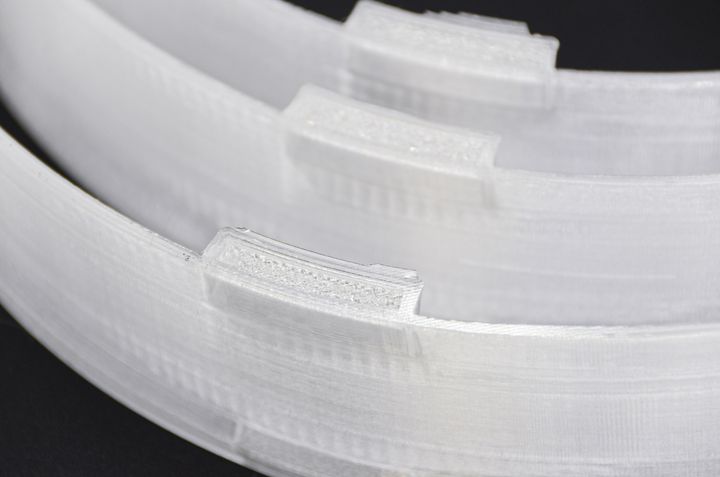
I had a discussion with the techs at 3DQue and discovered they have found a way to 3D print many different engineering materials at very low cost.
3DQue Background
If youāre not familiar with 3DQue, they are a Vancouver-based startup that is developing an automation system for 3D printing. The foundation of their technology is a magic print surface called āVAAPRā that somehow locks onto the print when heated, and releases it when cooled.
Theyāve leveraged this capability into an automation concept where they tip the 3D printers on a side so that prints literally fall off when the bed cools. Arranging machines of this type in an array, they have made a continuously-operating 3D printing factory. Currently they have several units at customer sites.
3DQue Looping Kit
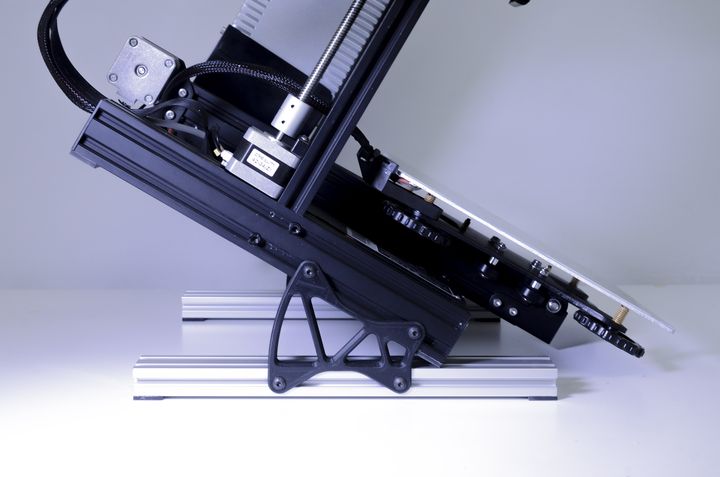
Thatās the industrial angle, but the company has also been recently exploring the use of their technology for more casual 3D printing. A few weeks ago they launched a beta test program for their āLooping Kitā, a.k.a Quinly, which initially equips a standard Creality Ender 3 3D printer with their amazing print surface. It also tips the machine at a 45 degree angle to allow for automated release of completed prints. Theyāre looking to create additional conversion kits for other popular 3D printers.
In discussions with company representatives, it turns out they have been performing a number of highly unusual experiments with this configuration. The idea is that the VAAPR print surface can adhere to more materials than those commonly used on the Ender 3.
3D Print Engineering Materials on Ender
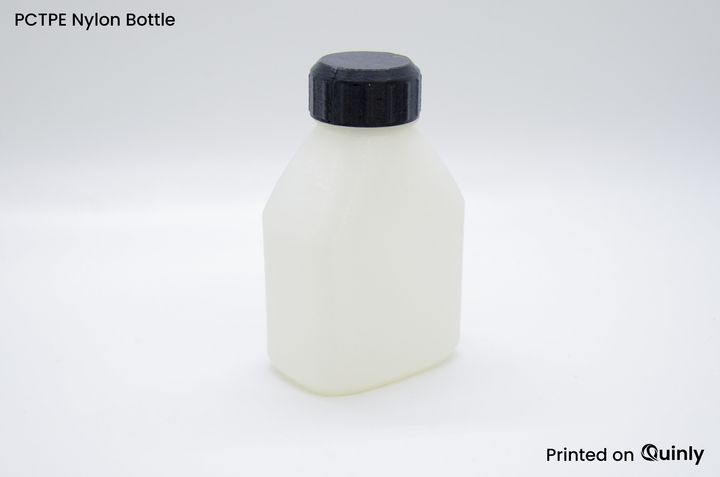
They asked themselves the question, āIf thatās the case, then what materials could we successfully 3D print on the Quinly Ender?ā
One of their techs has been performing these experiments for several weeks and has come up with some surprising results.
The Creality Ender 3 has been designed to 3D print PLA, TPU and PETG, and has internal components to meet those needs. Normally Ender 3 operators are using the device for PLA only. 3DQue quickly realized they had to make some modifications to the stock Ender 3 configuration. Hereās what they changed:
- They replaced the Ender 3ās hot end with a V6 clone (Triangle Labs, US$35). This allowed the use of higher temperatures up to 280C without melting the PTFE tube in the stock Ender 3
- They added some insulation (US$20 for a huge roll of pipe foam) to the bottom of the print bed. This keeps heat from leaking out the bottom and allowed the print surface temperature to rise to 140C
- They added an inexpensive leveling probe because the more extreme temperatures would throw off calibrations
These changes cost them far less than US$100 and are easy to procure and install, making the modified Ender 3 still extremely inexpensive. Of course, the experimental Ender 3 also had their print surface installed.
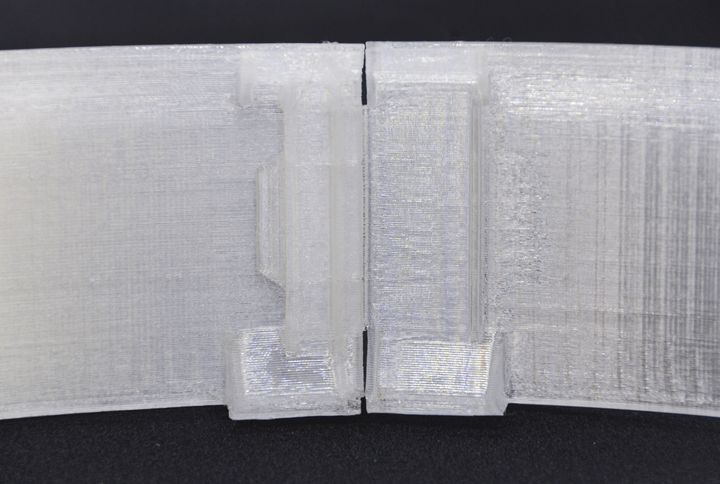
Once all this was configured, they began experimenting with a variety of different 3D print materials. So far, they have successfully tested:
- PLA
- PLA Composites (some are still being tested)
- ABS
- PETG
- Nylon 910 (Small parts work when unenclosed)
- HIPS
- PCTPE Nylon
- Polycarbonate
- Colorfabb NGEN Co-polymers
- TPU
- TPE
Polypropylene was also attempted, and this material stuck very well to their VAAPR print surface. However, as the prints proceeded extreme warping caused the models to tear apart. Whatās very interesting is that the inter-layer adhesion released before the bed adhesion, as you can see in this image:
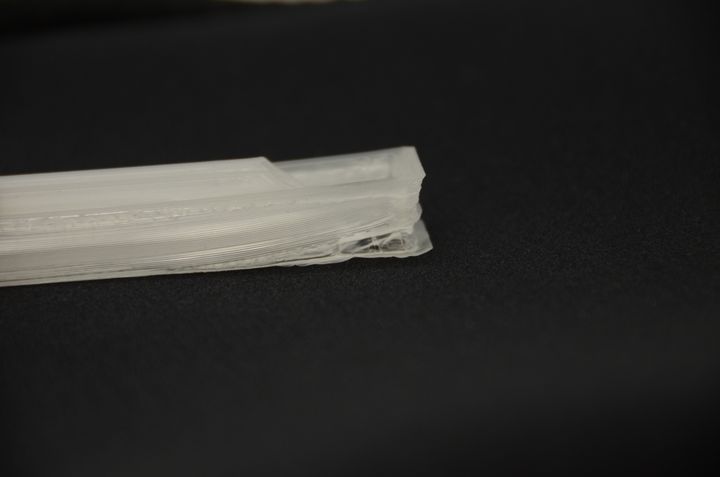
For the working materials 3DQue have developed print profiles that result in high-quality prints that properly adhere and release after printing. However, they discovered a few strange effects along the way.
First, PETG and Copolymers were strange in that they eventually had to create unique print profiles for each vendorās product. It turns out that these materials are more like material families that vary considerably in adhesion properties due to chemistry variances.
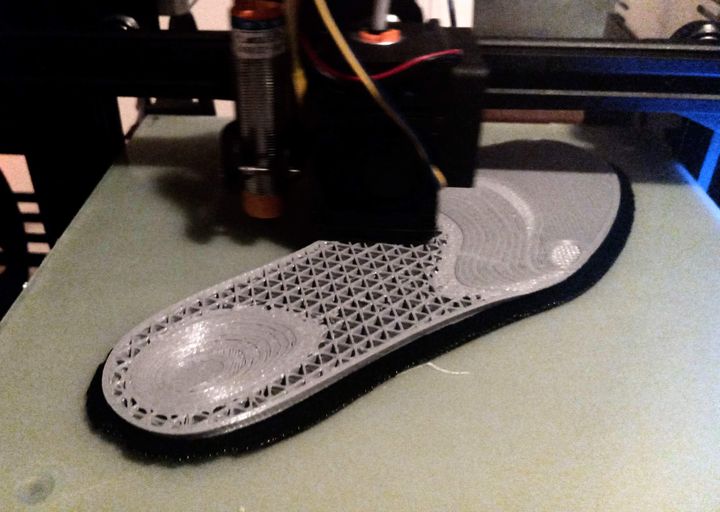
3DQue found that flexible TPU would leave a very small residue on the print surface. This is not surprising, as flexible materials are notoriously hard to 3D print, and thus would be challenging for any automated removal system. However, they have devised an ingenious approach to overcome this effect: 3D print a PLA raft underneath the flexible material, which allows it to easily adhere and release.
3D Print Support Removal Automation
This last point is interesting, as full automation of that concept would require a two-extruder device with both TPU and PLA active during the same job, and the Ender 3 is not that device. It sounds like 3DQue will be exploring dual extrusion in the near future.
That could be a very interesting development, as it would allow for use of soluble support materials like PVA. This means highly complex 3D prints could be successfully completed on a Quinly device. But once they are completed they could be released and fall into a water tub to dissolve support material immediately and completely unattended.
These experiments are extremely interesting as they suggest it would be possible for DIY 3D printer operators to easily configure a 3D printer capable of using engineering materials for only a few hundred dollars that would work for at least some types of small parts. It also means that a 3D printer manufacturer could produce a device of this type more easily than one might think.
However, such a device would likely operate best if using an enclosure to capture stray heat and diminish the thermal gradient during printing. Otherwise there could be warping of larger objects. I wonder if there could be another upgrade kit coming in the future for this?
Iām curious to see how 3DQue leverages these discoveries in their future products.
Via 3DQue