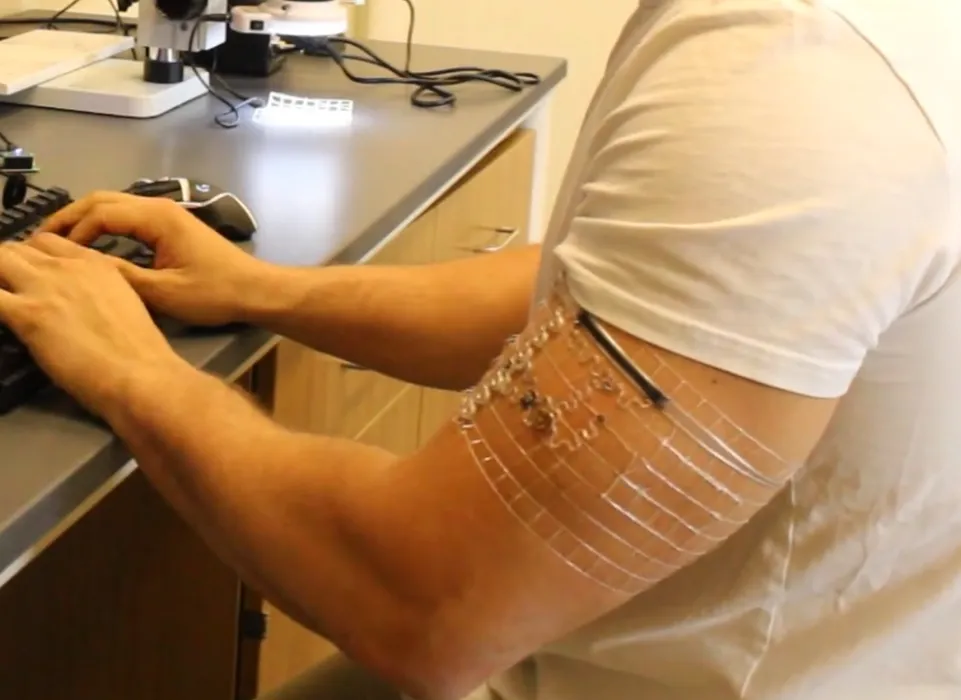
Researchers have found a way to 3D print soft, bio-electronic sensors that directly integrate with the body.
Itās often of interest to monitor bodily functions and movement, and typically this is done with sensors of various types. This is essentially digitizing bodily operations, and that data can be analyzed in a number of ways for various benefits.
However, the conventional sensors tend to be intrusive and difficult for the wearer. Now there has been a new class of devices developed by researchers at the University of Arizona, described in their paper, āBiosymbiotic, personalized, and digitally manufactured wireless devices for indefinite collection of high-fidelity biosignalsā.
Existing sensors typically involve power sources (usually batteries) nearby that incur weight, or adhesives to the skin that are irritating or constrain movement.
They explain:
āThis work introduces a previously unexplored class of devices that overcomes the limitations using digital manufacturing to tailor geometry, mechanics, electromagnetics, electronics, and fluidics to create unique personalized devices optimized to the wearer. These elastomeric, three-dimensional printed, and laser-structured constructs, called biosymbiotic devices, enable adhesive-free interfaces and the inclusion of high-performance, far-field energy harvesting to facilitate continuous wireless and battery-free operation of multimodal and multidevice, high-fidelity biosensing in an at-home setting without user interaction.ā
Their process is to perfectly fit a sensor to an individual by using 3D scanning and subsequently 3D printing a geometry to fit.
How did they overcome the weighty power problem? Then explain:
āThe devices are powered wirelessly over a long range to facilitate continuous acquisition of clinical grade biosignals.ā
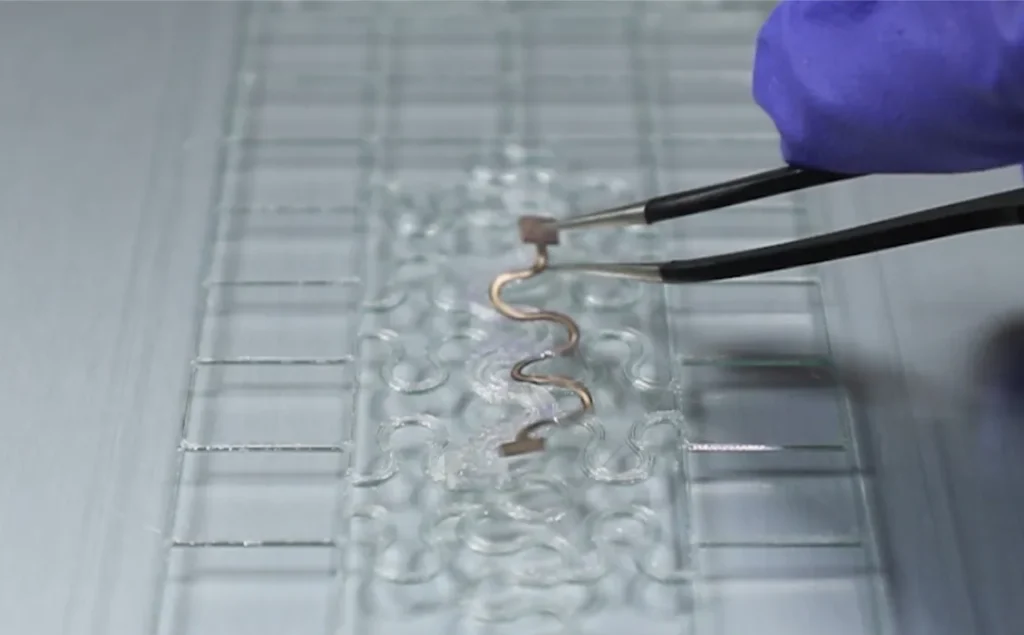
Electronic components are embedded within the structure, which happens to be flexible 3D printed TPU material (Shore 85-A Ninjaflex). Hereās how they build a sensor:
āThe base layer (450 μm) of TPU is printed onto a glass surface, and device geometries incorporate a channel with a 200 μm-thick wall at a height of 300 μm above the base layer. This creates a 3D printed channel that serves as a receptacle that guides placement of the flexible printed circuits and electronics. The circuits are placed into the mesh by hand, using 3D structured channels to guide placement. The resulting structure is subsequently encapsulated by continuation of the 3D printing process, which deposits a layer of TPU over the channel with embedded circuity, forming a seal around the electronics.ā
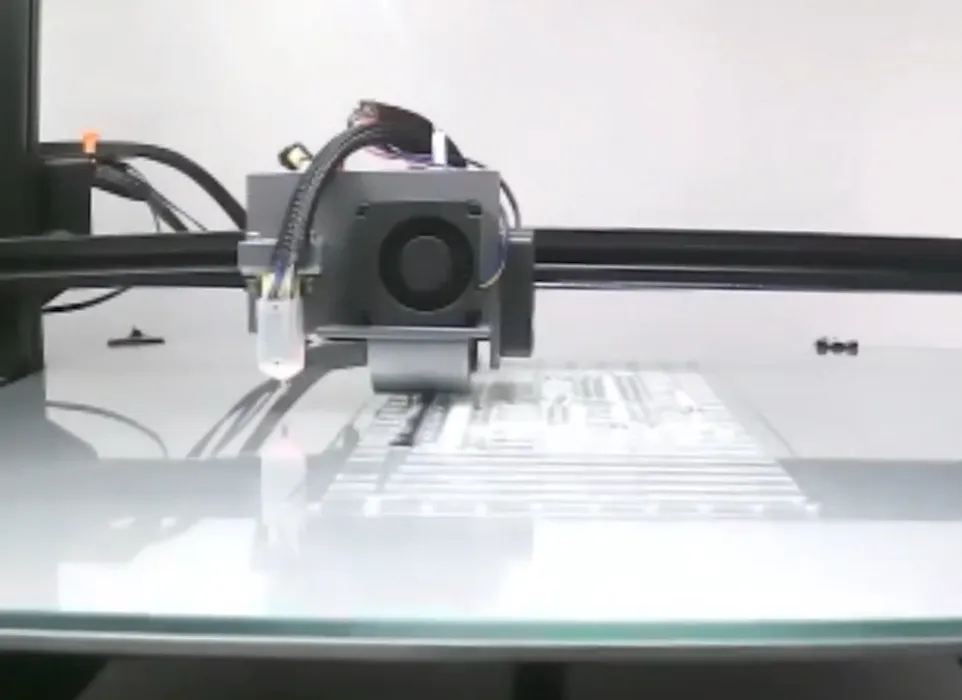
The project used different forms of 3D scanning data to develop the necessary geometry for individual applications, including MRI, CT scans or conventional 3D scanning techniques. This data was used to adjust a base 3D model to fit the wearer perfectly, and they say the fit is good enough for use in highly mobile body regions, including shoulders.
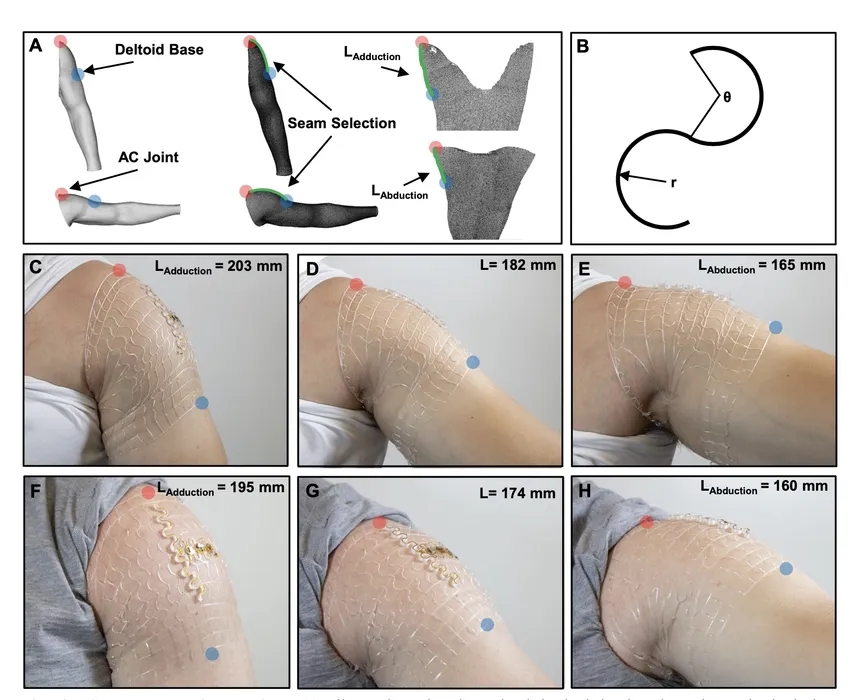
The geometry developed has issues similar to that encountered in the fashion industry: seams, flex points and more must be identified and accounted for in the design.
The biggest benefit is that the approach allows not only a custom fit, but also custom design for the sensors. If sensors are best placed in a very specific surface area, the print geometry can be designed around that requirement. This could lead to improved signal levels.
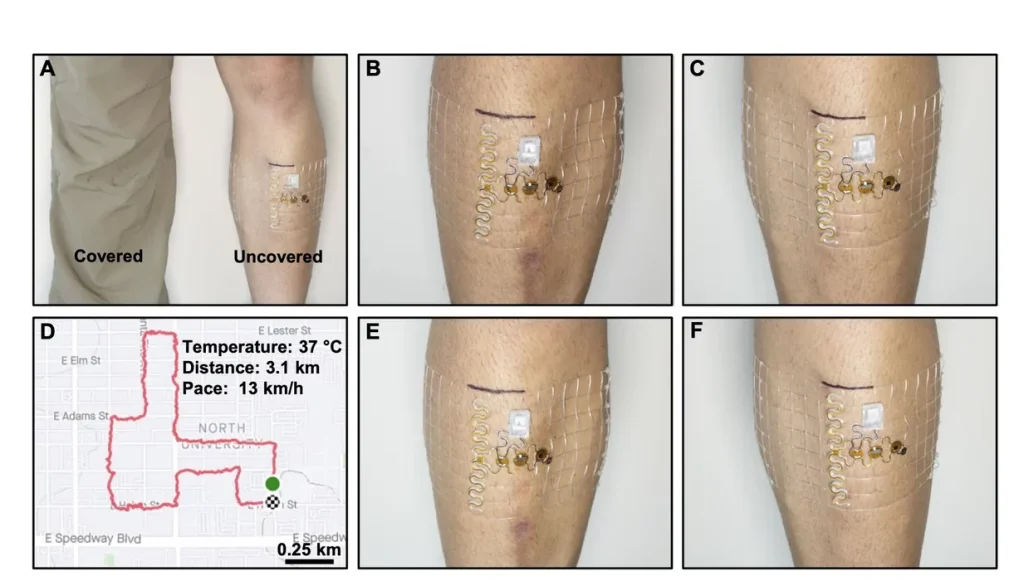
The result is a 3D printed sensor that a patient can wear with nearly no physical interference. The patient can proceed as normal without any worry about the sensor: itās even waterproof!
It seems to me that this process could be a relatively inexpensive to produce extremely effective medical sensors, and therefore itās likely this approach will soon make its way to commercialization.
Via Science