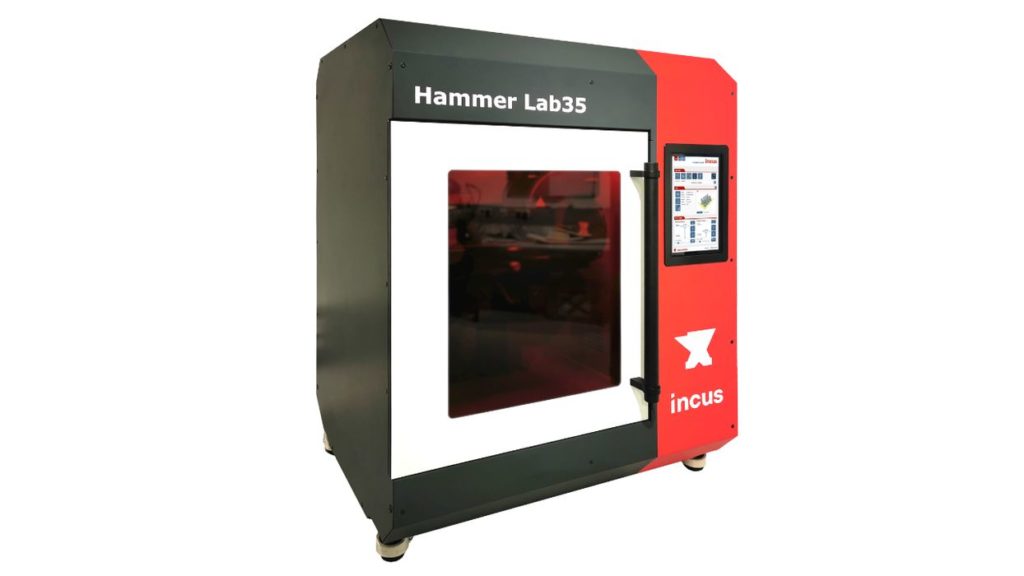
You might not have heard of Incus, a company that’s developed a unique metal 3D printing system.
Vienna-based Incus has an interesting history. Evidently their base 3D printing process was invented at TU Wien way back in 2006. Initially, the technology was used to 3D print ceramic parts, and from that was born Lithoz, a familiar name in the 3D print world. Since then, Lithoz has produced a number of machines capable of printing high resolution ceramic parts.
However, behind the scenes this research led to the formation of Incus in 2019, which adapted the technology to be used with metal materials.
Their process is called Lithography-based Metal Manufacturing, or, “LMM”. It uses a liquid polymer solution containing metal particles. These proprietary fluids can contain up to 60% weight of metal particles.
This solution is selectively deposited, layer-by-layer to gradually form an object. Of course, it’s not quite a solid, finished object at that point. It’s a “green” part that must then undergo binder removal and sintering to fuse the metal particles together. Here you can see the entire LMM process:

Incus said they can handle a wide variety of metals, including some that cannot easily be 3D printed using more commonly available metal 3D printing processes, such as copper.
The LMM technology is bundled into a product offering, the Hammer Lab35 machine. This is a metal 3D printer that has a build volume of 89.5 x 56 x 120 mm. This is quite small, but more than sufficient to 3D print the extremely detailed objects that LMM is capable of producing.
Using a 2560 x 1600 pixel UV light engine, they are able to solidify voxels 0.035mm on a side. That enables the very fine resolution on this device.
Print speed is rapid because each layer is processed simultaneously, unlike PBF laser systems where the laser dot must traverse each solid portion of the print surface. Incus claims a print speed of “up to 250 slices per hour”, where slices range from 0.01 to 0.10 mm in height. In other words, their maximum print speed could be as high as 25 mm per hour.
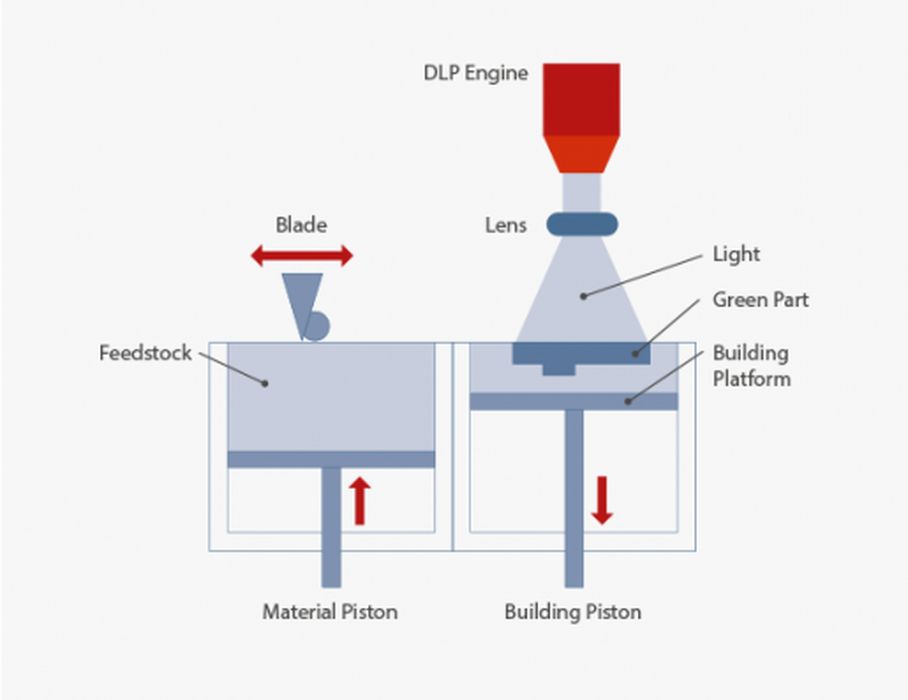
One interesting advantage of LMM is that it does not require support material, unlike most metal 3D printing processes. This is because the material used provides inherent support all around the object. This makes it entirely possible to easily 3D print very complex geometries on the Hammer Lab35.
Incus appears to be targeting the MIM (metal injection molding) industry with LMM technology, as that industry is already familiar with the multi-step process involved, and would simply need to add the LMM printing step into their existing procedures. LMM also provides the ability to handle many different metal materials, although it appears that you must purchase the proprietary liquid from Incus. They explain their materials strategy:
“The LMM feedstock is a proprietary blend of photo-reactive resins and metal powders up to a solid loading of 60 Vol% (depending on the powder). This composition allows for a wide range of metals to be processed, from iron-based alloys to titanium, copper, precious metals and hard metals. The Incus technology can process the widest range of metals compared to other metal AM processes on the market. Each feedstock offered is tailored to perfectly suit Incus’ technology and to facilitate the production of high-quality parts for the desired application of the customer, i.e. Incus sells the feedstock and serves as a partner in customized material development and innovation studies.”
It appears that Incus is ready to accept requests for any reasonable material, whereupon they will quickly develop an appropriate custom liquid material for the job.
At this time, it seems to me that Incus is targeting metal producers with technology that allows them to more easily produce highly complex small metal objects that would otherwise be impossible to create using traditional molding approaches. This could be a very welcome capability, so we may see Incus grow their business in coming years.
Via Incus