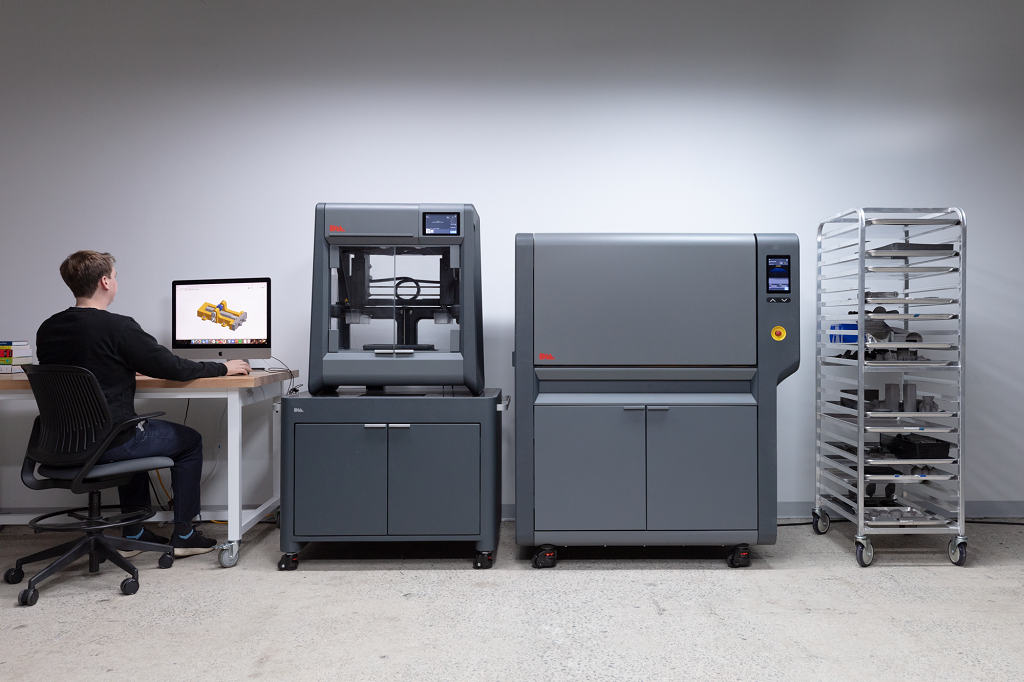
The key word is “easy” for the latest metal 3D printing launch from Desktop Metal.
Studio System 2
In 2017, it was the Studio System. In 2018, it was the Studio System+. Today, Desktop Metal is announcing the Studio System 2.
“The big thing with the Studio system when we originally launched it was all about making low-volume metal parts 3D printing easy and accessible. We had come into the market when all that was available with powder bed fusion. I know the landscape has changed a bit since then, now there are other smaller systems, other solutions in the low-volume metal 3D printing market,” Desktop Metal’s Arjun Aggarwal, VP Product & Business Development told me. “We wanted to introduce a new generation of the technology that brought the ease-of-use of the Studio System to the next step. We’d been spending a lot of time on materials development. One of the things we have in-house is a great materials team, and with their work we realized we could take out a step.”
The Studio System introduced an intriguingly accessible solution for low-volume metal 3D printing: an office-friendly, simple setup. Design a part — and Desktop Metal made that easy too with powerful software introductions — then 3D print it, debind it, and sinter it. Done: easy peasy.
But as with any product introduction, as time goes on, a natural question arises: how could this be better? And Desktop Metal is not a company to shy away from such a question, especially when customers have some ideas. While the debinder and debinding solution “was acceptable around the world,” Aggarwal confided, “some customers had issues”:
“We said, ‘Let’s see if we can make that process practically hands-off and take that middle step out.’ It’s only print and sinter now.”
Two-Step Metal 3D Printing
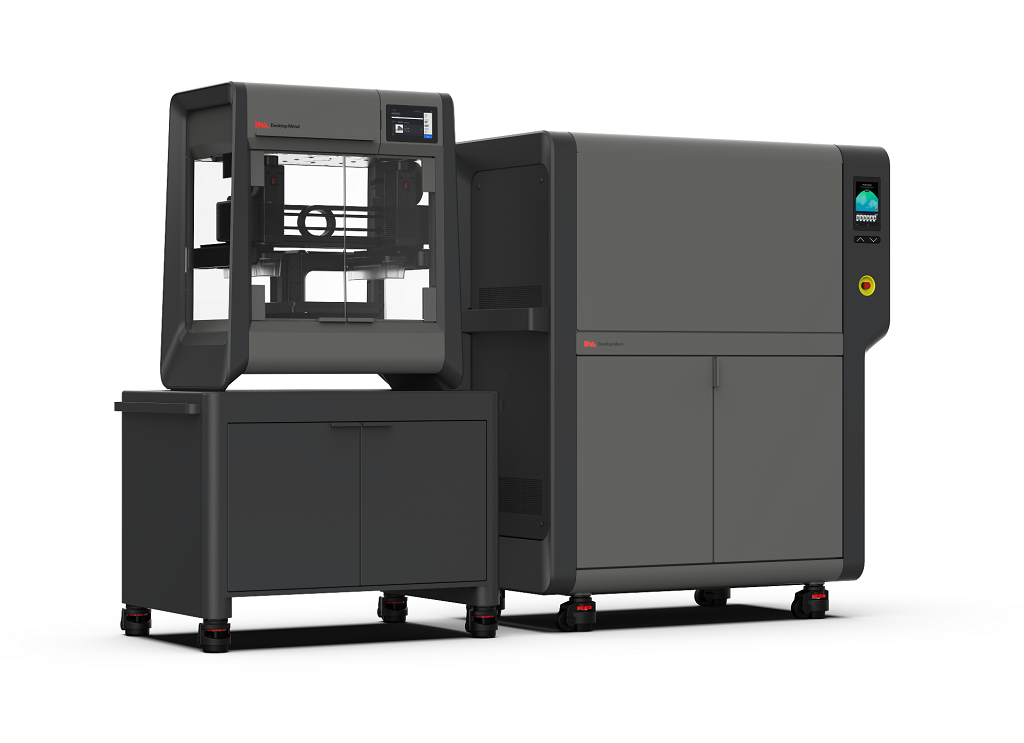
The Studio System 2 does away with the need for a debinding setup. New material formulations debind thermally rather than chemically.
“The new materials system is the backbone of the Studio System 2,” Aggarwal explained. “We started from scratch internally and designed a whole new materials system. There are no loose powders, that’s still a core benefit of the Studio System; we have these rods that encase a mixture of metal powder and binder. We went back to the drawing board, looked at that mixture, looked at each component, and selected new components that would no longer need to have a chemical debind phase. These could instead be broken down during a sintering cycle, in a thermal debinding process. Now what we have is, in our sintering, we pause at a relatively low temperature — compared to the temperature where it sinters — and all the binder in the rods that’s been extruded into the part is basically removed from the part during that debind. Then it elevates up to the sintering temperature.
Desktop Metal’s Fabricate software includes sintering profiles for each material, automating the thermal debinding and sintering processes.
Easier, Better Metal 3D Printing
Along with eliminating an entire third of required steps, the Studio System 2 launch features “a whole host of other features,” as Aggarwal noted.
“There are significant improvements across the board — not only in processes, but parts,” he said. “We have R&D improving profiles for sintering, combined with hardware upgrades in the printer and the furnace, and we’re seeing really improved part quality.”
An eBike motor mount made using the Studio System 2 A close look at support facing surface finish from the Studio System 2
While supports from Desktop Metal parts have always been relatively easy to remove, thanks to their separable support technology, there’s still a difference in surface finish where the supports had been. New updates for the Studio System 2 have led to a “really great surface finish on sidewalls and support-facing surfaces,” which Aggarwal noted is “something our customers have always talked about to us.” Now, he says, the process improvements can “deliver smooth surface finish on the bottoms of parts and minimize stair-stepping on sidewalls.” All told, these enhancements can lead to an uptick in first-time part success — and “allow for a wider set of geometries that can be printed.”
“Designed to consistently deliver high-performance metal parts, Studio System 2 minimizes the trial and error common in alternative 3D printing processes, enabled by new print profiles and a re-engineered interface layer material for more even shrinkage during sintering and increased part success across an array of geometries,” the Desktop Metal announcement notes.
There’s also now a new isotropic triply periodic minimal surface (TPMS) infill to strengthen those complex parts.
The Studio System 2 is launching with 316L stainless steel, with more material options coming this year. Never fear for the immediate, though:
“As we get that new set of materials ramped up, the system will be backwards-compatible with all the legacy materials we’ve introduced. All of these will be available for existing customers who have a debinder, and for new Studio System 2 customers who purchase a debinder,” Aggarwal said.
The three key words for the Studio System 2, says Aggarwal, are accessibility, quality, and reliability.
Those facets come into play as Desktop Metal seeks to make its offerings more appealing to more potential users. Reducing hands-on time, improving the surface finish, improving geometrical possibilities: these are all steps toward “addressing an even wider range of customers with the Studio System,” Aggarwal said.
“One of our core competencies at Desktop Metal is making 3D printing — not just metal 3D printing, now polymer 3D printing as well, with our recent announcement — is to make this technology easy to use and accessible for customers,” Aggarwal told me as we wrapped up our conversation. “That may mean a whole host of different things depending who you are. If you’re printing hundreds of thousands of different parts on the Production System, that’s one thing, but accessibility is also about economics. Can you get the volumes of parts you need? On the lower-volume end of the spectrum, how easy is it for a designer who’s designing the parts to walk over to a system and hit go? Everything we do, from software to hardware to materials, we design with the goal of making it very easy and accessible for the user. I think the Studio System 2 has always been that, improving with this new generation.”
Desktop Metal has been broadening from both “desktop” and “metal” with announcements in large- and mid-volume 3D printing, fiber-reinforced 3D printing, and a company acquisition with polymer 3D printing and bioprinting implications. In a way, it’s refreshing to see a desktop metal-focused announcement from Desktop Metal.
The Studio System 2 is planned for global shipment starting in Q1 2021.
Via Desktop Metal