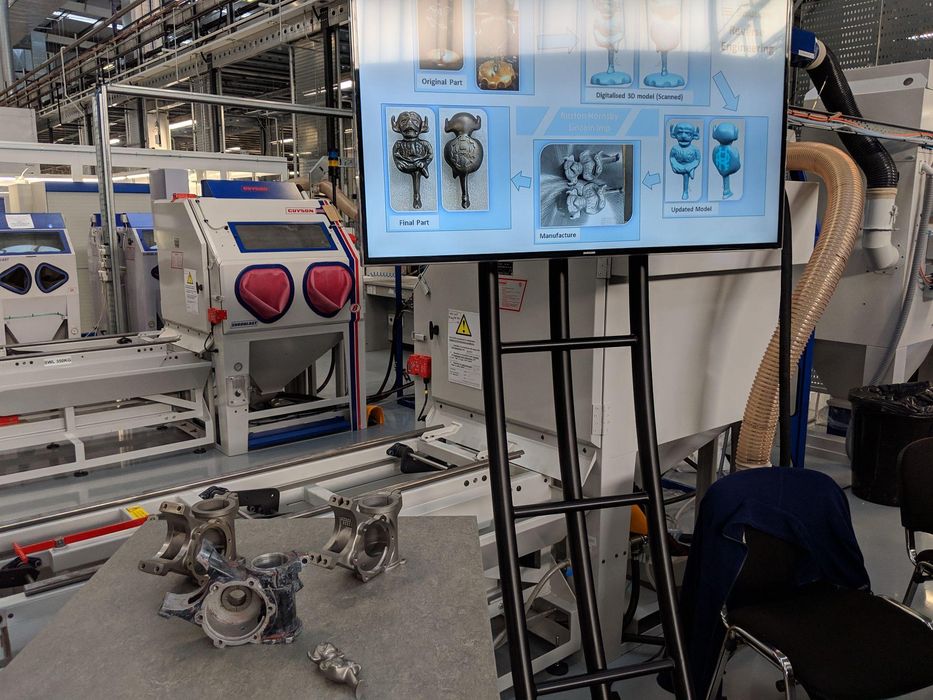
From custom cup holders to spare parts, additive manufacturing is changing the aftermarket for car parts.
The automotive aftermarket is a massive quagmire of original equipment manufacturer (OEM), off-the-shelf, and cobbled-together parts used to repair or replace the parts that keep vehicles moving.
While ancillary aftermarket parts ā think cup holders, personalization details, or other more aesthetic features ā have been a hotspot for 3D printing, thereās a huge potential market for more practical parts where on-demand manufacturing and digital warehousing can offer incredible benefits. Indeed, additive manufacturing (AM) is changing the aftermarket for car parts.
From digital inventories of spare and replacement parts to reverse engineering of obsolete parts to tooling to ā yes ā the fun things to personalize vehicles, AM in the automotive aftermarket is abuzz with possibility.
Digital Inventory
Grills, valves, even engine components: Imagine not worrying about stock, even for long out-of-production vehicles or those so popular even spare parts fly off shelves. What if there were no shelves, no warehouses, no superstores to worry about, and instead a quick online order form? Thatās both a near-future and current reality, ready to scale up for more aftermarket suppliers.
Especially for rarely-replaced parts or for shorter-run production vehicles, it simply doesnāt always make sense to keep physical parts on shelves gathering dust. Producing them using the original manufacturing method is rarely cost-effective, since tools and molds may no longer be available. However, if digital files are available, additive manufacturing can relatively quickly turn those virtual parts into physical replacements.
With many automotive OEMS, from Ford to General Motors to BMW, having invested in 3D printing for decades now ā often as a āsecret sauceā and only somewhat recently publicly sharing a glimpse into their applications ā more and more manufacturers are producing digital twins as part of their standard operating procedures. That leaves them one print job away from offering any spare part on demand. Building such a process into design and production eliminates those physical inventory shelves from the get-go.
Similarly, vehicle manufacturers can add higher-end touches with on-demand components. Prefer a metal shifter to a standard polymer version? At IMTS 2018, HP showed just what its Metal Jet technology could do with a Volkswagen shifter.
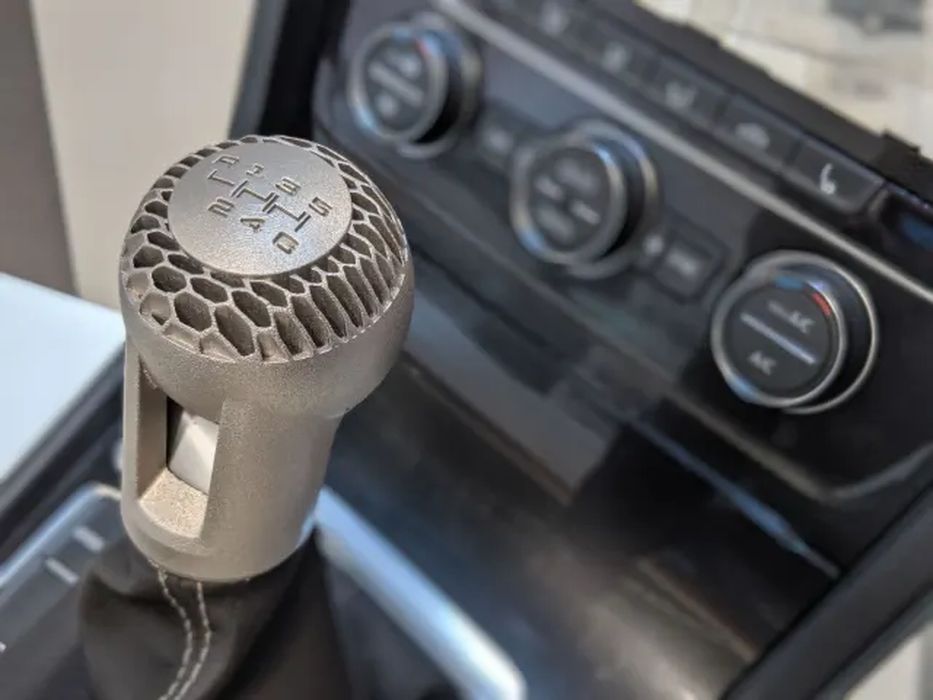
From specialized nuts and bolts to dashboard components and under-the-hood parts, polymer and metal 3D printing technologies are rising to the challenge of road-worthy parts production.
Reverse Engineering
Out-of-production reproduction came to prominence relatively early on in the discussion of additive manufacturing for the automotive aftermarket.
Typically, parts are made in significant quantities for automotive manufacture, with thousands or millions of components assembled to create each run of vehicles. This keeps traditional manufacturing ā think molding, casting, milling ā busy and cost-effective.
But when those vehicles go out of production and itās been long enough that their spare parts are nowhere to be found, what options do owners have? If a given part is the difference between junking a car and keeping an oldie-but-goodie on the roads, it seems silly to bid farewell when that part could be reverse engineered.
In these processes, engineers need to create a new digital file. This often involves taking a detailed 3D scan of a legacy part, repairing as necessary within the software suite of choice, and then generating a printable file.
From there, itās just a matter of selecting the right 3D printing process and material of choice to create the needed parts. That oldie-but-goodie will be road-ready again before a traditional line might even start prepping an outdated mold.
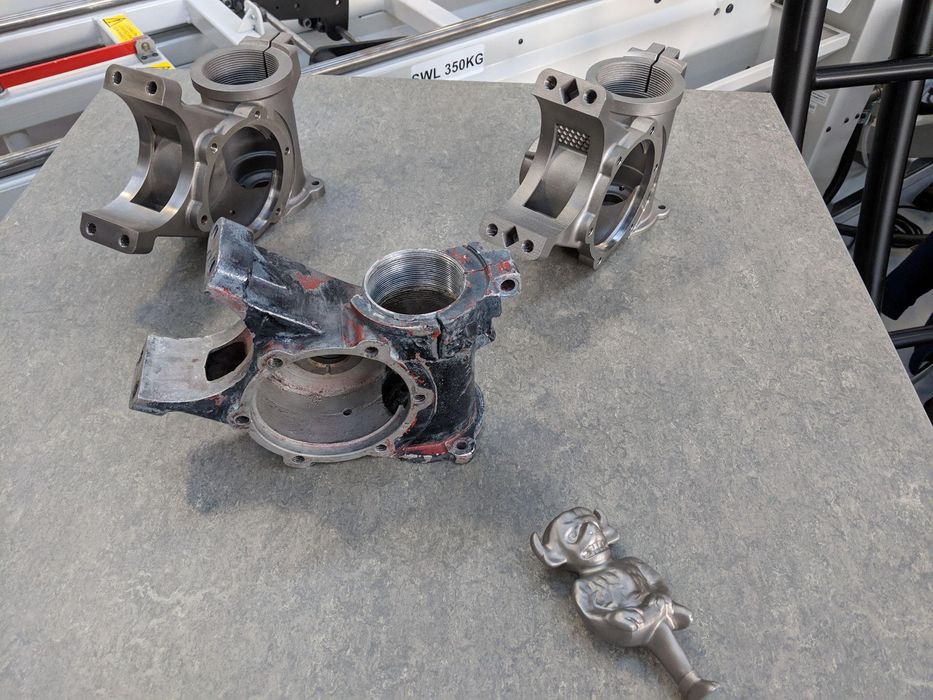
Siemensā Materials Solutions facility in Worcester, England had examples cases like this on a media tour some years ago. There, Engineering.com was among the welcomed guests to see how the in-house team reverse engineered a classic Ruston Hornsby. I had the opportunity to join that event while working with Fabbaloo, getting a close ā in-vehicle ā experience with the Ruston Hornsby.
Hands-on, the vehicle was looking as good as new, with steering box components and even its classic hood ornament recreated via reverse engineering and additive manufacturing.
Read the rest of this story at ENGINEERING.com