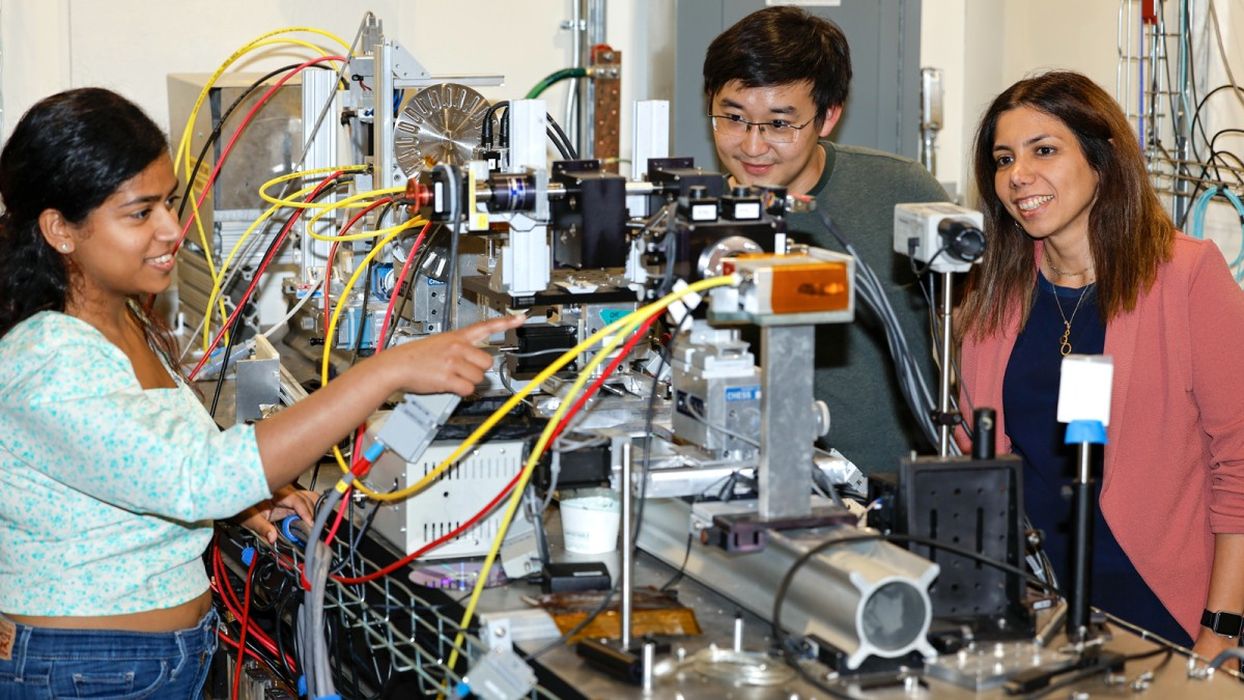
High-energy X-rays shed light on how thermomechanical deformation creates localized microscale phenomena.
Metal additive manufacturing (AM) has many advantages over traditional machining, such as the ability to produce parts with intricate internal features or the potential to lower material costs. However, whether a part is produced additively from metal powder or subtractively from a casting or forging, its underlying microstructure makes a sizeable impact on its performance.
Microstructural issues—such as porosity—can reduce the strength of a part, ultimately leading to unexpected failures. It’s a well-known problem, but such defects are normally only identified once the part has actually been printed. Understanding how the microstructure of a 3D-printed part emerges during the printing process could go a long way to improving additive part performance.
That’s the goal of a team of researchers from the Sibley School of Mechanical and Aerospace Engineering at Cornell University. By bombarding a metal alloy with X-rays while it was being printed, they have uncovered important insights into how its microstructure forms during the AM process. In this case, their focus was on directed energy deposition of the nickel-based superalloy IN625.
In order to access the high-energy X-rays needed for their research, the team constructed a portable 3D-printing setup for testing at the Center for High Energy X-ray Sciences at the Cornell High Energy Synchrotron Source (CHEXS@CHESS). In addition to assisting with the printer setup, CHESS scientists developed safety protocols for operating a high-power laser in conjunction with the flammable metal powder.
The experiment itself involved sending a focused X-ray beam through the IN625 as it was heated, melted and cooled. A detector on the other side of the printer captured the resulting patterns of diffraction.
“The way these diffraction patterns form gives us a lot of information about the structure of the material,” explained Cornell assistant professor Atieh Moridi in a press release. “They are the microstructural fingerprints that capture the history of the material during the processing. Depending on the interaction and what caused it, we get different patterns, and from those patterns, we can back calculate the structure of the material.”
Read the rest of this story at ENGINEERING.com