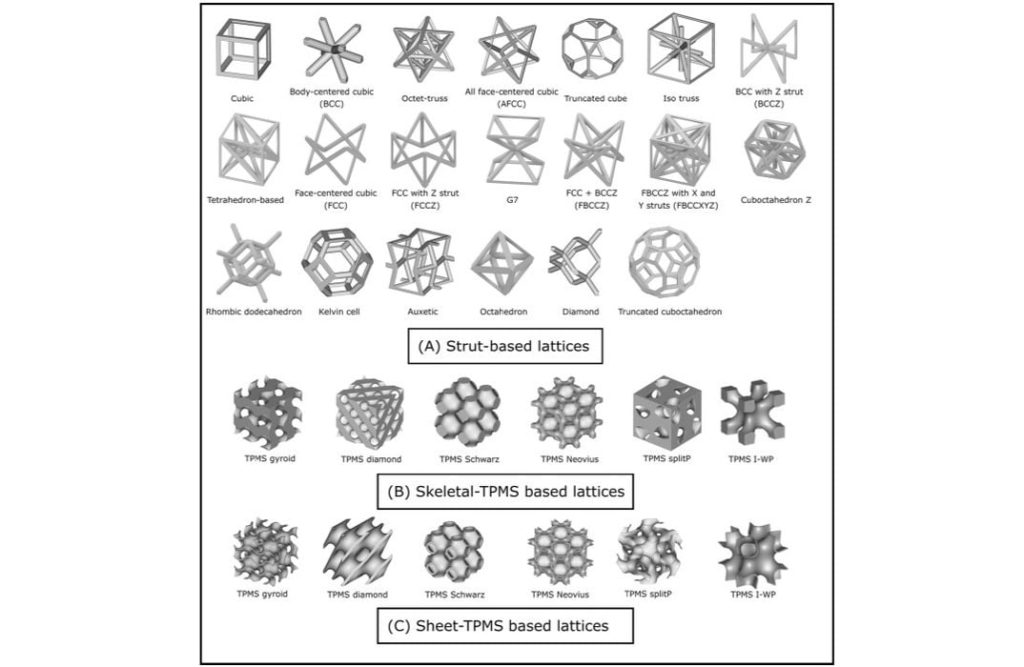
A new research paper investigates the rather long list of applications for 3D printed lattices.
Lattices are complex geometric structures that are sometimes referred to as ācellularā. This is because the geometry of the lattice is sometimes the space not occupied by ācellsā inside of a volume.
In traditional manufacturing lattices are rarely used, except for foams. Foams are indeed a type of lattice, but the issue is that they are generally not controllable and tend to be uniform structure.
With the advent of 3D printing technology it became possible to literally control the lattice design, cell by cell. Sophisticated CAD software is now able to generate complex lattice forms, including for example, lattice gradients, where the cells size varies over a structure.
Some industries have adopted 3D printed lattice structures as a strategic advantage. The most notable has been the footwear industry, where several players are involved in developing highly advanced midsoles. These midsoles are able to optimally transmit energy through ingenious lattice designs, making for shoes seemingly with superpowers.
But what else can you use 3D printed lattices for? Some might be obvious, like lightweighting parts for aerospace, where every gram counts financially. It turns out there are vastly more potential applications.
A new research paper discusses no less than 19 different application areas, many of which I did not realize were possible.
Hereās their list:
- Lightweight Structures (High Specific Stiffness; High Specific Strength)
- Biomedical Implants (Tuned mechanical properties to match bone elastic modulus; Good bone integration, enhanced by appropriate pore size, large surface area, permeability)
- Crashworthiness applications (High energy absorption; Low transmitted stress)
- Vibration Control (High mechanical loss/damping coefficient; High specific natural flexural vibration frequencies)
- Packaging (High Energy Absorption prior to densification)
- Shock Absorption (High Energy Absorption at very high strain rates)
- Ballistics (Low dynamic indentation)
- Electrodes (High Surface/Volume ratio)
- Catalysts (High surface/volume ratio;
- High permeability)
- Heat pipe wicks (High permeability
- High capillary performance)
- Thermal Insulation (Low Thermal Conductivity
- Low Specific Heat )
- Heat Exchanger (High Thermal Diffusivity;
- Low Differential Thermal Expansion ā Expansion limited; High Failure Stress ā Pressure Limited)
- Heat sink (High convective heat transfer; Low thermal resistance)
- Thermal control, hydrogen storage tanks (Controlled thermal conductivity; High surface area)
- Buoyancy (Low Density; Good corrosion resistance)
- Filtration (High Pore Size Control; Adequate Pore Connectivity)
- Acoustic Absorption (High sound-absorption coefficient)
- Soft hinges (Compliant mechanisms)
- Support structures and infill in additive manufacturing processes (Low-density)
This is effectively a list of 3D printing applications, as all 3D printing processes can tackle the geometry required by these applications.
Note that the list talks only about technical mechanisms, and not specific industries. The next step is to match each industry against each of these possible applications to see if there is an advantage to be gained. For example, Iād guess that aerospace would gain from lightweighting, crashworthiness, vibration control, shock absorption, thermal insulation, heat exchanger, buoyancy and more.
Which ones apply to your industry? Time to give this a hard think.
If youād like to learn more about any of these specific applications, I encourage you to read this paper, as it dives deep on each of these topics.
Via Science Direct