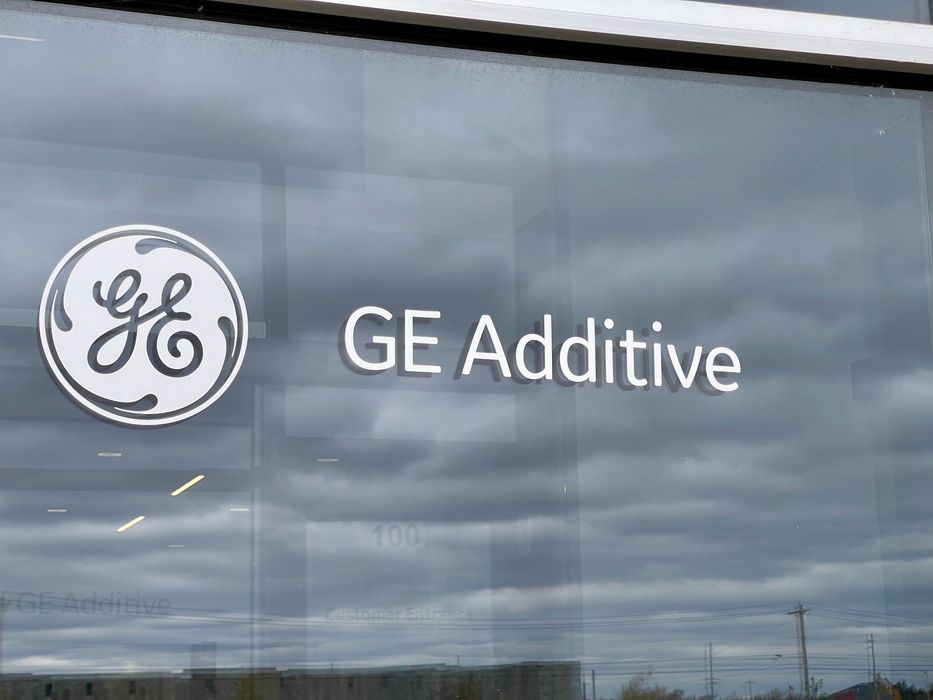
This week GE Additive announced a very different 3D printer that could dramatically change manufacturing.
At first glance, the Series 3 would appear to be “another binder jet 3D printer”, and while that’s basically true, there is a lot more to the story. Yesterday we published a short overview of the Series 3, which you may want to read before going further.
I had a behind-the-scenes look at the new device this week at GE Additives HQ just north of Cincinnati. I should stop calling the Series 3 a “printer” because it’s really a system composed of multiple parts.
There is a 3D printer, of course, but it’s actually not the center of the action. The real activity is sourced from the Material Handling Systems, one for powder and one for liquids. These act as “hubs” for a cluster of Series 3 printers that are periodically fed consumables automatically.
GE Additive’s vision here is breathtaking: they have designed the entire Series 3 system from top to bottom to be for factory use. This is quite different from other “industrial” 3D printers that are essentially standalone 3D printers with a few features that might be useful in a factory.
Here GE Additive has ensured the entire system as a whole is compliant with factory practices and protocols. In addition, they’ve taken a number steps to reduce operational and consumable costs, which when amplified by cluster scaling, will be significant.
For example, the entire system is automated — completely automated — except for these operator activities:
- Roll drums of fresh powder & liquids to the MHS units
- Remove liquid waste drums
- Remove & Depowder parts
That last step is also being deeply investigated to discover the best way to provide further automation. However, everything else seems to be automatic, just like a factory would want. Prints are dispatched and run; material is automatically supplied to printers as required; completed build boxes can even be routed along conveyor belts to post processing stations. There’s just not a lot for an operator to do, other than make sure it’s all running.
Even the maintenance of the Series 3 is easy: they’ve designed the system to be very modular, so that if one component fails, a factory operator could quickly swap in a spare and keep the line going.
GE Additive representatives hadn’t yet figured out how many machines could be supported by a single operator, but it’s certainly going to be a large number.
The result of this is high quality metal parts 3D printed at low cost. I was shown a complex metal demonstration part about the size of a fist, and was told the cost to produce it was about US$35, as opposed to the hundreds of dollars it would take to produce a similar part using traditional LPBF methods. That said, LPBF can produce much more complex geometries than the Series 3 can; the Series 3 is for a different market.
How did GE Additive get here? It seems they first started thinking about solving the manufacturing problem way back in 2016, when they started working on binder chemistry. This apparently took quite a while to figure out, and the results are startling: green parts are incredibly tough, making the Series 3 able to print complex objects without fear of them breaking before sintering.
GE Additive then iterated through a series of versions of the machine, ending up with, you guessed it, Series 3. That’s the first version ready for general customer use.
While GE was one of the pioneers in “turning” aerospace onto metal 3D printing, the Series 3 isn’t actually targeted at those applications. Instead it’s focused on a new market (which may include aerospace, automotive and healthcare) that is currently unable to afford the high costs of LPBF metal 3D printing.
These would include all kinds of metal foundries producing lower-cost parts for industry and consumer use. Existing metal 3D print solutions really weren’t appropriate for such implementations because of two factors:
The cost to make the parts exceeds what part buyers would be willing to pay
The system is too much trouble to setup and scale at a factory because it’s too “standalone”
GE Additive has breached both of those barriers with the Series 3. The parts are produced quickly, cheaply, with good quality and (mostly) automatically.
It’s not just the hardware, too. For example, the Series 3 is apparently able to directly connect with manufacturing execution systems (MES) and ERP systems to accept print orders.
The Series 3 seems to be “plug in ready” for factories, more than any other metal 3D print option I’ve seen.
There are some major implications here.
One is that GE Additive could break open an enormous metal manufacturing market that up to know has been left to the wayside by conventional metal 3D printing. This is likely a market far larger than today’s metal 3D print market, and would surely generate a metric tonne of revenue for GE Additive.
If that happens, it could also drive strongly increased adoption of 3D printing everywhere. If the technology becomes commonplace at foundries, the knowledge of 3D printing approaches will be more widely used.
Aside: while the Series 3 is a metal 3D printer, the technology and process used in the system is entirely compatible with other powdered materials, including ceramics, composites, polymers and more. I could imagine foundries adding new product lines when they realize what this system can do.
But there’s one more implication that faces GE Additive. Once the system is shown to work, they must then persuade factory operators to adopt it. With all the buzz around the Series 3, you’d think this would be easy, but it won’t be. Existing industrial additive applications were adopted only after years of demonstrations, presentations, special deals, handholding and more. This will have to be done again, this time for yet another group of prospects.
After seeing all this at the factory, I can understand GE Additive’s vision: very large factories with multiple clusters of Series 3 (or successor machines) being continuously fed consumables and automatically producing thousands and thousands of metal parts.
That’s how 3D printing will eventually reach mass manufacturing levels.
Via GE Additive