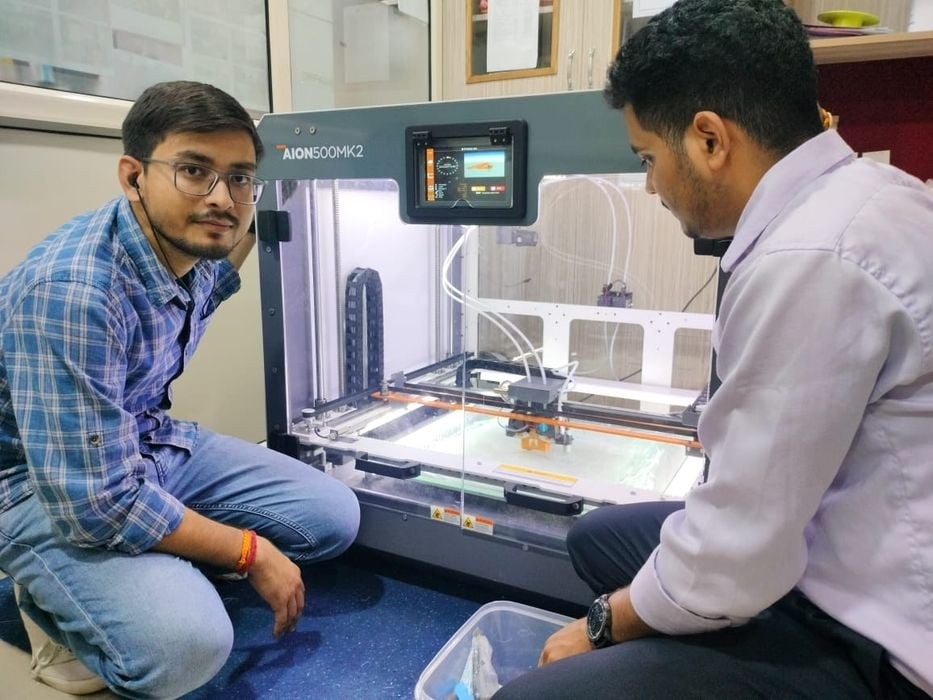
Divide By Zero Technologies has introduced an “auto-switchover” technology in their latest 3D printer, apparently the world’s first.
The Indian company manufactures FFF-style 3D printers for desktop, professional and industrial markets, and has been in business for over ten years. Their product shelf now includes six different models, and they primarily operate in the Indian market.
Their latest release is an updated version of their Aion500 MK2, an industrial model. This device can handle high temperature materials, up to 400C, and sports a unique liquid-cooled extruder. The print surface can reach 150C, far higher than most FFF 3D printers.
It’s also a large machine with a 500 x 500 x 500 mm build volume. It’s completely enclosed, and includes a sophisticated air filtration system.
The Aion500 MK2 includes all the usual FFF features, including networking, automated calibration, swappable nozzles, on board webcam etc.
However, there’s one feature that is of particular interest: Auto-Switchover.
At first I thought this might be a way to automatically change spools, should the first one run out. But that’s not what auto-switchover does.
Auto-switchover is a process that is triggered when a clog or stall is detected in an extruder. This is done, presumably, by monitoring the movement of the filament. If the filament isn’t moving, you have a problem.
Divide By Zero explains how this works:
“Aion 500 MK2 comes with patented precision filament flow sensor that tracks consumption of the material flow through extruder & compares that with the consumption indicated in the G code. In case of clogging, the machine resolves the condition pro-actively by cleaning nozzle automatically.”
It’s then that the Auto-Switchover takes over. The clog detection then automatically switches extruders!
The Aion500 MK2’s second toolhead then takes over for the inoperative toolhead and hopefully completes the print job. This implies, however, that the second extruder is pre-loaded with the same material as the first extruder, preventing this from working when using soluble support material.
Nevertheless, this is a unique reliability feature I have not seen on any other device. It should eliminate the possibility of discovering a failed print in the morning due to a clogged nozzle, also known as “air printing”. The operator would merely get a notice that a clog has to be dealt with after the successful print.
In retrospect I am surprised this hasn’t been done by other manufacturers. The required hardware elements are present on many devices: dual extruders and clog detection. All that’s needed is some firmware changes to invoke the procedure.
I’m hoping that this capability is implemented by more 3D printer manufacturers, as it seems to be a highly desirable feature.
Via Divide By Zero