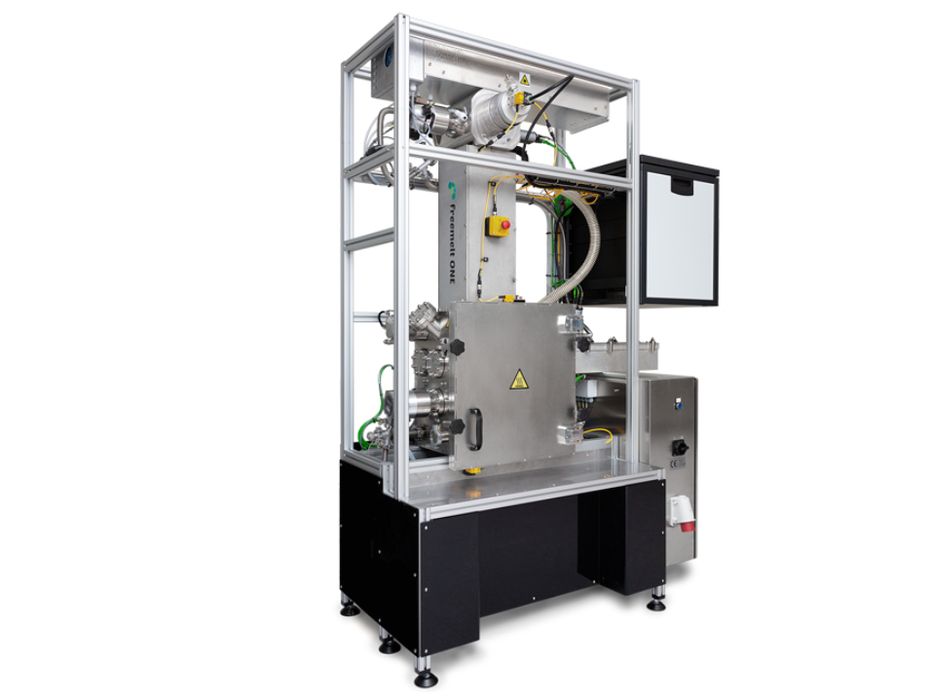
Freemelt is a Swedish company offering an unusual electron beam metal 3D printing system.
I had not heard of the company until recently, likely due to the pandemic. I decided to take a bit of a dive into their material to find out what theyāre all about.
They launched in 2017 with intentions of building a kind of open source metal 3D printer. It seems theyāve achieved part of that goal, but letās take a look at their system.
The lone machine in their product catalog is the Freemelt One, billed as a āmaterials development 3D printerā. In other words, this device is targeted at researchers looking to test new metal powders in the most efficient manner.
This application is mostly due to the rather small build volume of the Freemelt One, which happens to be only 100 mm diameter by 100 mm tall (it uses a cylindrical build volume).
This build volume is vastly smaller than many other metal 3D printers on the market, so thereās no intent to compete with them. However, this build volume provides an incredible advantage when working with small samples of powder: you have only a very small build volume to fill.
Consider the situation if youāre developing a new metal alloy for 3D printing. You have twelve different combinations to test, but most production metal 3D printers you would have to supply more powder to operate the devices. Thatās not desirable when you are iterating through a sequence of different alloys.
One interesting feature of the Freemelt One is that instead of safely removing oxygen from the build chamber by means of purging with an inert gas such as nitrogen or argon as is done with most other metal 3D printers, the Freemelt One instead uses a vacuum chamber. This approach reduces the pressure inside the small build chamber to only 10-6 hPa (mbar). This removes not only the oxygen, but also water vapor and other potential airborne contaminants. Freemelt said the chamber can be evacuated to operating pressure in less than 15 minutes.
The electron beam in the Freemelt One is able to deliver variable amounts of energy from zero to 6kW to the entire build surface, and the company said this can be done with āconsistent beam spot quality.ā Temperatures can reach an astounding 1200C during operation.
Curiously, the Freemelt One, if you hadnāt noticed, doesnāt seem to have an exterior casing. Itās simply a frame, and thatās done purposely. This allows researchers easy access to all elements of the machine, because the device is designed to encourage tweaking.
Along the same lines, the recoater blade and mechanism can be modified and optimized for specific materials. Interestingly, the blade sits outside the build chamber until called for ā then a sliding door opens to allow the blade into the build chamber for recoating.
Thatās the nature of this machine: itās for research.
This philosophy carries forward into the machineās software, which is provided in open source form (note: I donāt believe the machine itself is open source, but the software apparently is). This allows researchers to dabble not only with the materials, but also with the software that works with the materials.
The Freemelt One is not a machine for commercial use; instead itās designed from ground up as a research device. Those companies and institutions wishing to experiment with new types of metal alloys for additive manufacturing might want to check out this interesting machine.
Via Freemelt