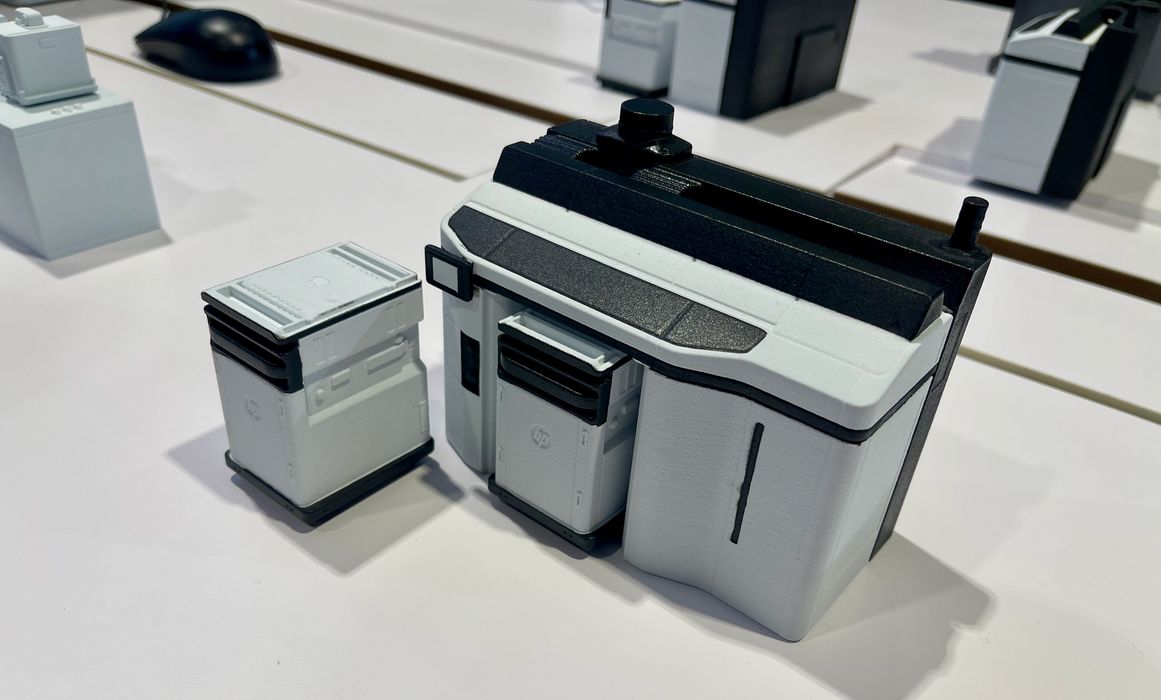
HP seems to be developing a robotic assist solution for their MJF 3D printing systems.
The companyās MJF technology is quite powerful and can produce strong end-use production parts. Indeed, the process lends itself best to production applications, rather than prototyping that dominates much of the 3D printing usage.
Why so? Itās because of the nature of the MJF process.
HP MJF Process
MJF is a relatively straightforward process involving powder and a special ink thatās distributed with rows of high-resolution inkjets. Layers of powder are selectively wet with the ink and stacked upon each other. Eventually you end up with a ābrickā of loose powder with ink distributed inside the the geometry of the 3D model.
At that point the entire build chamber is heated, and the ink absorbs much of the heat, causing the powder itās in contact with to soften and fuse together. This creates the solid print, which can then be extracted from the remaining powder that remains loose.
But thereās a catch: the heat is significant, and with a large build volume it can take considerable time for the chamber to cool down.
HP recognized this early on in development and designed their MJF systems to have a removable build chamber. In this way an operator can pull out a chamber, or as HP calls them āBuild Moduleā, to cool on its own, while installing a second module for subsequent printing.
The time to get a single print is a bit longer, but because of the parallel nature of the MJF design, the system is able to generate considerable parts production throughput over time: the build module is quite large, so each job produces many parts.
This all sounds good until you consider the operational requirements for MJF systems: you must have an operator handy to pull out the build modules and install fresh modules in order to keep up the production throughput.
What happens if the job ends at 2:30 in the morning? I guess you must have someone on duty at that late hour, and that could be a very inefficient way to spend resources if there are not that many swaps taking place overnight.
HP MJF Robot
HP has recognized this issue, as they may have heard comments from prospects about the issue during sales conversations. Theyāre now in the process of developing a solution, which turns out to be a robot.
At top you can see a 3D printed model of their proposed solution: a robotic system that can move build modules on its own.
The idea is that when a job completes, the robot can automatically pull out a build module and relocate it to a place where it can leisurely cool down. It would then locate a fresh build module and slide it into the empty 3D printer, where software can automatically dispatch the next job. No human required!
This would certainly reduce the need for overnight staff, but it turns out there is even more to the story.
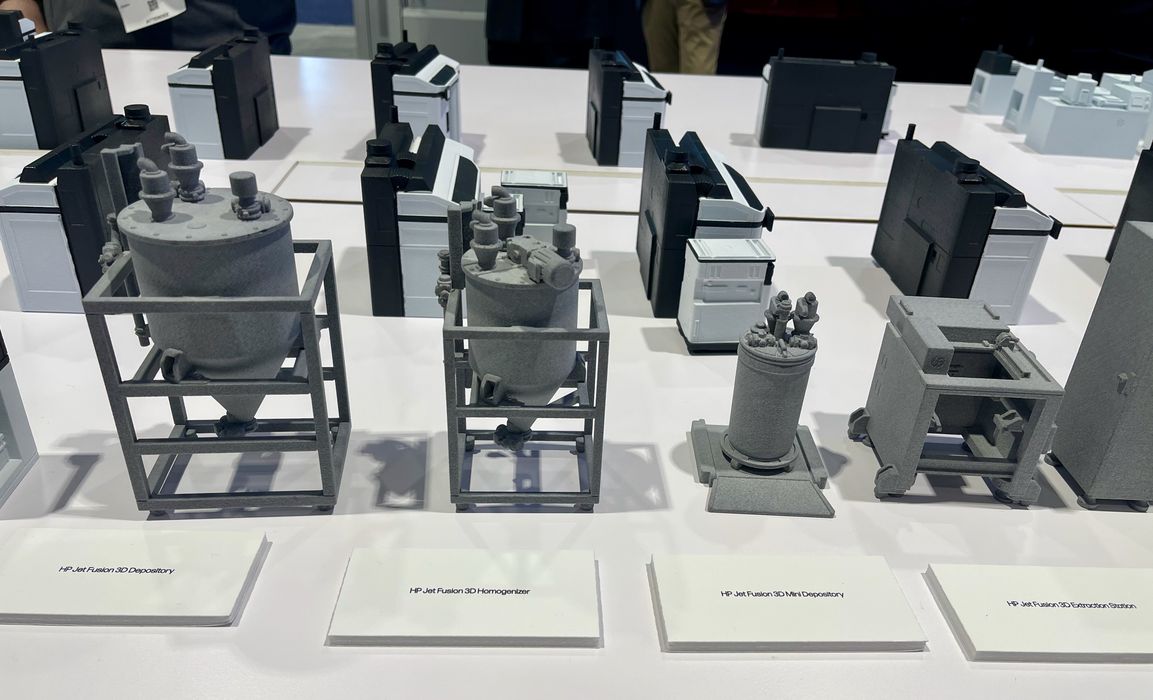
HP is also developing a bulk material distribution system to complement the robot.
Here you can see a 3D printed model of the solution. It involves large hoppers where powder can be stored. These are the components:
- 3D Depository for fresh powder
- 3D Homogenizer (for recombining used powder to the correct ratio?)
- 3D Mini depository (perhaps a small version for smaller operations)
- 3D Extraction Station (for bulk automated powder removal from print jobs)
We were told these components would enable scaling to about 20 MJF devices, and one processing station would handle about three MJF 3D printers.
These components would be combined and be able to refill build modules automatically. Presumably these could then be picked up by the robots to be placed in printers for new jobs. Robots could also drop off cooled build modules at the extraction station for powder removal. Apparently the āunpackingā stage takes only ten minutes and uses a combination of air blasts and agitation to separate powder from parts.
In all, these proposed features should dramatically reduce the labor required to use HP MJF equipment and thus enable expansion of production applications.
Via HP