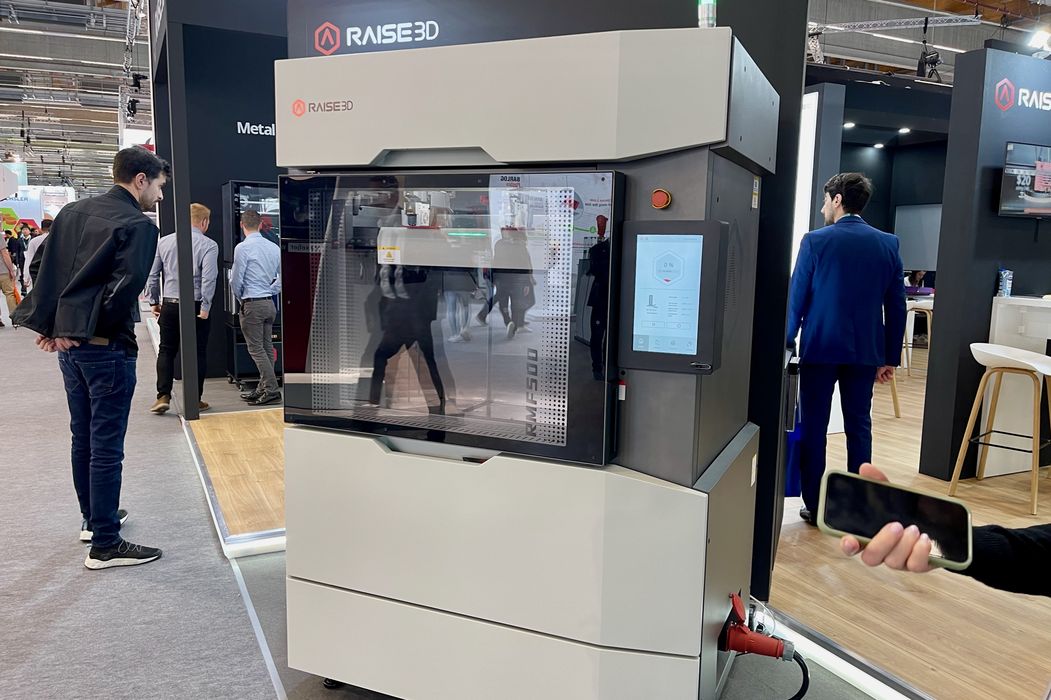
We had a look at Raise3D’s RMF500 3D printer.
This is the largest 3D printer made by Raise3D, which began operations marketing much smaller desktop devices. They still do that, although the current models are far more powerful than their predecessors.
The RMF500 boasts a ridiculously large build volume of, you guessed it, 500 x 500 x 500 mm. This makes it not quite a large format machine, but it’s getting pretty close.
The IDEX print speed is also ridiculous, at up to 500mm/s, with 15000mm/s/s acceleration. There’s also closed loop control for extreme accuracy. They say the XY resolution is a mere 0.001mm, and the Z resolution is 0.0009765mm. That’s pretty tight!
What’s most interesting about this device is that it can handle a wide range of engineering materials. This is due to the 330C hot end temperature and 110C build plate temperature.
Raise3D has quite a long list of unusual materials that can be printed on the RMF500, including PLA, ABS, PA12, PPA, PET, PETG, PVA+, TPU, ASA, and PC, with several CF and GF variants. These materials are sold by Raise3D and certified for use.
The company also has an open materials program, where any filament can be used. While operators can tweak the settings to use literally any filament, the open materials program lists filaments from manufacturers that have had their products certified on the RMF500. As of this writing there are no less than 50 producers on Raise3D’s list, with perhaps close to 200 filament options.
Regardless of which filament is used, the RMF500 has a very unusual spooling system. There are four bays for spools, and the intent is to provide redundancy. Typically there would be two spools of model material, and two of support material. When one runs out, the RMF500 automatically switches to the secondary spool and alerts the operator. This means the RMF500 can operate continuously, as long as the operator keeps feeding in spools.
There’s another unique feature of their spooling system. Many of the engineering materials require drying for optimal use, and in most systems that’s done in two ways. One way is to use an external “dry box” to pre-dry the materials before printing, and the second approach is to integrate the dry box into the 3D printer itself.
Both of these approaches are somewhat expensive, because there is heating involved. However, Raise3D’s approach is entirely different.
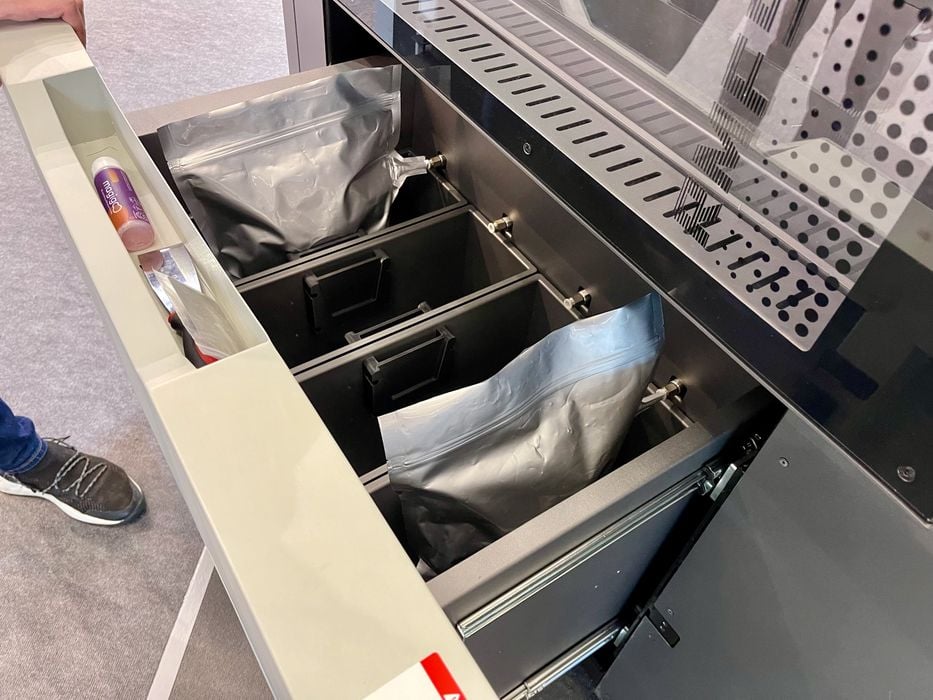
In their spool bays they offer “dry bags”. These are empty sealable bags where the spools can be placed during printing.
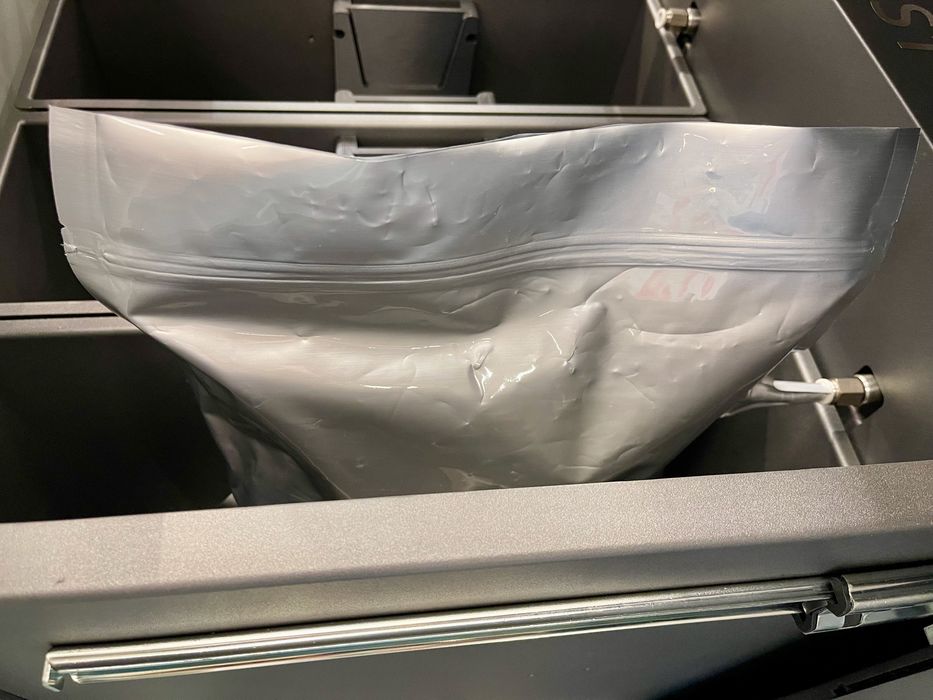
There is a small outlet through which filament can be smoothly fed during printing, as the spools remain in the bags throughout the job. Inside the bags is desiccant, which dries out the filament.
This approach is quite inexpensive and lowers the cost of operating the RMF500 somewhat.
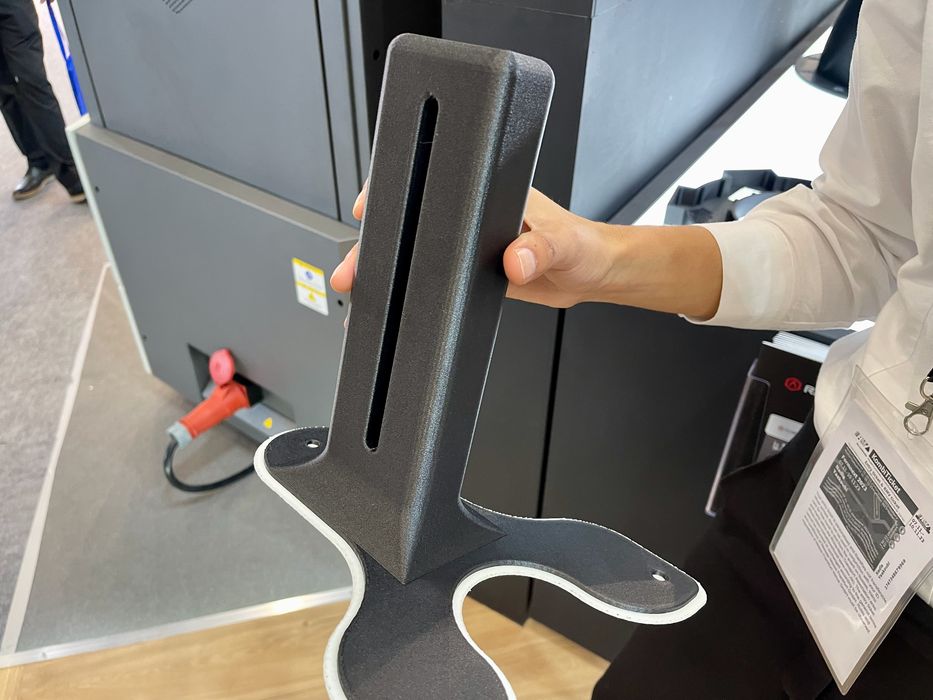
Finally, the RMF500 is set up to use Raise3D’s MetalFuse feature. This is a way to produce metal objects using an FFF 3D printer. It’s done using specialized BASF filament that has a high ratio of metal particles, such as 316L stainless steel.
The prints are producing using a specialized version of Raise3D’s IdeaMaker software, and then printed in the usual manner. This produces a “green” part that must undergo debinding and then sintering to create the final part.
While the RMF500 can’t do those steps, the system is designed to be fully compatible with standard MIM (metal injection molding) equipment. In other words, there are plenty of local services that can perform the final steps for anyone operating a RMF500 3D printer with MetalFuse.
Via Raise3D