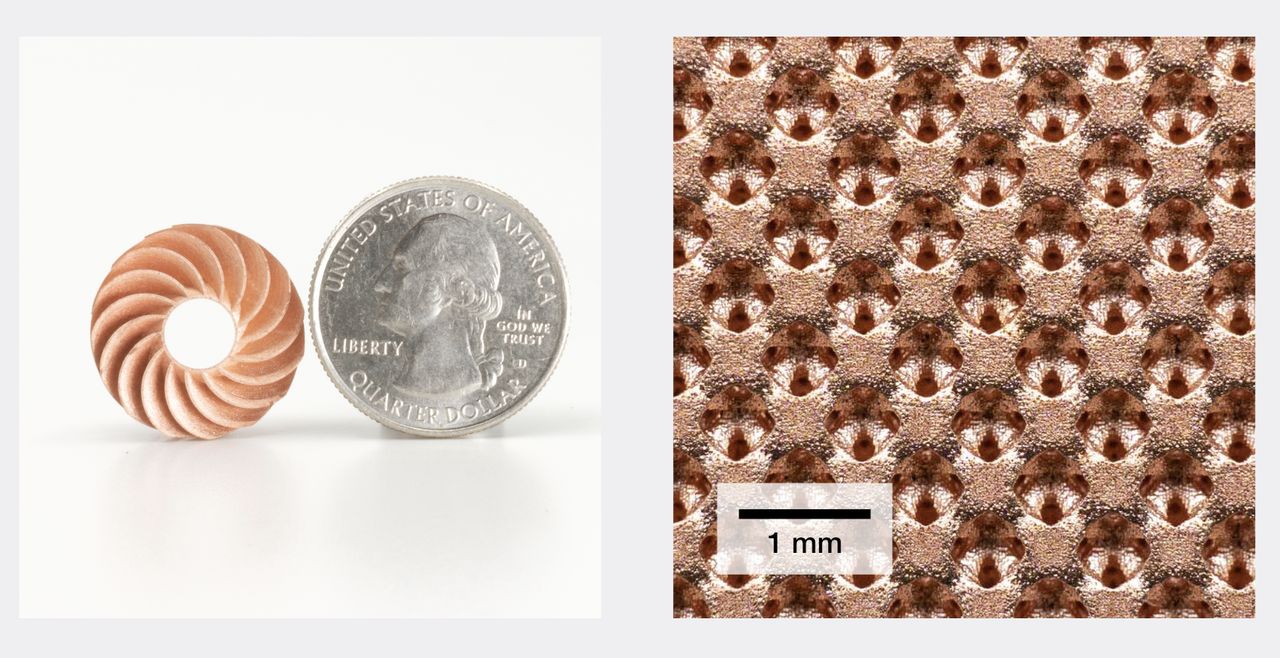
Fabric8Labs has developed a truly unique metal 3D printing process that is unlike all existing processes.
Their process, âECAMâ, does not use powder. It does not use wire. It does not use lasers. It doesnât even involve heat, either during or after 3D printing.
Yet, it can 3D print entirely solid pure metal objects.
How does ECAM work? ECAM stands for âElectro Chemical Additive Manufacturingâ. The first two words give away how this process works: itâs a form of electroplating.
The electroplating process is well-known and actually used frequently to provide a metallic coat to polymer 3D prints. It involves submerging an object in a metal solution and applying an electrical current. The metal atoms then accumulate on one of the electrodes, and form a solid surface.
Fabric8Labs has leveraged the electrochemical process to create a way to 3D print metal objects.
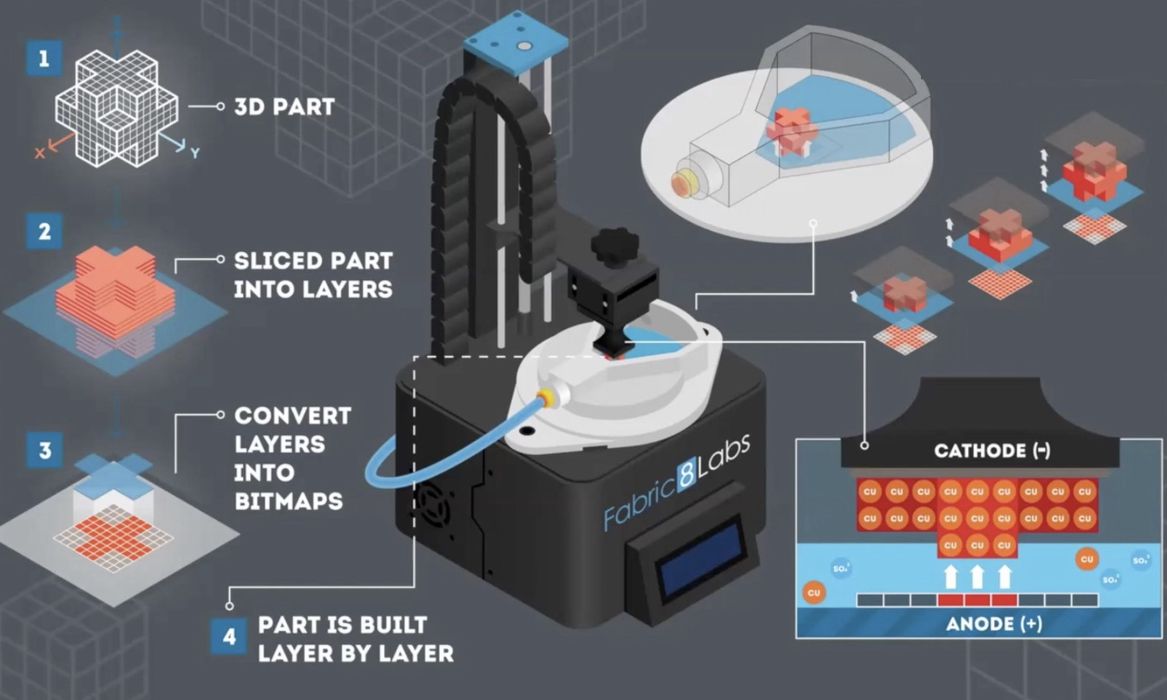
The key to ECAM is a special printhead made of a thin film transistor (TFT) backplane. The TFT backplane is an array of anodes with 50 micron resolution.
The printhead and print plate are immersed in a liquid metal solution containing the target material. The print plate is positioned close to the printhead, which then lights up with electricity â selectively. Only certain âpixelsâ on the printhead array fire, matching to the solid portions of the layer.
The electricity takes the shortest path through the liquid to the corresponding position on the plate. Then the electrochemical effect causes metal to accumulate on that spot. After a short time, the layer is considered complete and the print plate moves slightly further away from the printhead, and the process repeats. The full 3D model is gradually built up, layer by layer.
The process, as you can see, involves no lasers, no heat, no power and no wire. Yet it can make fully solid metal objects.
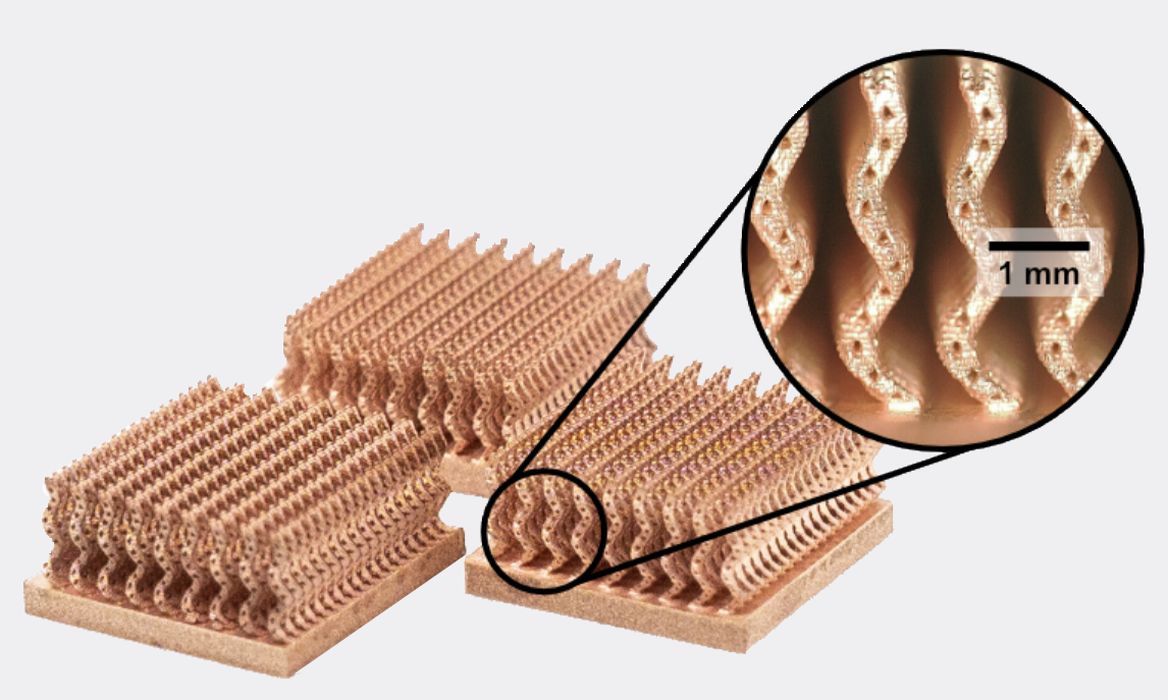
Fabric8Labs is able to 3D print copper and nickel objects, and they are likely able to do even more materials.
The build volume is all about the dimensions of the TFT panel, since the Z-axis can be made as tall as you need. Beginning with a 25 x 25 mm array, Fabric8Labs proved the concept, and then moved on to a 100 x 100 mm array.
They apparently can easily scale ECAM up: the manufacturing of the TFT panels, done by industry partners that make such panels for other consumer applications. Evidently it is straightforward for them to modify their production processes to produce the proprietary ECAM TFT panels. Fabric8Labs has spoken about the possibility of 1000mm panels, which tells you how big ECAM could get.
That doesnât even mention the possibility of moving the printhead in the build chamber. For example, you could print a 1000mm square area, then shift the printhead over 1000mm and do it again. If perfected, this enables the possibility of precision metal 3D printing at almost any scale.
The accuracy of ECAM is impressive. The sample prints shown in this post are all quite small, yet exhibit significant detail. Thatâs due to the 0.05mm resolution of the ECAM TFT panel. This is approximately the same resolution seen in SLA and MLSA systems. Imagine obtaining metal 3D prints with the same quality as a good resin 3D printer!
Finally, with the absence of lasers and heat, ECAM is incredibly energy efficient and therefore highly desirable for our zero CO2 footprint future. Here you can see a comparison chart of the eco-friendliness of common metal 3D printing processes alongside ECAM:
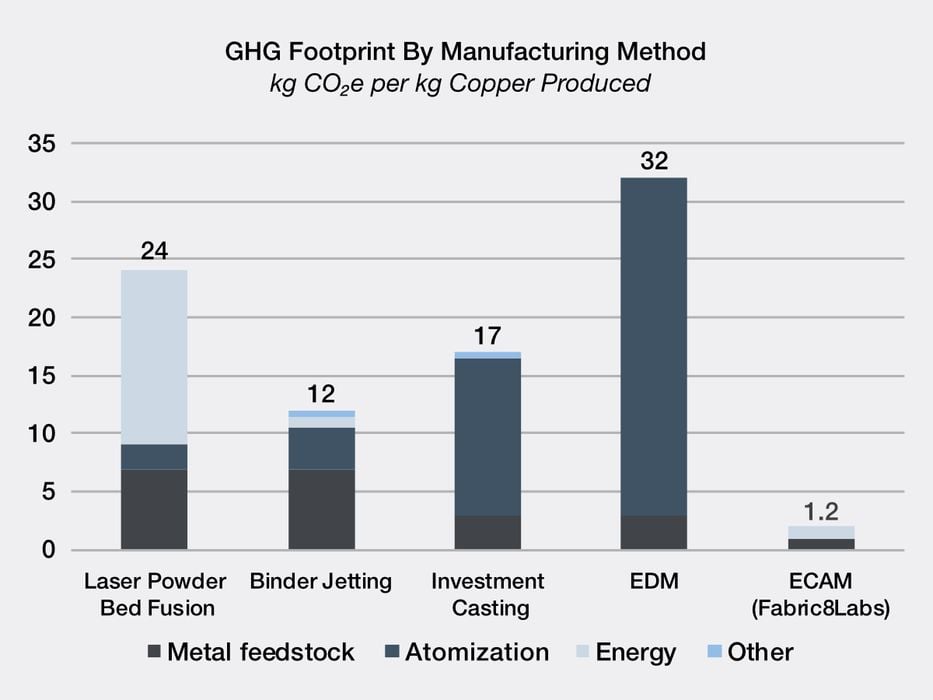
This pitch video explains a great deal about how ECAM works and how the company intends to proceed:
One interesting twist heard in the video is their plan to monetize primarily through the materials. They would supply customers with the proprietary liquid metal fluid to run in the ECAM systems.
Fabric8Labs patented the process in 2015, and only now is beginning to grow. In fact, they recently received a massive US$50M Series B investment. This funding will apparently be used to build a pilot production plant in San Diego.
Thatâs a lot of money, but as you can probably agree that the investors could be on to a big thing with Fabric8Labs and ECAM.
Via Fabric8Labs