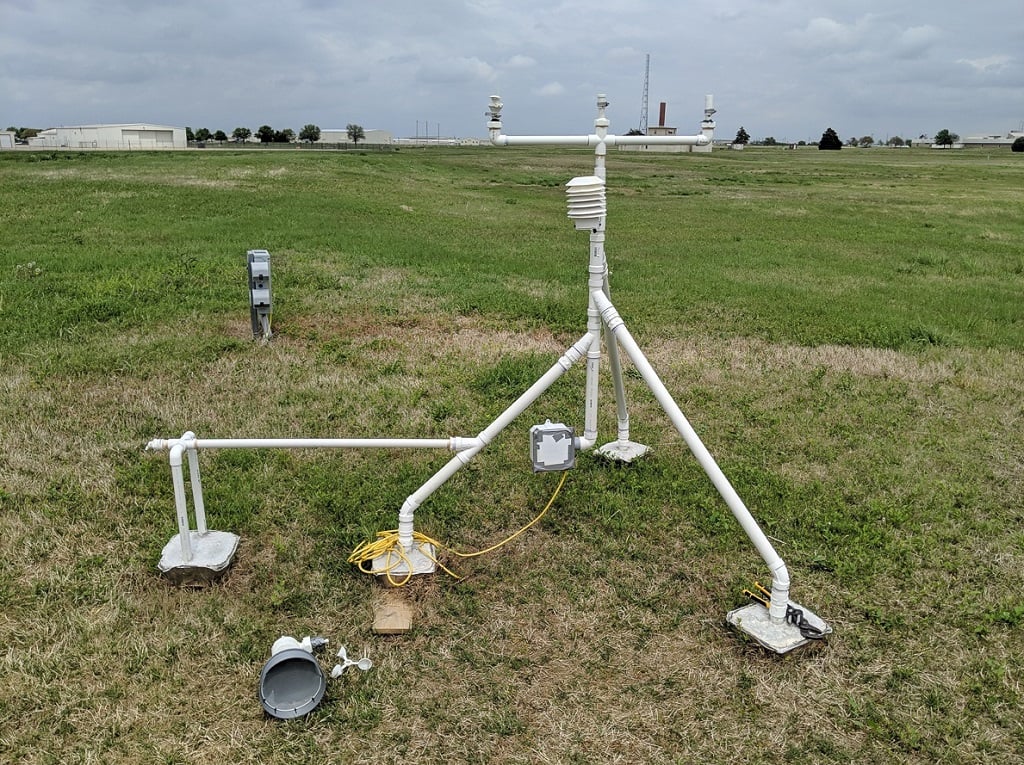
Sometimes “field testing” is very literal, as Argonne National Laboratory’s recent work with a 3D printed weather station highlights.
Weather stations can be complicated, expensive endeavors. Capturing accurate weather data to understand and study climate with an array of instruments and sensors is an important undertaking. And, as with so many important undertakings, that usually means a several-thousand-dollar investment.
But — enter 3D printing — what if costs could be lowered for shorter-term study?
A 3D Printed Weather Station
University of Oklahoma (UO) undergrad students led a 3D printed weather station project with Adam Theisen, who was initially with the UO before taking on a position as an atmospheric and Earth scientist at Argonne. The charmingly named 3D-PAWS (3D-Printed Automatic Weather Station) project set out to ascertain whether a lower-cost could measure weather well enough for use.
From mid-August 2018 to mid-April 2019, an intriguing installation in Oklahoma stook out in a field. The 3D-PAWS initiative was developed at the University Corporation for Atmospheric Research, which came up with guidance and open source plans for more than 100 parts to be 3D printed for a weather station.
The UO team 3D printed these parts using ASA (acrylonitrile styrene acrylate) material. ASA was chosen for its higher ultraviolet radiation, temperature, and impact resistance than PLA. The 100+ parts were designed to be made inexpensively and quickly, so also used a grid infill to reduce printing time, though this ultimately made for somewhat weaker parts.
Over the course of eight months, the 3D printed installation was subjected to “strong rainstorms, snow and temperatures ranging from 14 to 104°F (-10 to 40°C).” Argonne reports that “[w]ith the exception of a couple of instruments, the plastic material held up in the Oklahoma weather.”
About five months in, some of the 3D printed parts degraded and broke, and the relative humidity sensor corroded and failed. But that’s to be expected when working with a lower-cost, shorter-term installation. What was more hoped than expected, though, was the results during that time: the data collected was good. Measurements were measuring up to those of a commercial-grade, standard weather system.
“I didn’t expect that this station would perform nearly as well as it did. Even though components started to degrade, the results show that these kinds of weather stations could be viable for shorter campaigns,” said Theisen.
“Even though components started to degrade, the results show that these kinds of weather stations could be viable for shorter campaigns.”
Lowering Scientific Barriers
The 3D printed weather station is impressive — and carries with it some larger implications.
Part of the abstract from the paper published about this project notes:
“Temperature, relative humidity, atmospheric pressure, wind speed and direction, solar radiation, and precipitation measurements were collected over an 8-month field deployment in Norman, Oklahoma. Measurements were comparable to the commercial sensors except for wind direction, which proved to be problematic. Longevity and durability of the system varied, as some sensors and 3D-printed components failed during the deployment. Overall, results show that these low-cost sensors are comparable to the more expensive commercial counterparts and could serve as viable alternatives for researchers and educators with limited resources for short-term deployments. Long-term deployments are feasible with proper maintenance and regular replacement of sensors and 3D-printed components.”
The basic implications — lower cost, acceptable short-term performance — are in line with what we’ve come to expect from 3D printing.
But others go beyond this into some of the known, but perhaps less frequently discussed, benefits of the technology. Namely, adoption can be widespread, including to more remote areas, and less-experienced scientists (i.e., students) are able to gain access to scientific tools.
Wherever a 3D printer can be installed, such devices can be made. Weather stations can be installed in a field in Oklahoma, as this case shows — or really anywhere.
“The ability to print specialized components could make weather stations more feasible in remote areas because replacement parts could be fabricated right away when needed. And even if a cheaper sensor breaks after a few months, the math still works out for a low budget,” Argonne explains.
Further, as Theisen points out:
“The students learned skill sets they would not have picked up in the classroom. They developed the proposal, designed the frame, and did most of the printing and wiring. …If you’re talking about replacing two or three of these inexpensive sensors versus maintaining and calibrating a $1,000 sensor every year, it’s a strong cost-benefit to consider.”
The full paper is available here for a closer look into how this 3D printed weather station performed.
Via Argonne National Laboratory