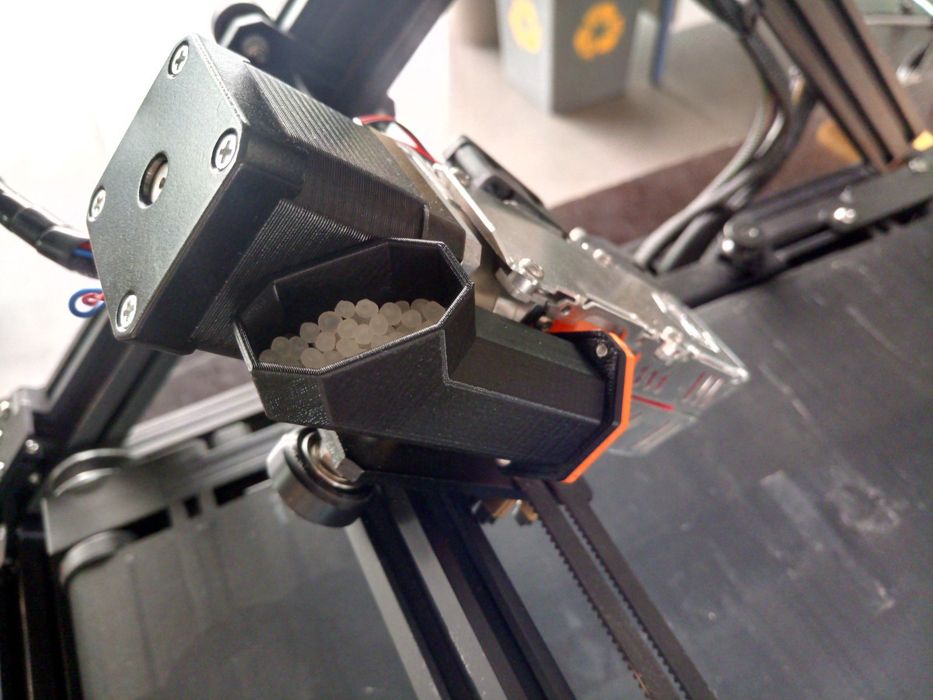
That was the challenge facing Gilloz, who decided to take out that filament extruder and replace it with a pellet extruder. This is where the problems started, as there are indeed pellet extruders on the market. Unfortunately they are intended to be used with large-format 3D printers and they can cost quite a bit of money. More than the cost of the CR-30, in many cases.
Eventually, Gilloz landed on the Mahor Pellet Extruder V4, which is a smaller pellet extruder that is available at a much lower price than the other pellet extruders.
Gilloz wrote a long post explaining his journey through the installation and operation of the pellet extruder on a CR-30.
It turns out the swap was far more complex than originally thought, but he did manage to get it working successfully.
Issues encountered included:
- Physically modifying the CR-30 to enable mounting of the pellet extruder
- Recompiling Marlin firmware to interface with the new hardware
- Configuring the flow rate for the extruder
- Determining basic 3D print parameters that worked
- Ensuring motion that ājigglesā the pellet hopper to ensure plastic bits are tightly packed
- Designing effective air flow ducting to cool freshly printed material
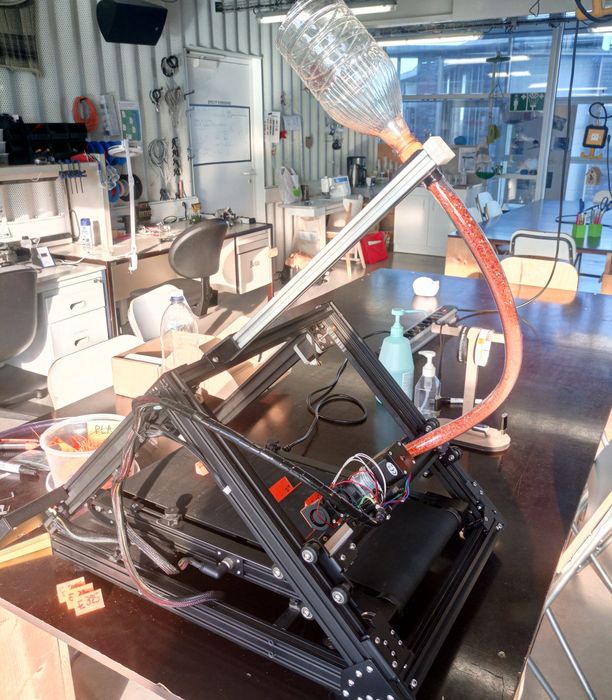
One of the most interesting problems was that of humidity. Gilloz found that if the humidity was higher than 40%, then printing would not work properly. Itās likely that the added surface area of pellets tended to absorb more humidity than normal filament would absorb.
Another issue was feeding the pellets. Some commercial pellet systems Iāve seen include sophisticated hopper systems involving feeder screws. Here Gilloz simply used a long plastic tube and let gravity do the work.

Gilloz spent much effort working on print parameters. The main issue seems to be that the momentum of the flow is quite different from filament, as the thermoplastic in the pellet extruder responds differently to force.
Eventually it appears that Gilloz figured out the correct combination of parameters and was able to 3D print objects successfully.
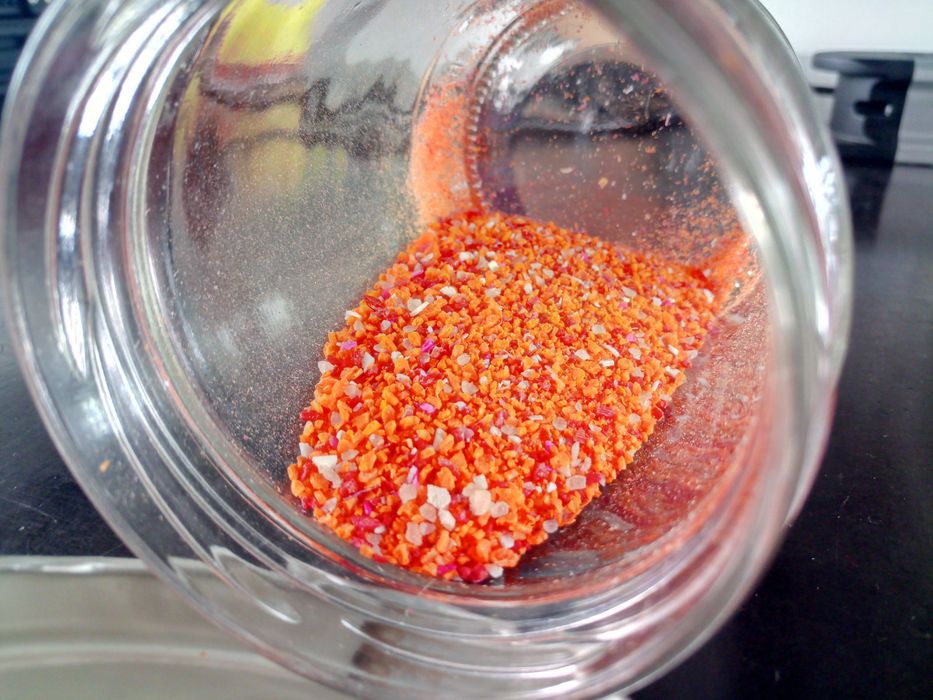
Gilloz also intended to use the pellet capability as a way to reuse thermoplastic: chop it up and use it instead of pellets. However, this turned out to be quite challenging.
The Mahor extruder was unable to handle pellets exceeding 3mm in size, and so Gilloz was forced to devise a system that could grind up plastic into appropriately sized pieces.
This is certainly not a project many would wish to undertake themselves, but it definitely proves the belt-pellet combination can be made to work.
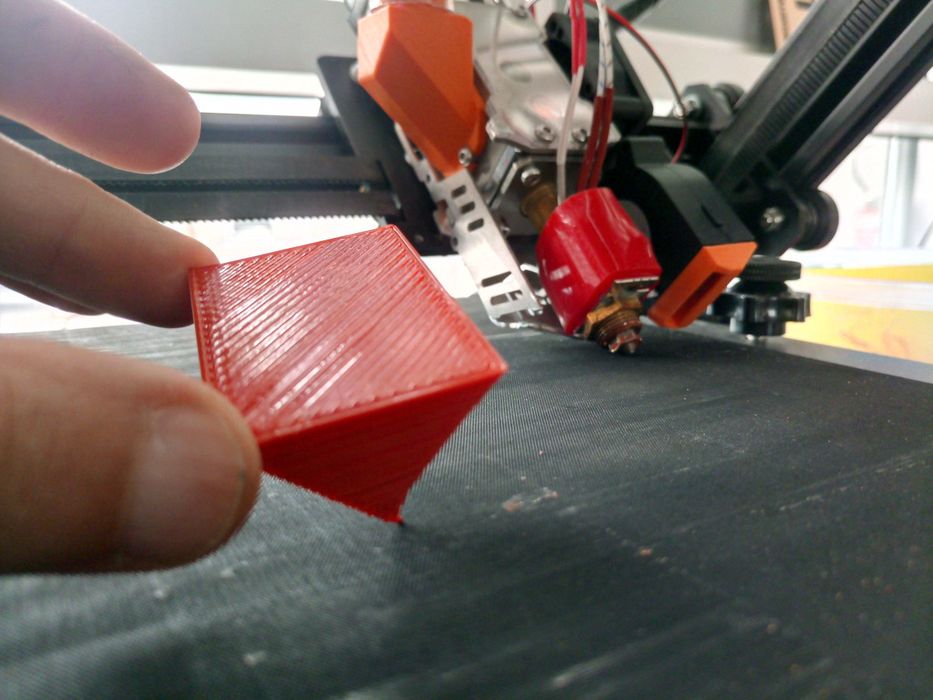
With the number of makers using the CR-30 as a production device for their low-volume needs, the ability to use pellets would be immediately useful. Iām wondering if Creality (or others) would consider building a more easily-installed pellet extruder upgrade, or even market a CR-30 pellet version in the future. Iām certain it would attract considerable attention.
Meanwhile, If you want to upgrade your own CR-30 in the same way as Gilloz, hit the link below for all the details.